Giving the driver a quiet
Page 60
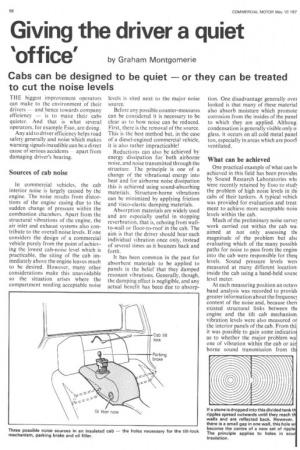
Page 61
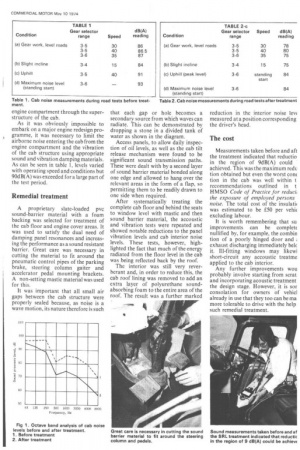
If you've noticed an error in this article please click here to report it so we can fix it.
'office' by Graham Montgomerie
Cabs can be designed to be quiet — or they can be treated to cut the noise levels
THE biggest improvement operators can make to the environment of their drivers — and hence towards company efficiency — is to make their cabs quieter. And that is What several operators, for example Esso, are doing.
Any aid to driver efficiency helps road safety generally and noise which makes warning signals inaudible can be a direct cause of serious accidents — apart from damaging driver's hearing.
Sources of cab noise
In commercial vehicles, the cab interior noise is largely caused by the engine. The noise results from distortions of the engine casing due to the sudden change of pressure within the combustion chambers. Apart from the structural vibrations of the engine, the air inlet and exhaust systems also contribute to the overall noise levels. If one considers the design of a commercial vehicle purely from the point of achieving the lowest cab-noise level which is practicable, the siting of the cab immediately above the engine leaves much to be desired. However, many other considerations make this unavoidable so the situation arises where the compartment needing acceptable noise levels is sited next to the major noise source.
Before any possible counter-measures can be considered it is necessary to be clear as to how noise can be reduced. First, there is the removal of the source. This is the best method but, in the case of a diesel-engined commercial vehicle, it is also rather impracticable!
Reductions can also be achieved by energy dissipation for both airborne noise, and noise transmitted through the structure. The principle is one of a change of the vibrational energy into heat and for airborne noise dissipation this is achieved using sound-absorbing materials. Structure-borne vibrations can be minimized by applying friction and visco-elastic damping materials.
Absorption materials are widely used and are especially useful in stopping reverbration, that is, echoing from wallto-wall or floor-to-roof in the cab. The aim is that the driver should hear each individual vibration once only, instead of several times as it bounces back and forth.
It has been common in the past for absorbent materials to be applied to panels in the belief that they damped resonant vibrations. Generally, though, the damping effect is negligible, and any actual benefit has been due to absorp tion. One disadvantage generally over looked is that many of these material also absorb moisture which promote corrosion from the insides of the panel to which they are applied. Althoug condensation is generally visible only o, glass, it occurs on all cold metal panel too, especially in areas which are poorf ventilated.
What can be achieved
One practical example of what can be achieved in this field has been provide( by Sound Research Laboratories wh( were recently retained by Esso to stud! the problem of high noise levels in the cabs of their tankers. A typical vehicle was provided for evaluation and treat ment to achieve more acceptable noise levels within the cab.
Much of the preliminary noise surve! work carried out within the cab wa: aimed at not only assessing the magnitude of the problem but als( evaluating which of the many possible paths for noise to pass from the engine into the cab were responsible for thes1 levels. Sound pressure levels wen measured at many different location: inside the cab using a hand-held sounc level meter.
At each measuring position an octave band analysis was recorded to provide greater information about the frequenq content of the noise and, because then existed structural links between the engine and the tilt cab mechanism vibration levels were also measured or! the interior panels of the cab. From thil it was possible to gain some indicatio as to whether the major problem wa one of vibration within the cab or air borne sound transmission from th engine compartment through the superstructure of the cab.
As it was obviously impossible to embark on a major engine redesign programme, it was necessary to limit the airborne noise entering the cab from the engine compartment and the vibration of the cab structure using appropriate sound and vibration damping materials. As can be seen in table 1, levels varied with operating speed and conditions but 90dB(A) was exceeded for a large part of the test period.
Remedial treatment
A proprietary slate-loaded pvc sound-barrier material with a foam backing was selected for treatment of the cab floor and engine cover areas. It was used to satisfy the dual need of damping panel resonances and increasing the performance as a sound resistant barrier. Great care was necessary in cutting the material to fit around the pneumatic control pipes of the parking brake, steering column gaiter and accelerator pedal mounting brackets. A non-setting mastic material was used for this.
It was important that all small air gaps between the cab structure were properly sealed because, as noise is a wave motion, its nature therefore is such that each gap or hole becomes a secondary source from which waves can radiate. This can be demonstrated by dropping a stone in a divided tank of water as shown in the diagram.
Access panels, to allow daily inspection of oil levels, as well as the cab tilt release mechanism were found to be significant sound transmission paths. These were dealt with by a second layer of sound barrier material bonded along one edge and allowed to hang over the relevant areas in the form of a flap, so permitting them to be readily drawn to one side when required.
After systematically treating the complete cab floor and behind the seats to window level with mastic and then sound barrier material, the accoustic and vibration tests were repeated and showed notable reductions to the panel vibration levels and cab interior noise levels. These tests, however, highlighted the fact that much of the energy radiated from the floor level in the cab was being reflected back by the roof.
The interior was still very reverberant and, in order to reduce this, the cab roof lining was removed to add an extra layer of polyurethane soundabsorbing foam to the entire area of the roof. The result was a further marked reduction in the interior noise levi measured at a position corresponding the driver's head.
The cost
Measurements taken before and aft the treatment indicated that reductio in the region of 9dB(A) could achieved. This was the maximum redu tion obtained but even the worst con( tion in the cab was well within t recommendations outlined in t H MSO Code of Practice for reduci, the exposure of employed persons noise. The total cost of the insulath was estimated to be £50 per vehi( excluding labour.
It is worth remembering that su. improvements can be complete nullified by, for example, the combin tion of a poorly hinged door and ; exhaust discharging immediately belc it. Ill-fitting windows may likewi short-circuit any accoustic treatme applied to the cab interior.
Any further improvements wou probably involve starting from scrat and incorporating acoustic treatment the design stage, However, it is sor consolation for owners of vehicl already in use that they too can be ma more tolerable to drive with the help such remedial treatment.