A FTER spending three days with the latest KarrierYorkshire combined cesspool
Page 78
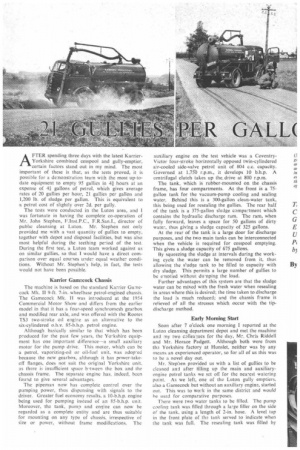
Page 79
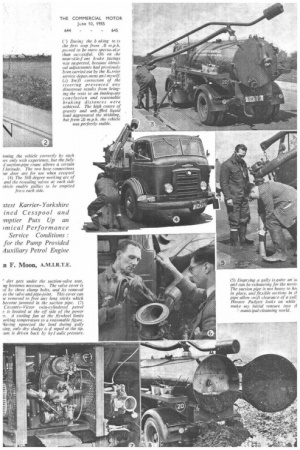
Page 80
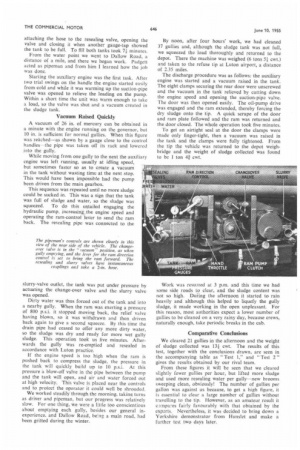
Page 81
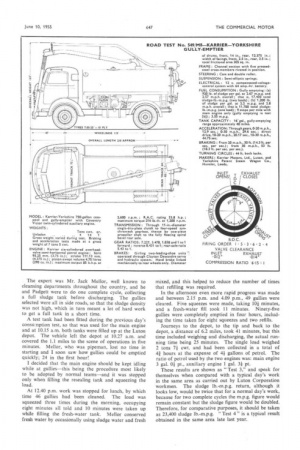
Page 82
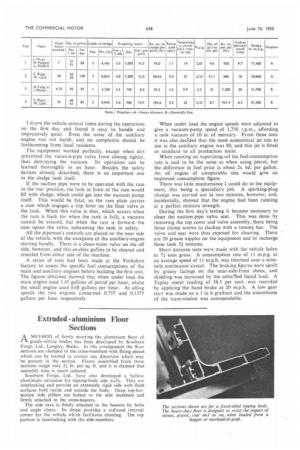
If you've noticed an error in this article please click here to report it so we can fix it.
and gully-emptier, certain factors stand out in my mind. The most important of these is that, as the tests proved, it is possible for a demonstration team with the most up-todate equipment to empty 95 gullies in 41 hours at an expense of LU gallons of petrol, which gives average rates of 20 gullies per hour, 21 gullies per gallon and 1,200 lb. of sludge per gallon. This is equivalent to a petrol cost of slightly over 2d. per gully.
The tests were conducted in the Luton area, and I was fortunate in having the complete co-operation of Mr. John Stephen, F.Inst.P.C., F.R.San.I., director of public cleansing at Luton. Mr. Stephen not only provided me with a vast quantity of gullies to empty, together with depot and disposal facilities, but was also most helpful during the teething period of the test. During the first test, a Luton team worked against us on similar gullies, so that I would have a direct comparison over equal courses under equal weather conditions. Without Mr. Stephen's help, in fact, the tests would not have been possible.
Kanrier Gamecock Chassis
The machine is based on the standard Karrier Gamecock Mk. II 9-ft, 7-in, wheelbase petrol-engined chassis. The Gamecock Mk. II was introduced at the 1954 Commercial Motor Show and differs from the earlier model in that it has a four-speed synchromesh gearbox and modified rear axle, and was offered with the Rootes TS3 two-stroke oil engine as an alternative to the six-cylindered o.h.v. 85-h.h.p. petrol engine.
Although basically similar to that which has been produced for the past few years, the Yorkshire equipment has one important difference—a small auxiliary motor for the pump drive. This motor, which can be a petrol, vaporizing-oil or oil-fuel unit, was adop'ed because the new gearbox, although it has power-takeoff flanges, does not suit the orignal Yorkshire unit. as there is insufficient space b-tween the box and the chassis frame. The separate engine has, indeed, been found to give several advantages.
The pipeman now has complete control over the pumping power, thus dispensing with signals to the driver. Greater fuel economy results, a 10-b.h.p. engine being used for pumping instead of an 85-b.h.p. unit. Moreover, the tank. pump and engine can now be regarded as a complete entity and are thus suitable for mounting on any type of chassis, irrespective of size or power, without frame modifications, The
auxiliary engine on the test vehicle was a CoventryVictor four-stroke horizontally opposed twin-cylindered air-cooled side-valve petrol unit of 804 c.c. capacity. Governed at 1,750 r.p.m., it develops 10 b.h.p. A centrifugal clutch takes up the_ drive at 800 r.p.m.
The tank, which is rubber-mounted on the chassis frame, has four compartments. At the front is a 75gallon tank for the vacuum-pump cooling and sealing water, Behind this is a 300-gallon clean-water tank, this being used for resealing the gullies. The rear half of the tank is a 375-gallon sludge compartment which contains the hydraulic discharge ram. The ram, when fully forward, leaves a space for 50 gallons of dirty water, thus giving a sludge capacity of 325 gallons.
Al the rear of the tank is a large door for discharge purposes, and the two main tanks can be interconnected when the vehicle is required for cesspool emptying. This gives a sludge capacity of 675 gallons.
By squeezing the sludge at intervals during the working cycle the water can be removed from it, thus altowine the sludge tank to be filled to capacity with dry sludge. This permits a large number of gullies to be emptied without dumping the load.
Further advantages of this system are that the sludge water can be mixed with the fresh water when resealing in areas where this is desired; the time taken to discharge the load is much reduced; and the chassis frame is relieved of all the stresses which occur with the tipdischarge method.
Early Morning Start
Soon after 7 o'clock one morning I reported at the Luton cleansing department depot and met the machine and my two colleaaues for the day, Mr. Chris Riddell and Mr. Horace Padgett. Although both were from the Yorkshire factory at Hunslet, neither was by any means an experienced operator, so for all of us this was lo be a novel day out.
Mr. Stephen provided us with a list of gullies to be cleaned and after titling up the main and auxiliaryengine petrol tanks we set oit for the nearest watering point. As we left, one of the Luton gully empticrs, also a Gamecock but without an auxiliary engine, started out. This was to work in the same district and would he used for comparative purposes.
There were two water tanks to be filled. The pump cooling tank was filled through a large filler on the side ci1. the tank. using a length of 2-in. hose. A level tap in the front plate of the tank served to indicate when the tank was full. The resealing tank was filled by
ioning the vehicle correctly by each Fes only with experience, but the fully d suction-pipe crane allows a certain f latitude. The two hose connections ?ar door are for use when cesspool (4) The 360 degree working arc of and the resealing valves at each side Miele enaMe gullies to be emptied fro;:t each side.
' dirt gets under the suction-valve seat, ng becomes necessary. The valve cover is ni by three clamp bolts, and its removal es the valve and pipe-joint. This cover can ie removed to free any long sticks which become jammed in the suction pipe. (7) Coventry-Victor twin-cylindered petrol e is located at the off side of the power A cooling fan at the flywheel limits orking temperature to a reasonable figure. 'laving squeezed the load during gully ring, only dry sludge is d mped at the tip. 'am is driven back by hy.1 aulic pressure.
attaching the hose to the resealing valve, opening the valve and closing it when another gauge-tap showed the tank to be full. To fill both tanks took 7 minutes.
From the water point we went to Dallow Road, a distance of a mile, and there we began work, Padgett acted as pipeman and from him I learned how the job was done.
Starting the auxiliary engine was the first task. After two trial swings on the handle the engine started easily from cold and while it was warming up the suction-pipe valve was opened to relieve the loading on the pump. Within a short time the unit was warm enough to take a load, so the valve was shut and a vacuum created in the sludge tank.
Vacuum Raised Quickly
A vacuum of 26 in. of mercury can be obtained in a minute with the engine running on the governor, but 10 in. is sufficient for normal gullies. When this figure was reached—as shown by a gauge close to the control handlesthe pipe was taken off its rack and lowered into the gully.
While moving from one gully to the next the auxiliary engine was left running, usually at idling speed, hut sometimes faster so as to create a vacuum in the tank without wasting time at the next stop. This would have been impossible had the pump been driven from the main gearbox.
This sequence was repeated until no more sludge could be sucked in. This was a sign that the tank was full of sludge and water, so the sludge was squeezed. To do this entailed engaging the hydraulic pump, increasing:the engine speed and operating the ram-control lever to send the ram back. The resealing pipe was connected to the
The pipeman's controls are shown clearly in this view of the near side of the vehicle. The changeover valve is in the " vacuum" position, as when gully emptying, and the lever for the ram direction control is set to bring the ram forward. The resealing and slurry valves have instantaneous couplings and take a 2-in. hose.
slurry-valve outlet, the tank was put under pressure by actuating the change-over valve and the slurry valve was opened.
Dirty water was thus forced out of the tank and into a nearby gully. When the ram was exerting a pressure of 800 ps.i. it stopped moving back, the relief valve having blown, so it was withdrawn and then driven back again to give a second squeeze. By this time the drain pipe had ceased to offer any more dirty water, so the sludge was dry and ready for more wet gully sludge. This operation took us five minutes. Afterwards the gully was re-emptied and resealed in accordance with Luton practice.
if the engine speed is too high when the ram is pushed back to compress the sludge, the pressure in the tank will quickly build up to 10 p.s.i. At this pressure a blow-off valve in the pipe between the pump and the tank will open, and air and water forced out at high velocity. This valve is placed near the controls and to protect the operator it could well be shrouded.
We worked steadily through the morning, taking turns as driver and pipcman, but our progress was relatively slow. For one thing, we were a little too conscientious about emptying each gully, besides our general inexperience. and Dallow Road, be:ng a main road, had been gritted during the winter. By noon, after four hours' work, we had cleaned 37 gullies and, although the sludge tank was not full, we squeezed the load thoroughly and returned to the depot. There the machine was weighed (6 tons 51 cwt.) and taken to the refuse tip at Luton airport, a distance of 2.35 miles.
The discharge procedure was as follows: the auxiliary engine was started and a vacuum raised in the tank. The eight clamps securing the rear door were unscrewed and the vacuum in the tank relieved by cutting down the engine speed and opening the suction-pipe valve. The door was then opened easily. The oil-pump drive was engaged and the ram extended, thereby forcing the dry sludge onto the tip. A quick scrape of the door and ram plate followed and the ram was returned and the door closed. The whole operation took five minutes.
To get an airtight seal at the door the clamps were made only finger-tight, then a vacuum was raised in the tank and the clamps were fully tightened. From the tip the vehicle was returned to the depot weighbridge and the weight of sludge collected was found to be 1 ton 41 cwt.
Work was resumed at 3 p.m. and this time we had some side roads to clear, and the sludge content was not so high. Wing the afternoon it started to rain heavily and although this helped to liquefy the gully sludge, it made working in the open unpleasant. For this reason, most authorities expect a lower number of gullies to be cleaned on a very rainy day, because crews, naturally enough, take periodic breaks in the cab.
Comparative Conclusions We cleared 21 gullies in the afternoon and the weight of sludge collected was 13.1cwt. The results of this test, together with the conclusions drawn, are seen in the accompanying table as "Test 1," and " Test 2 " gives the results obtained by our rival team.
From these figures it will be seen that we cleared slightly fewer gullies per hour, but lifted more sludge and used more resealing water per gully—new brooms sweeping clean, obviously! The number of gullies per gallon was against us because, to get a high figure, it is essential to clear a large number of gullies without travelling to the tip. However, as an amateur result it c.)rnpares fairly favourably with that obtained by the experts. Nevertheless, it was decided to bring down a Yorkshire demonstrator from Hunslet and make a further test two days later. The expert was Mr. Jack Mellor, well known to cleansing departments throughout the country, and he and Padgett were to do one complete cycle, collecting a full sludge tank before discharging. The gullies selected were all in side roads, so that the sludge density was not high, which in turn meant a lot of hard work to get a full tank in a short time.
A test tank had been fitted during the previous day's consuliption test, so that was used for the main engine and at 10.15 a.m, both tanks were filled up at the Luton depot. The vehicle left the depot at 10,27 a.m. and covered the 1.1 miles to the scene of operations in five minutes. Mellor, who was pipeman, lost no time in starting and I soon saw how gullies could be emptied quickly; 24 in the first hour!
I decided that the main engine should be kept idling while at gullies—this being the procedure most likely to be adopted by normal teams—and it was stopped only when filling the resealing tank and squeezing the load.
At 12.40 p.m. work was stopped for lunch, by which time 46 gullies had been cleaned. The load was squeezed three times during the morning, occupying eight minutes all told and 10 minutes were taken up while filling the fresh-water tank. Mellor conserved fresh water by occasionally using sludge water and fresh mixed, and this helped to reduce the number of times that refilling was required.
In the afternoon even more rapid progress was made and between 2.15 p.m. and 4.09 p.m., 49 gullies were cleared. Five squeezes were made, taking 101 minutes, and a fresh-water fill took 11 minutes. Ninety-five gullies were completely emptied in four hours, including the time taken for eight squeezes and two refills.
Journeys to the depot, to the tip and back to the depot, a distance of 6.2 miles, took 41 minutes, but this time included weighing and discharging, the actual running time being 25 minutes. The single load weighed
2 tons 71 cwt. and had been collected in a total of 4i hours at the expense of 4 gallons of petrol. The ratio of petrol used by the two engines was: main engine
3 gal. Oi pt., auxiliary engine 1 gal. 3i pt.
These results are shown as "Test 3," and speak for themselves when compared with a typical day's work in the same area as carried out by Luton Corporation workmen. The sludge lb.-m.p.g. return, although it looks low, would be twice that for a normal day's work, because for two complete cycles the m.p.g. figure would remain constant but the sludge figure would be doubled. Therefore, for comparative purposes, it should be taken as 23,400 sludge lb.-m.p.g. "Test 4" is a typical result obtained in the same area late last year. I drove the vehicle several times during the operations on the first day and found it easy to handle and impressively quiet. Even the noise of the auxiliary engine was not harsh, and no complaints should be forthcoming from local residents.
The equipment worked perfectly, except when dirt prevented the vacuum-pipe valve from closing tightly, thus destroying the vacuum, Its operation can he learned thoroughly in an hour, Besides the safety devices already described, there is an important one in the sludge tank itself, If the suction pipe were to be operated with the ram in the rear position, the tank in front of the ram would fill with sludge, which could get into the vacuum pump itself. This would be fatal, so the ram plate carries a cam which engages a trip lever on the float valve in the tank. When this valve is shut, which occurs when the ram is back (or when the tank is full), a vacuum cannot be created, but when the ram is forward the cam opens the valve, exhausting the tank in safety.
All the pipeman's controls are placed on the near side of the vehicle, with the exception of the auxiliary-engine starting handle. There is a clean-water valve on the off side, however, and this enables gullies to be cleared and resealed from either side of the machine.
A series of tests had been made at the Yorkshire factory to assess the specific fuel consumptions of the main and auxiliary engines before building the first unit. The figures obtained showed that when under load the main engine used 1.45 gallons of petrol per hour, whilst the small engine used 0.68 gallons per hour. At idling speeds the two engines consumed 0.757 and 0.1375 gallons per hour respectively. When under load the engine speeds were adjusted to give a vacuum-pump speed of 1,750 r.p.m., affording a tank vacuum of 10 in. of mercury. From these tests it was also decided that the most economical jet size to use in the auxiliary engine was 90, and this jet is fitted as standard to all production units.
When running on vaporizing oil the fuel-consumption rate is said to be the same as when using petrol, but the difference in fuel price is about 2s, 6d. per gallon. An oil engine of comparable size would give an improved consumption figure.
There was little maintenance I could do to the equipment, this being a specialist's job. A sparking-plug change was carried out in two minutes, however, and, incidentally, showed that the engine had been running at a perfect mixture strength.
During the first day's testing it became necessary to clean the suction-pipe valve seat. This was done by removing the top cover and valve assembly, there being three clamp screws to slacken with a tommy bar. The valve and seat were thus exposed for cleaning. There are 20 grease nipples on the equipment and to recharge these took 31 minutes.
Short distance tests were made with the vehicle laden to 71 tons gross. A consumption rate of II m.p.g. at an average speed of 1I m.p.h. was returned over a ninemile continuous circuit. The braking figures were spoilt by greasy facings on the near-side-front shoes, and skidding was increased by the unbaffled liquid load. A Tapley meter reading of 38.5 per cent. was recorded by applying the hand brake at 20 m.p.h. A low gear start was made on a 1 in 6 gradient and the smoothness of the transmission was commendable.