Mainta the Bic Munin Bus
Page 20
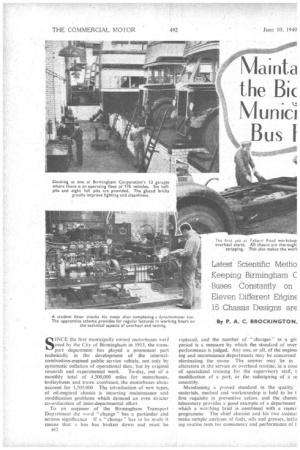
Page 21
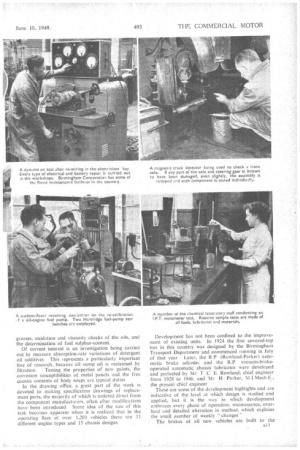
Page 22
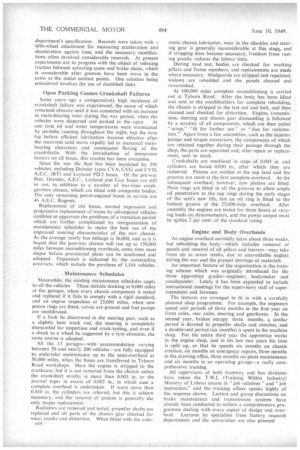
If you've noticed an error in this article please click here to report it so we can fix it.
Latest Scientific Meth° Keeping Birmingham C Buses Constantly on Eleven Different EriginE 15 Chassis Designs am
By P. A. C. BROCK1NGTON,
SINCE the first municipally owned motorbuses were used by the City of Birmingham in 1913, the transport department has played a prominent part technically in the development of the internalcombu.stion-engined public service vehicle, not only by systematic collation of operational data, but by original research and experimental work. To-day, out of a monthly total of 4,500000 miles for motorbuses, trolleybuses and trams combined, the motorbuses alori.-_, account for 3,500.000 The introduction of new types. of oil-engined chassis is incurring maintenance and modification problems which demand. an even stricter
co-ordination of inter-departmental effort .
To an engineer of the Birmingham Transport Department the word "change " has a particular and serious significance If a " cha.nge " has to be made it means that a bus has broken down and must be B12 replaced, and the number of changes" in a giv period is a measure by which the standard of over performance is judged_ Any one, or all, of the enginer ing and maintenance departments may be concerned eliminating the . cause The answer may lie in alteration in the service or overhaul routine, in a cow of specialized training for the supervisory staff, t modification of a part, or the redesigning of a in assembly.
Maintaining a proved standard in the quality materials, method and workmanship is held to be t first requisite in preventive action, and the ehernic laboratory provides a good example of a -department which a watching brief is combined with a resew) programme. The chief chemist and his two assistar make sample analyses of fuels, oils and greases, inelu ing routine tests for consistency and performance of t: greases, oxidation and viscosity checks of the oils, and the determination of fuel sulphur-content.
Of current interest is an investigation being carried out to measure absorption-rate variations of detergent oil additives. This represents a particularly important line of research, because all sump oil is reclaimed by filtration. Testing the properties of new paints, the corrosion susceptibilities of metal panels and the free caustic contents of body soaps are typical duties
In the drawing office, a great part of the work is devoted to making specification drawings of replacement parts, the majority of which is ordered direct from the component manufacturers, often after modifications have been introduced. Some idea of the size of this task becomes apparent when it is realized that in the operating fleet of over 1,20;1 vehicles there are 11 different engine types and 15 chassis designs
Development has not been confined to the improveJnent of existing units. In 1924 the first covered-top
• bus in this country was designed by the Birmingham Transport Department and commenced running in July of that year Later, the R.P. (Rowland-Parker) automatic brake adjuster and the R.P vacuum-brakeoperated automatic chassis lubricator were developed and perfected by Mr T C. E. Rowland. chief engineer from 1928 to 1946, and Mr H Parker, M 1 Mech E , the present chief engineer These are some -of the development highlights and are indicative of the level at which design is studied and applied, but it is the way in which development embraces every phase of operation, maintenance, overhaul and detailed alteration in method, which explains the small number of weekly " changes " The brakes ot all new vehicles are built to the a 13 department's specification. -Records were taken with a fifth-wheel attachment far measuring acceleration and deceleration against time, and the necessary modiflcalions often involved considerable research. At present experiments are in progress with the object of reducing friction between actuating cams and brake shoes, which is considerable after grooves have been worn in the cams at the initial contact points. One solution being considered involves the use of dumbbell links.
Open Parking Causes Crankshaft Failures . Some yearsago a comparatively high incidence of . crankshaftfailure was experienced, the cause of which remained Obscure until it was connected with an increase in main-bearing.wear. during the war period., when the vehicles were dispersed and parked in the open. At one time oil and water temperatures were maintained by periodie, running throughout the night, bnt the time lag before efficient lubrication became effective after the recurrent. cold starts rapidly led to increased mainbearing clearances and consequent flexing of the crankshafts. With the intrOcluction • of immersion heaters on all buses, this trouble has been overcome.
Since the war the fleet has been increased by 398 vehicles; including Daimler types CVA, CVG and CVD, A.E.C. (RT) and Leyland PD.2.buses. Of the pre-war fleet, Daimler, A.E.C., Leyland and Guy buses are still in use, in_ addition .to. a number of war-time crash-•
• gearbox chassis, which are fitted with composite bodies. The only remaining petrol-engined buses in service are 46 A.E.C. Regents. . •
Replacement of old !Rises, normal expansion and progressive replacement of trams by Oil-engined vehicles combine to aggravate the problems of a transition period, which are further coinplicated. by reorganization of maintenance schedules to make the best use of the improved wearing characteristics of the new chassis. As the average yearly bus mileage is 36,000, and as it is hoped that the post-war chassis will run up to 150,000 miles between reconditioning overhauls, some time must elapse before provisional plans can be confirmed and adonted. Expansion is indicated by the outstandina. contracts, Which include. the purchase of 1,104 vehicles.
Maintenance Schedules Meanwhile, the existing maintenance schedules apply to all the vehicles These include docking at 8,000 miles at the garages, when every chassis component is tested and replaced if it fails to comply with a rigid standard, and an engine inspection, at 25,000 miles, when new piston rings are fitted, valves are ground and fuel pumps are recalibrated.
If a fault be discovered in the steering gear, such as a slightly bent track rod, the steering is completely dismantled for inspection and crack-testing, and even if a shock to a wheel be suggested by a-tyre abrasion, the same course is adopted.
All the 13 garages—with accommodation varying between 50-and nearly 200 vehicles—are fully equipped to undertake maintenance up to the semi overhaul at 50,000 miles, when the buses are transferred to Tyburn Road workshops. Here the engine is stripped to the crankcase, but it is not removed from the chassis unless the crankshaft ovality is more than 0.003 in. or the journal taper in excess of 0002 in., in which case a complete overhaul is undertaken. If worn more than 0.010 in. the cylinders are rebored, but this is seldom necessary, and the renewal of pistons is generally the only major replacement.
Radiators are removed and tested, propeller shafts are replaced and all parts of the chassis gear checked for wear, cracks and distortion. When fitted with the auto
B14" matic chassis lubricator, wear in the shackles and steering gear is generally inconsiderable at this stags, and if stripping does become necessary, freedom from rusting greatly reduces the labour time.
During road test, bodies are checked for working pillars and frame members, and replacements are made where necessary. Mudguards are stripped and repainted, widows are rebedded and the panels cleaned and revam i shed. • At 100,000 miles complete reconditioning is carried out at Tyburn Road. After the body has been lifted and sent to the coachbuilders for complete rebuilding, the chassis is stripped to the last nut and bolt, and then cleaned and checked for distortion. Engine, transmission, steering and chassis gear dismantling is followed by a scrutiny of all components, which are then coded " scrap," " fit for further use" or "due for reclamation." Apart from a few assemblies, such as the injector pumps and torque convertors, the components of which are retained together during their passage through the shop, the parts are separated and, after repair or replacement, sent to stock.
Crankshafts are machined in steps of 0.005 in, and cylinders are bored 0.030 in., after which they are resleeved. Pistons are welded at the top land and the grooves are recut at the first complete overhaul. At the subsequent overhaul, however, new pistons are fitted. Plain rings are fitted in all the grooves to allow ample oil penetration to the top rings during the early stages of the unit's new life, but an oil ring is fitted to the bottom groove at the 25,000-mile overhaul. After assembly the engines are tested for three hours at varying loads on dynamometers, arid the power output must be ithin 2 per cent.. of the standard rating.
Engine and Body Overhauls
An engine overhaul normally takes about three weeks. but rebuilding the body—Which includes removal of panels and renewal of all pillars and bearers--may take from 'six to seven weeks, due to unavoidable neglect during the war and the present shortage of materials.
An important feature' of 'the organization is the training scheme .which was originally introduced for the three apprentice gradesengineer, bodymaker and coachpainter. Lately it has been expanded to include instructional meetings for' the supervisory staff of superintendents and foremen.
The lectures are arranged to fit in with a carefully planned shop programme. For example, the engineers spend unit periods of three months in the first year on
front axles, rear. axles, steering and gearboxes. In the second year, brakes occupy three months, a similar
period is devoted to propeller shafts and clutches, and a double-unit period (six months) is spent in the machine shop. For the entire third year the apprentice works in the engine shop, and in his last two years his time is split up, so that he spends six months on chassis erection, six months on emergency repairs, three months in the drawing office, three months on plant maintenance and six months in an operating garage—a really comprehensive training.
All supervisors of both tramway and bus divisions have taken the T.W.I. (Training Within IndustrY) Ministry of Labour course in "job relations " and "job instruction," and the training officer, speaks highly of the response shown. Lecture and group discussions on brake maintenance and transmission systems have already been conducted to initiate a comprehensive programme dealing with every aspect of design and overhaul. • Lectures by specialists from factory research departments and the universities are also planned