Brake developmeni never stop!
Page 28
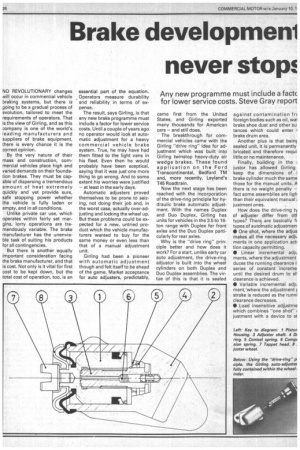
Page 29
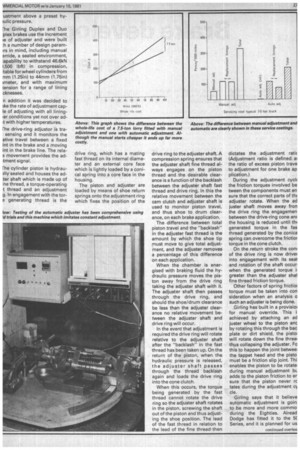
Page 30
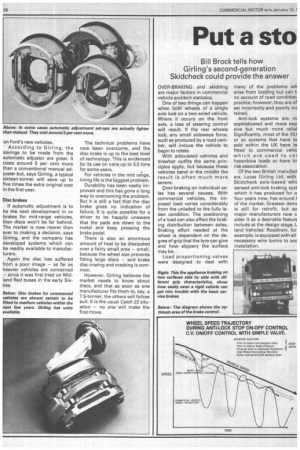
If you've noticed an error in this article please click here to report it so we can fix it.
Any new programme must include a factc for lower service costs. Steve Gray report
NO REVOLUTIONARY changes will occur in commercial vehicle braking systems, but there is going to be a gradual process of evolution, tailored to meet the requirements of operators. That is the view of Girling, and as this company is one of the world's leading manufacturers and suppliers of brake equipment, there is every chance it is the correct opinion.
By the very nature of their mass and construction, commercial vehicles place high and varied demands on their foundation brakes. They must be capable of dispersing a tremendous amount of heat extremely quickly and yet provide sure, safe stopping power whether the vehicle is fully laden or empty, and in all conditions.
Unlike private car use, which operates within fairly set margins, lorry operations are tremendously variable. The brake manufacturer has the unenviable task of suiting his products for all contingencies.
But there is another equally important consideration facing the brake manufacturer, and that is cost. Not only is it vital for first cost to be kept down, but the total cost of operation, too, is an essential part of the equation. Operators measure durability and reliability in terms of expense.
The result, says Girling, is that any new brake programme must include a factor for lower service costs. Until a couple of years ago no operator would look at automatic adjustment for a heavy commercial vehicle brake system. True, he may have had them fitted to the light vans in his fleet. Even then he would probably have been sceptical, saying that it was just one more thing to go wrong. And to some extent his worries were justified — at least in the early days.
Automatic adjusters proved themselves to be prone to seizing, not doing their job and, in the worst case, actually over-adjusting and locking the wheel up. But these problems could be expected for a new, untried product which the vehicle manufacturers wanted to buy for the same money or even less than that of a manual adjustment unit.
Girling had been a pioneer with automatic adjustment though and felt itself to be ahead of the game. Market acceptance for auto adjusters, predictably, came first from the United States, and Girling exported many thousands for American cars — and still does.
The breakthrough for commercial vehicles came with the Girling "drive ring" idea for adjustment which was built into Girting twinstop heavy-duty air wedge brakes. These found application on the Ford Transcontinental, Bedford TM and, more recently, Leyland's T45 Roadtrain.
Now the next stage has been reached with the incorporation of the drive-ring principle for hydraulic brake automatic adjustment. With the names Duplex and Duo Duplex, Girling has units for vehicles in the 3.5 to 16ton range with Duplex for front axles and the Duo Duplex particularly for rear axles.
Why is the "drive ring" principle better and how does it work? For a start, unlike early car auto adjustment, the drive-ring adjustor is built into the wheel cylinders on both Duplex and Duo Duplex assemblies. The virtue of this is that it is sealed
against contamination frc foreign bodies such as oil, wa1 brake shoe dust and other SU tances which could enter I brake drum area.
Another plus is that beinc sealed unit, it is permanently bricated and therefore requi little or no maintenance.
Finally, building in the justor has allowed Girling keep the dimensions of brake cylinder much the same those for the manual units. A there is no weight penalty — fact some assemblies are ligh than their equivalent manual justrnent ones.
How does the drive-ring t), of adjuster differ from ott types? There are basically ft types of automatic adjustrnen.
• One shot, where the adjus makes all the necessary adjt.. ments in one application acti tier capacity permitting.
• Linear incremental adju ments, where the adjustment duces the running clearance i, series of constant increme: untii the desired drum to sh clearance is achieved.
• Variable incremental adju ment, where the adjustment r stroke is reduced as the runni clearance decreases.
• Load insensitive adjustme which combines "one shot" justment with a device to st ustment above a preset hyiulic pressure.
Ehe Girling Duplex and Duo plex brakes use the increment te of adjuster and were built :h a number of design param:rs in mind, including manual amide, a sealed environment, :apability to withstand 46.6kN 1,500 lbft) in compression, table for wheel cylinders from mm (1.251n) to 44mm (1.75in) 'meter, and with maximum tension for a range of lining cknesses.
n addition it was decided to ike the rate of adjustment caple of adjusting with all liningNar conditions yet not over ad;t with higher temperatures.
fhe drive-ring adjustor is trasensing and it monitors the ative travel between a fixed int in the brake and a moving int in the brake line. The relaa movement provides the adtrnent signal.
fhe cylinder piston is hydrauIlly sealed and houses the adter shaft which is made up of ne thread, a torque-operating t thread and an adjustment g. In engagement with the tore generating thread is the drive ring, which has a mating fast thread on its internal diameter and an external core face which is lightly loaded by a conical spring into a core face in the housing.
The piston and adjuster are loaded by means of shoe return springs onto the adjustment ring which fixes the position of the drive ring to the adjuster shaft. A compression spring ensures that the adjuster shaft fine thread always engages on the piston thread and the desirable clearance is a function of the backlash between the adjuster shaft fast thread and drive ring. In this the relative movement between the cam clutch and adjuster shaft is used to monitor piston travel, and thus shoe to drum clearance, on each brake application.
The difference between total piston travel and the "backlash" in the adjuster fast thread is the amount by which the shoe tip must move to give total adjustment, and the adjuster removes a percentage of this difference on each application.
When the chamber is energised with braking fluid the hydraulic pressure moves the piston away from the drive ring taking the adjuster shaft with it. The adjuster shaft then passes through the drive ring, and should the shoe/drum clearance be less than the adjuster clearance no relative movement between the adjuster shaft and drive ring will occur.
In the event that adjustment is required the drive ring will rotate relative to the adjuster shaft after the "backlash" in the fast thread has been taken up. On the return of the piston, when the hydraulic pressure is released, the adjuster shaft passes through the thread backlash again and loads the drive ring into the cone clutch.
When this occurs, the torque being generated by the fast thread cannot rotate the drive ring so the adjuster shaft rotates in the piston, screwing the shaft out of the piston and thus adjusting the shoe position. The lead of the fast thread in relation to the lead of the fine thread then dictates the adjustment ratic {Adjustment ratio is defined at the ratio of excess piston trave to adjustment for one brake ap plication.) During the adjustment cyclt the friction torques involved be tween the components must en sure that the correct parts of tilt adjuster rotate. When the ad juster shaft moves away fron the drive ring the engagemen between the drive-ring cone anc the housing is reduced until tht generated torque in the fas thread generated by the conica spring can overcome the frictior torque in the cone clutch.
On the return stroke the cons of the drive ring is now driver into engagement with its seal and rotation of the shaft occur: when the generated torque greater than the adjuster shal fine thread friction torque.
Other factors of spring frictioi torque must be taken into con sideration when an analysis o such an adjuster is being done.
Girling has built in a provisioi for manual override. This i achieved by attaching an ad juster wheel to the piston anc by rotating this through the bac plate or dirt shield, the pistol will rotate down the fine threal thus collapsing the adjuster. Fa this to happen the joint betweei the tappet head and the pisto must be a friction slip joint. Thi enables the piston to be rotate, during manual adjustment bi adds to the piston friction to er sure that the piston never rc tates during the adjustment cy cle.
Girling says that it believe automatic adjustment is goin to be more and more comma during the Eighties. Al read Dodge has fitted it to the 5C Series, and it is planned for us on Ford's new vehicles.
According to Girling, the savings to be made from the automatic adjustor are greet. It costs around 5 per cent more than a conventional manual adjuster but, says Girling, a typical sixteen-tonner will save up to five times the extra original cost in the first year.
Disc brakes If automate adjustment is to be the next development in cv brakes for mid-range vehicles, then discs won't be far behind. The market is now nearer than ever to making a decision, says Girling, and the company has developed systems which can be readily available tomanufacturers.
Again the disc has suffered from a poor image — as far as heavier vehicles are concerned — since it was first tried on Midland Red buses in the early Sixties. The technical problems have now been overcome, and the disc brake is up to the best level of technology. This is evidenced by its use on vans up to 3,5 tons for some years.
For vehicles in the mid range, lining life is the biggest problem.
Durability has been vastly improved and this has gone a long way to overcoming the problem. But it is still a fact that the disc brake gives no indication of failure. It is quite possible for a driver to be happily unaware that the pads are down to the metal and keep pressing the brake pedal.
There is also an enormous amount of heat to be dissipated over a fairly small area — small, because the wheel size prevents fitting large discs — and brake disc crazing and cracking is common.
However, Girling believes the market needs to know about discs, and that as soon as one manufacturer fits them to, say, a 7.5-ton ner, the others will follow suit. It is the usual Catch 22 situation — no one will make the first move.