PREVENTING TROUBLE WITH BIG-ENDS.
Page 61
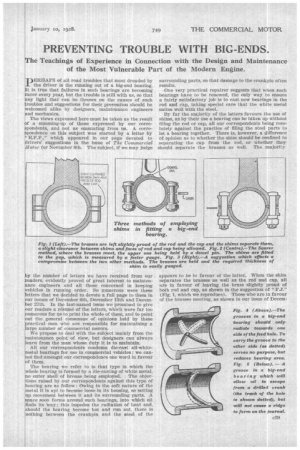
Page 62
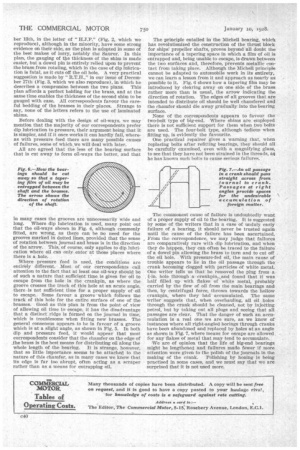
If you've noticed an error in this article please click here to report it so we can fix it.
he Teachings of Experience in Connection with the Design and Maintenance of the Most Vulnerable Part of the Modern Engine.
PERHAPS of all road troubles that most dreaded by the driver is the running out of a big-end bearing. t is true that failures in such bearings are becoming arer every year, but the trouble is still with us, so that
y light that can be thrown on the causes of such roubles and suggestions for their prevention should be elcomed alike by designers, maintenance engineers nd mechanics.
The views expressed here must be taken as the result f a summing-up of those expressed by our correpondents, and not as emanating from us. A corre, pondence on this subject was started by a letter by
• E.F.F.," which appeared in our page devoted to rivers' suggestions in the issue of The Commercial lfotor for November 8th. The 'subject, if we May judge
y the number of letters we have received from our eaciers, evidently proved of great interest to maintenace engineers and all those concerned in keeping chides in running order. So numerous were these etters that we decided to devote a full page to them in ur issues of December 6th, December 13th and Decemer 27th. In the last-named issue we promised to give ur readers a résumé of the letters, which were far too tumerous for us to print the whole of them, and to point ut the general consensus of opinions held by these ractical men who are responsible for maintaining a arge number of commercial motors.
We propose to deal with the subject mainly from the iaintenance point of view, but designers can always earn from the man whose duty it is to maintain.
All our correspondents condemn die-cast all-whiteetai bearings for use in commercial vehicles; we canot find amongst our correspondence one word in favour rf them.
The bearing we refer to is that type in which the thole bearing is formed by a die-casting of white metal, o outer shell of bronze being employed. The objections raised by our correspondents against this type of bearing are as follow : Owing to the soft nature of the metal it is apt to become loose in its housing, so setting up movement between it and its surrounding parts. A pace soon forms around such bearings, into which oil finds its way ; this impedes the radiation of heat and, should the bearing become hot and run out, there is nothing between the crankpin and the steel of the surrounding parts, so that damage to the crankpin often results.
One very practical repairer suggests that when such bearings have to he renewed, the only way to ensure a fairly satisfactory job is to cast new bearings in the rod and Cap, taking special care that the white metal unites well with the steel.
By far the majority of the letters favours the use of shims, as by their use a bearing can be taken up without filing the rod or cap, all our correspondents being resolutely against the practice of filing the steel parts to let a bearing together. There is, however, a difference of opinion as to whether the shim should he confined to separating the cap from the rod, or whether they should separate the brasses as well. The majority appears to be in favour of the latter. When the shim separates the brasses as well as the rod and cap, all are in favour of leaving the brass slightly proud of both rod and cap, as shown in the suggestion of " F.J." (Fig. 1, which we reproduce). Those who are in favour of the brasses meeting, as shown in our issue of Decem her 13th, in the letter of " II.J.P." (Fig. 2, which we reproduce), although in the minority, have some strong evidence on their side, as the plan is adopted in some of the best makes of lorry, notably the &wren In this plan, the gauging of the thickness of the shim is made easier, but a dowel pin is entirely relied upon to prevent the brass from rotating, which in the case of dip lubrication is fatal, as it cuts off the oil hole. A very practical suggestion is made by " R.T.H.," in our issue of December 27th (Fig. 3, which we also reproduce), in which he describes a compromise between the two plans. This plan affords a perfect holding for the brass, and at the same time enables the thickness of the second shim to be gauged with ease. All correspondents favour the careful bedding of the brasses in their places. Strange to say, none of the letters refers to the use of laminated Shims.
Before dealing with the design of oil-ways, we may mention that the majority of our correspondents prefer dip lubrication to pressure, their argument being that it is simpler, and if it once works it can hardly fail, whereas with pressure feed there are many possible causes of failure, some of which we will deal with later.
All are agreed that the less of the bearing surface that is cut away to form oil-ways the better, and that
in many cases the grooves are unnecessarily wide and long. Where dip lubrication is used, many point out that the oil-ways shown in Fig. 4, although commonly fitted, are wrong, as there can be no need for the grooves marked in dotted lines, provided that the sense of rotation between journal and brass is in the direction of -the arrow. This, of course, only applies to dip lubrication where oil can only enter at those places where there is a hole.
Where pressure feed Is used, the conditions are entirely different. Most of our correspondents call attention to the fact that at least one oil-way should be of such a nature that sufficient time is given for oil to escape from the hole in the crankpin, as where the groove crosses the track of this hole at an acute angle, there is not sufficient time for a proper supply of oil to escape. Some favour a groove which follows the track of this hole for the entire surface of one of the brasses. Good as this plan is from the point of view of allowing oil time to escape, it has the disadvantage that a distinct ridge is formed on the journal in time, which is troublesome when fitting new brasses. The general consensus appears to be in favour of a groove which is at a slight angle, as shown in Fig. 5. In both dip and pressure feed, it would appear that most correspondents consider that the chamfer on the edge of the brass is the best means for distributing oil along the whole length of the bearing. It is strange, however, that so little Importance seems to be attached to the nature of this chamfer, as in many cases we know that its edge is far too abrupt, often acting as a scraper rather than as a means for entrapping oil. The principle entailed in the Michell bearing, which has revolutionized the construction of the thrust block for ships' propeller shafts, proves beyond all doubt the importance of a tapering space in which a film of oil is entrapped and, being unable to escape, is drawn between the two surfaces and, therefore, prevents metallic contact from taking place. Although the Michell principle cannot be adapted to automobile work in its entirety, we can learn a lesson from it and approach as nearly as possible to it. Fig. 6 shows how a tapering film may be introduced by clearing away on one side of the brass rather more than is usual, the arrow indicating the direction of rotation. The edges of all grooves that are intended to distribute oil should be well chamfered and the chamfer should die away gradually, into the bearing surface.
None of the correspondents appears to favour the two-bolt type of big-end. Where shims are employed there is not sufficient support for them when two bolts are used. The four-bolt type, although tedious when fitting up, is evidently the favourite.
One practical repairer gives a warning that, when replacing bolts after refitting hearings, they should all be carefully examined, even with a magnifying glass, to see that they have not been strained in the threads, as he has known such bolts to cause serious failures.
The commonest cause of failure is undoubtedly want of a proper supply of o'l to the bearing. ft is suggested by some of the writers that in a case of unduly early failure of a bearing, it should never be trusted again until the cause of the failure has been ascertained. From the correspondence, we may judge that failures are comparatively rare with dip lubrication, and when they do happen, they can often be traced to the failure" of a dowel pin allowing the brass to turn and to cut off . the oil hole. With pressure-fed oil, the main cause of trouble appears to lie in the oil passage through the crank becoming clogged with particles of white metal. One writer tells us that he removed the plug from a 4-in. hole through a crankpin, and found that it was half filled up . with flakes of white metal, probably carried by the flow of oil from the main bearings and then, by centrifugal force, thrown towards the hollow crankpin, where they had accumulated. The same writer suggests that, when overhauling, all oil holes through the crank should be cleaned, not by injecting petrol, hut by taking out all plugs and seeing that all passages are clear. That the danger of such an accumulation is a real one we are sure, as we know of instances where all right-angled borings through cranks have been abandoned and replaced by holes at an angle as shown in Fig. 7, where means for escape are allowed for any flakes of metal that may tend to accumulate.
We are of opinion that the life of big-end bearings might he lengthened and failures made fewer if more attention were given to the polish of the journals in the making of the crank. Polishing by honing is being practised in some cases, and we must say that we are surprised that it is not used more.