Earning while learning
Page 14
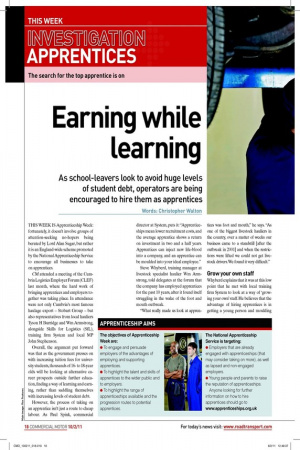
Page 15
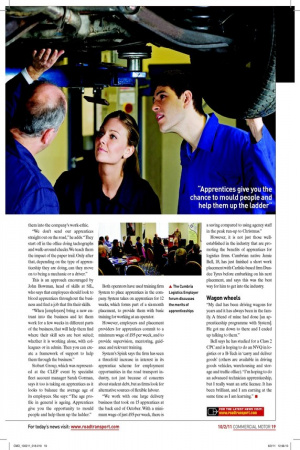
If you've noticed an error in this article please click here to report it so we can fix it.
As school-leavers look to avoid huge levels of student debt, operators are being encouraged to hire them as apprentices
Words: Christopher Walton
THIS WEEK IS Apprenticeship Week: fortunately, it doesn’t involve groups of attention-seeking no-hopers being berated by Lord Alan Sugar, but rather it is an England-wide scheme promoted by the National Apprenticeship Service to encourage all businesses to take on apprentices.
CM attended a meeting of the Cumbria Logistics Employer Forum (CLEF) last month, where the hard work of bringing apprentices and employers together was taking place. In attendance were not only Cumbria’s most famous haulage export – Stobart Group – but also representatives from local hauliers Tyson H Burridge and Wm Armstrong, alongside Skills for Logistics (SfL), training irm System and local MP John Stephenson.
Overall, the argument put forward was that as the government presses on with increasing tuition fees for university students, thousands of 16to 18-year olds will be looking at alternative career prospects outside further education, inding a way of learning and earning, rather than saddling themselves with increasing levels of student debt.
However, the process of taking on an apprentice isn’t just a route to cheap labour. As Paul Spink, commercial director at System, puts it: “Apprenticeships mean lower recruitment costs, and the average apprentice shows a return on investment in two and a half years. Apprentices can inject new life-blood into a company, and an apprentice can be moulded into your ideal employee.” Steve Whyberd, training manager at livestock specialist haulier Wm Armstrong, told delegates at the forum that the company has employed apprentices for the past 10 years, after it found itself struggling in the wake of the foot and mouth outbreak.
“What really made us look at appren
tices was foot and mouth,” he says. “As one of the biggest livestock hauliers in the country, over a matter of weeks our business came to a standstill [after the outbreak in 2001] and when the restrictions were lifted we could not get livestock drivers. We found it very dificult.”
Grow your own staff
Whyberd explains that it was at this low point that he met with local training irm System to look at a way of ‘growing your own’ staff. He believes that the advantage of hiring apprentices is in getting a young person and moulding them into the company’s work-ethic.
“We don’t send our apprentices straight out on the road,” he adds. “They start off in the ofice doing tachographs and walk-around checks. We teach them the impact of the paper trail. Only after that, depending on the type of apprenticeship they are doing, can they move on to being a mechanic or a driver.” This is an approach encouraged by John Bowman, head of skills at SfL, who says that employees should look to blood apprentices throughout the business and ind a job that its their skills.
“When [employers] bring a new entrant into the business and let them work for a few weeks in different parts of the business, that will help them ind where their skill sets are best suited; whether it is working alone, with colleagues or in admin. Then you can create a framework of support to help them through the business.” Stobart Group, which was represented at the CLEF event by specialist leet account manager Sarah Gorman, says it too is taking on apprentices as it looks to balance the average age of its employees. She says: “The age proile in general is ageing. Apprentices give you the opportunity to mould people and help them up the ladder.” Both operators have used training irm System to place apprentices in the company. System takes on apprentices for 12 weeks, which forms part of a six-month placement, to provide them with basic training for working at an operator.
However, employers and placement providers for apprentices commit to a minimum wage of £95 per week, and to provide supervision, mentoring, guidance and relevant training.
System’s Spink says the irm has seen a threefold increase in interest in its apprentice scheme for employment opportunities in the road transport industry, not just because of concerns about student debt, but as irms look for alternative sources of lexible labour.
“We work with one large delivery business that took on 15 apprentices at the back end of October. With a minimum wage of just £95 per week, there is a saving compared to using agency staff in the peak run-up to Christmas.” However, it is not just those wellestablished in the industry that are promoting the beneits of apprentices for logistics irms. Cumbrian native Jamie Bell, 18, has just inished a short work placement with Carlisle-based irm Dundee Tyres before embarking on his next placement, and says this was the best way for him to get into the industry.
Wagon wheels
“My dad has been driving wagons for years and it has always been in the family. A friend of mine had done [an apprenticeship programme with System]. He got me down to there and I ended up talking to them.”
Bell says he has studied for a Class 2 CPC and is hoping to do an NVQ in logistics or a B-Tech in ‘carry and deliver goods’ (others are available in driving goods vehicles, warehousing and storage and trafic ofice). “I’m hoping to do an advanced technician apprenticeship, but I really want an artic licence. It has been brilliant, and I am earning at the same time as I am learning.” ■