ROAD AND WORKSHOP by HANDYMAN
Page 42
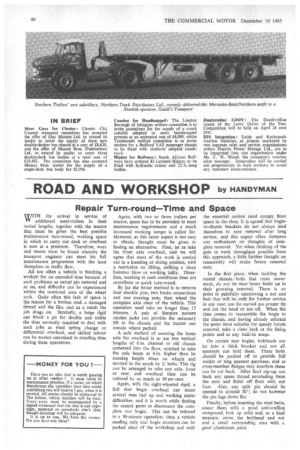
If you've noticed an error in this article please click here to report it so we can fix it.
Repair Turn-round—Time and Space
WITH the arrival in service of additional semi-trailers in their varied lengths, together with the tractor that must be given the best possible maintenance turn-round, working space in which to carry out dock or overhaul is now at a premium. Therefore, ways and means must be found whereby the transport engineer can meet his full maintenance programme with the least disruption to traffic flow.
All too often a vehicle is blocking a workpit for an extended time because of such problems as swivel pin removal and so on, and difficulty can be experienced within the restricted area of the wheel arch. Quite often this lack of space is the reason for a broken stud, a damaged thread and the like, and as a result the job drags on. Similarly, a large rigid can block a pit for double and treble the time normally required to deal with such .jobs as road spring change or differential overhaul, and skilled labour can be wasted unnoticed in standing time during these operations.
Again, with two or three trailers per tractor, space has to be provided to meet maintenance requirements and a much increased working tempo is called for. However, as this latter aspect is not easy to obtain, thought must be given to finding an alternative. First, let us take the front axle overhaul, and we will agree that most of the work is carried out in a kneeling or sitting position, with a restriction on lifting, striking a clean hammer blow or working tidily. Therefore, working in such conditions does not contribute to quick turn-round.
By far the better method is to remove four shackle pins, two brake connections and one steering arm; then wheel the complete axle clear of the vehicle. This operation need take no longer than 15 minutes. A pair of Simplex pattern ratchet jacks can provide the necessary lift to the chassis and the tractor can remain where parked.
A safe method of securing the loose axle for overhaul is to use two vertical lengths of Sin, channel or old chassis cemented into the floor, notched to take the axle beam at 6 in. higher than its running height when on wheels and secured in the notch by U bolts. This rig can be arranged to take any axle, front or rear, and overhaul time can be reduced by as much as 50 per cent.
Again, with the eight-wheeled rigid, a full rear bogie overhaul can mean several men tied up and working under difficulties, and it is worth while finding the easiest point to disconnect the complete rear bogie. This can be reduced to a 30-minute operation; thus, a vehicle needing only rear bogie attention can be parked clear of the workshop and only the essential section need occupy floor space in the shop. It is agreed that bogieto-chassis brackets do not always lend themelves to easy removal after long service, and this aspect often dampens any enthusiasm on thoughts of complete removal. Yet when thinking of the gain in work throughput possible from this approach, a little further thought on reassembly will make future removal easy.
In the first place, when tackling the rusted chassis/ bolts that resist movement, do not let man hours build up in their groaning removal. There is no point in painfully unscrewing a nut and bolt that will be unfit for further service in any case; use the curved gas gouger tip and cut the head or nut off. When the time comes to reassemble the bogie to the chassis, and having already selected the point most suitable for speedy future removal, take a close look at the fixing points and at any built-in snags.
On certain rear bogies, boltheads are let into a thick bracket and not all spanners can hold them. These bolts , should be packed off to provide full socket or ring spanner purchase, and as cross-member flanges may interfere these can be cut back. After final nip-up, cut back any spare thread protruding from the nuts and finish off flush with nut face. Also, any split pin should be opened to around 30'; do not hammer the pin legs down flat.
Finally, before inserting the vital bolts, smear them with a good anti-scuffing compound, lock up solid and, as a final measure, cover the boltheadand nut and a small surrounding area with a good aluminium paint.