Nitralloy Steels for Cylinders and Brake Drums
Page 41
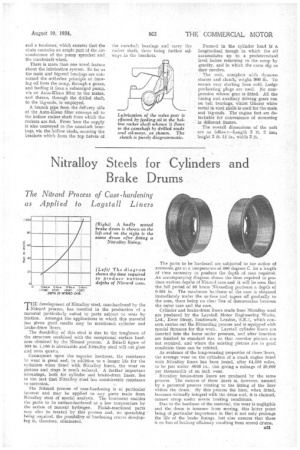
If you've noticed an error in this article please click here to report it so we can fix it.
The Nitrard Process of Case-hardening as Applied to Laystall Liners
THE development of Nitralloy steel, case-hardened by the Nitrard process, has resulted in the production of a material particularly suited to parts subject to wear by friction. Amongst the applications in which this material has given good results may be mentioned cylinder and brake-drum liners.
The durability of this steel is due to the toughness of the structure combined with the exceptional surface hardness obtained by the Nitrard process. A Brinell figure of 900 to 1,100 is obtainable and Nitralloy steel will cut glass and even quartz.
Consequent upon the superior hardness, the resistance 10 wear is great and, in addition to a longer life for the cylinders when fitted with Nitralloy liners, the wear on pistons and rings is much reduced. A further important advantage, both for cylinder and brake-drum liners, lies in the fact that Nitralloy steel has considerable resistance to corrosion.
The Nitrard process of case-hardening is of particular interest and may be applied to any parts made from Nitralloy steel of special analysis. The treatment enables the parts to be surface-hardened at a low temperature by the action of nascent hydrogen. Finish-machined parts may also be treated by this process and, no quenching being required, the possibility of hardening cracks developing is, therefore, eliminated. The parts to be hardened are subjected to the action of ammonia gas at a temperature of 500 degrees C. for a length of time necessary to produce the depth of case required. An accompanying diagram shows the time required to produce various depths of Nitrard case and it will be seen that the full period of 90 hours Nitrard.ing produces a depth of 0.031 in. The maximum hardness of the case is obtained immediately under the surface and tapers off gradually to the core, there being no clear line of demarcation between the outer case and the core, Cylinder and brake-drum liners made from Nitralloy steel are produced by the Laystall Motor Engineering Works, Ltd., Ewer Street, Southwark, London, S.E.1, which concern carries out Le Nitrarding process and is equipped with special furnaces for this work. Laystall cylinder liners are inserted into the bores under pressure, and after insertion are finished to standard size, so that oversize pistons are not required, and where the existing pistons are in good condition these can be refitted.
As evidence of the long-wearing properties of these liners, the average wear on the cylinders of a coach engine fitted with Nitralloy liners has been found, after 64.000 miles, to be just under .0035 in., this giving a mileage of 20,000 per thouRandth of an inch wear.
Nitralloy brake-drum liners are produced by the same process. The success of these liners is, however, assured by a patented process relating to the fitting of the liner within the drum. By this process the liner, when fitted, becomes virtually integral with the drum and, it is claimed, cannot creep under severe braking conditions.
Due to the hardness of the material, the wear is negligible and the drum is immune from scoring, this latter point being of particular importance in that it not only prolongs the life of the brake linings, but also ensures that there is no loss of braking efficiency resulting from scored drums.