Cool Considerations
Page 75
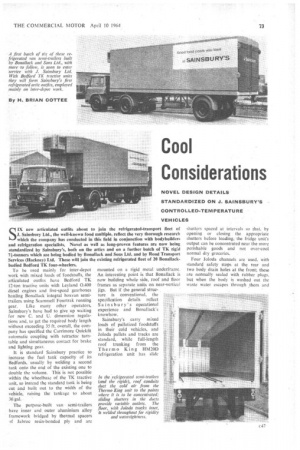
Page 76
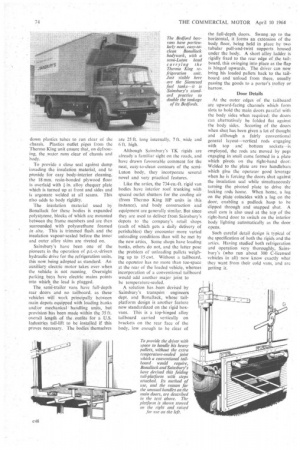
If you've noticed an error in this article please click here to report it so we can fix it.
NOVEL DESIGN DETAILS STANDARDIZED ON J. SAINSBURY'S CONTROLLED-TEMPERATURE VEHICLES
SIX new articulated outfits about to join the refrigerated-transport fleet of J. Sainsbury Ltd., the well-known food multiple, reflect the very thorough research which the company has conducted in this field in conjunction with bodybuilders and refrigeration specialists. Novel as well as long-proven features are now being standardized by Sainsbury's, both on the artics and on a further batch of TIC rigId 71-tonners which are being bodied by Itonallack and Sons Ltd. and by Road Transport Services (Hackney) Ltd. These.will loin the existing refrigerated fleet of 20 Bonallack. bodied Bedford TIC four-wheelers.
To be used mainly for inter-depot work with mixed loads of foodstuffs, the articulated outfits have Bedford TK 12-ton tractive units with Leyland 0.400 diesel engines and five-speed gearboxes hauling Bonallack integral boxvan semitrailers using Scarnmell Fourtrak running gear. Like many other operators, Sainsbury's have had to give up waiting for new C. and U. dimension regulations and, to get the required body length without exceeding 35 ft. overall, the company has specified the Carrirnore Quick& automatic coupling with retractor turntable and simultaneous contact for brake and lighting gear.
it is standard Sainsbury practice to increase the fuel tank capacity of its Bedford& usually by welding a second tank onto the end of the existing one to double the volume. This is not possible within the wheelbase of the TK tractive unit, so instead the standard tank is being cut and built out to the width of the vehicle, raising the tankage to about 36 gal. • The purpose-built van semi-trailers have inner and outer aluminium alloy framework bridged by thermal spacers Jabroc resin-bonded ply and are mounted on a rigid metal underframe. An ,interesting point is that Bonallack is now building whole side, roof and floor frames as separate units on. near-vertical jigs. But if the general struc ture is conventional, the specification details reflect Sainsbury's operational experience and Bonallack's knowhow.
Sainsbury's carry mixed loads of palletized foodstuffs in their cold vehicles, and Joloda pallets and tracks are standard, while full-length roof trunking from the Thermo King HM2OD refrigeration unit has slide shutters spaced at intervals so that, by opening or closing the appropriate shutters before loading, the fridge unit's output can be concentrated near the more perishable goods and not over-cool normal dry groceries.
Four Joloda channels are used, with standard safety stops at the rear and two body drain holes at the front; these are normally sealed with rubber plugs, but when the body is washed out the waste water escapes through them and
down plastics tubes to run clear of the chassis. Plastics outlet pipes from the Thermo King unit ensure that, on defrosting, the water runs clear of chassis and body.
To provide a close seal against damp invading the insulation material, and to provide for easy body-interior cleaning, the 18 mm. resin-bonded plywood floor is overlaid with in. alloy chequer plate which is turned up at front and sides and is argonarc welded at all seams. This also adds to body rigidity.
The insulation material used by Bonallack for these bodies is expanded polystyrene, blocks of which are mounted between the frame members and are then surrounded with polyurethane foamed in situ. This is trimmed flush and the insulation vapour-sealed before the inner and outer alloy skins are riveted on.
Sainsbury's have been one of the pioneers in the operation of p.t.-o.-driven hydraulic drive for the refrigeration 'units, this now being adopted as standard. An auxiliary electric motor takesover when the vehicle is not running. Overnight parking bays have electric mains points into which_ the lead is plugged.
The semi-trailer vans have full-depth rear doors and no tailboard, as these vehicles will work principally between main depots equipped with loading banks and/or mechanical handling units, but provision has been made within the 35 ft. overall length of the outfit for a U.S. Industries tail-lift to be installed if this proves necessary. The bodies themselves are 25 ft. long internally, 7 ft. wide and 6 ft. high.
Although Sainsbury's TK rigids are already a familiar sight on the roads, and have drawn favourable comment for the neat, easy-to-clean contours of the semiLuton body, they incorporate several novel and very practical features.
Like the arties, the 734-cu.-ft. rigid van bodies have interior roof trunking with spaced outlet shutters for the cooling air (from Thermo King HP units in this instance), and body construction and equipment are generally similar. But since they are used to deliver from Sainsbury's depots to the company's retail shops (each of which gets a daily delivery of perishables) they encounter more varied unloading conditions than will be met by the new attics. Some shops have loading banks, others do not, and the latter pose the problem of unloading pallets weighing up to 15 cwt. Without a tailboard, the operator has no more than toe-space at the rear of the loaded vehicle, whereas incorporation of a conventional tailboard would add anothermajor joint to be temperature-sealed.
A solution has been devised by Sainsbury's transport engineers dept. and Bonallack, whose tailplatform design is another feature now standardized on the rigid boxvans. This is a top-hinged alloy tailboard carried vertically on brackets on the rear face of the body, low enough to be clear of the full-depth doors. Swung-up to the horizontal, it formsan extension of the body floor, being held in place by two tubular pull-and-twist supports housed under the body. A short alloy ladder is rigidly fixed to the rear edge of the tailboard, this swinging into place as the flap is hinged upwards. The driver can now bring his loaded pallets back to the tailboard and unload from there, usually passing the goods to a porter's trolley or barrow.
Door Details At the outer edges of the tailboard are upward-facing channels which form slots to hold the main doors paral:el with the body sides when required; the doors can alternatively be folded flat against the body sides. Securing of the doors when shut has been given a lot of thought and although a fairly conventional general layout—vertical rods engaging with top and bottom sock ets---is employed, the rods are moved by pegs engaging in snail cams formed in a plate which pivots on the tight-hand door: Welded to the plate are two handlebars which give the operator good leverage when he is forcing the doors shut against the insulation seal while simultaneously turning the pivoted plate to drive the locking rods home. When home, a lug on the plate coincides with a lug on the door, enabling a padlock hasp to be slipped through and snapped shut. A snail cam is also used at the top of the right-hand door to switch on the interior body lighting automatically as the door opens.
Such careful detail design is typical of the specification of both the rigids and the allies. Having studied both refrigeration and operation very thoroughly, Sainsbury's (who run about 300 C-licensed vehicles in all) now know exactly what they want from their cold vans, and are getting it.