HOW IT IS DONE.
Page 123
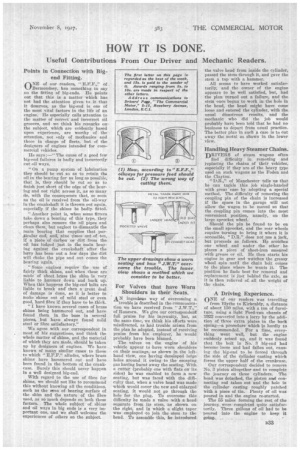
If you've noticed an error in this article please click here to report it so we can fix it.
Useful Contributions From Our Driver and Mechanic Readers.
Points in Connection with Bigend Fitting.
ONF of our readers, " E.F.F.," of Bermondsey, has something to say on the fitting of big-ends. He points out that this is a matter which has not had the attention given to it that it deserves, as the big-end is one of the most vital factors in the life of an engine. He especially calls attention to the matter of correct and incorrect oil grooves, and we think his remarks on the subject, which are evidently based upon experience, are worthy of the attention, not only of mechanics and those in charge of fleets, but of the designers of engines intended for commercial vehicles.
He says :—" The cause of a good few big-end failures is badly and incorrectly cut oil ways.
" On a pump system of lubrication they should be cut so as to retain the oil in the bearing for as long as possible, that is, they Mould be cut so as to finish just short of the edge of the bearing and not right across it, as so many do, with the consequence that, so soon as the oil is received from the oil-way in the crankshaft it is thrown out again, especially if the shims be badlyfitted.
" Another point is, when some fitters take down a bearing of this type, they perhaps also remove the oil pipes and clean them, but neglect to dismantle the main bearing that supplies that particular end, and, nine times out of ten, if a piece of carbon or dirt from the oil has lodged just in the main bearing against the crankshaft after the lorry has been out a few days the dirt will choke the pipe and out comes the bearing again.
" Some engines require the use of fairly thick shims, and when these are made• of sheet brass the shim is very liable to hammer down and buck up. When this happens the big-end bolts are liable to break and then agreat deal of damage is done, so it is better to make shims ant of mild steel or even good, hard fibre if they have to be thick.
"I have known several cases of brass shims being hammered oat, and have found them in the base in several pieces, but have always found mild steel or fibre satisfactory."
We agree with our correspondent in most of his suggestions, and think the whole matter of shims, and the material of which they are made, should be taken up by designers of engines. We have known of many similar cases to those to which "E.F.F." alludes, where brass shims have hammered out and have been found in the bottom of the crankcase. Surely this should never happen in a well designed big-end.
• With regard to the use of fibre for shims, we should not like to recommend this without knowing all the conditions, such as the area of bearing surface of the shim and the nature of the ffbre used, as so much depends on both these factors. The whole subject of shims and oil ways in big ends is a very important one, and we shall welcome the experiences of others on the subject.
For Valves that have Worn Shoulders in their Seats.
AN ingenious way of overcoming a trouble is described in the communication we have received from " J.W.T.," of Runcorn. We give our correspondent full praise for his ingenuity, but, at the same time, we think his efforts were misdirected, as had trouble arisen from the plan he adopted, instead of receiving praise from his employer, he would probably have been blamed.
The valves on the engine of his vehicle appear to -have worn shoulders on their scatings, as shown in the lefthand view, one having developed large holes around it owing to the escaping gas having burnt away the seating. With a cutter (probably one with flats on its sides) he was enabled to form lt new seating, but was faced with the difficulty that, when a valve head was made which would cover the new and enlarged seating, it would not go through the hole for the plug. To overcome this difficulty he made a valve with a head• separate from its stem, as shown on the right, and in which a slight taper was employed 'to join the stem to the head. To assemble this, he introduced the valve head from inside the cylinder, passed the stem through it, and gave the stem a tap with a hammer.
All seems to have worked satisfactorily, and the owner of the engine appears to be well satisfied, but, had the plan turned out a failure, and the stein once beeuu to work in the hole in the head, the head might have come loose and entered the cylinder, with the usual disastrous results, and the mechanic who did the job would probably have been told that he had no business to depart from usual practice. The better plan in such a ease is to eta away the metal as shown in the lower view.
Handling Heavy Steamer Chains.
DRIVERS of steam wagons often find difficulty in removing and replacing the chains of their vehicles, especially if they are of the heavy type used on such wagons as the Foden and the Clayton.
"D.R.," of Manchester tells us that he can taelde this job single-handed with great • ease by adopting a special method. The difficulty of removing the coupling pin of the chain is increased if the space in the garage will not allow the wagon to be moved so that the coupling pin comes into the most convenient position, namely, on the large sprocket wheel.
Should the pin be found to be on the small sprocket, and the rear wheels require turning to bring it where it is accessible, "DR." does not use a jack, but proceeds as follows. He scotches one wheel and under the other he places a piece of sheet-iron smeared with grease or oil. He then starts his engine in gear and watches the greasy wheel spin until the chain bolt comes to the place where he wants it. The position he finds best for removal and replacement is just behind the axle, as it is then relieved of all the weight of the chain.
A Driving Experience.
ONE a our readers was travelling
from Illythe to Kirkcaldy, a, distance of about 130 miles, with a ton of furniture, using a light Ford-van chassis of 1922 converted into a lorry by the addition of three extra plates in the back spring—a procedure which is hardly to be recommended, For a time, everything went well, but the engine suddenly seized up, and it was found that the bolt in No. 3 big-end had become loose and had fallen out, causing the big-end to be forced through the side of the cylinder casting which forms the upper half of the crankcase.
Our correspondent decided to remove No. 3 piston altogether and to complete the journey on three cylinders. The head was detached, the piston awl connecting rod taken out and the hole in the cylinder casting roughly patched with a piece of tin. Plenty of oil was poured in and the engine re-started.
The 55 miles forming the rest of the journey were completed quite satisfactorily. Three gallons of oil had to be poured into the engine to keep it going. ,