• A well-serviced turbo will not It you down
Page 42

Page 43
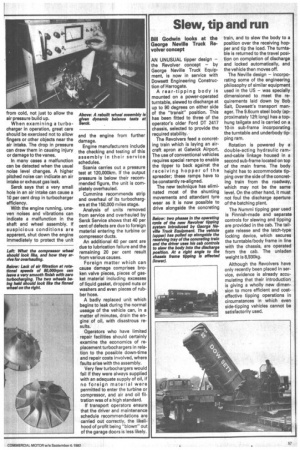
If you've noticed an error in this article please click here to report it so we can fix it.
Neglect your turbo and you'll be in trouble. Bryan Jarvis explains what can go wrong and how to ensure it doesn't
MAINTENANCE of turbochargers is generally carried out on the basis of when it develops a fault, change it." Provided that the driver follows the correct start up — shut down procedure and the recommended service maintenance is carried out correctly, there is every likelihood of it lasting the life of the engine.
However, when I visited Serck Services' turbocharger overhaul department at Redd itch I learned that this is not always the case.
Serck's overhaul facility handles up to 250 units per month. Among these are positive examples of oil starvation, prolonged lack of air filtration and faulty overhaul.
Major problems arise when there is a reduced or a non-lubricating oil flow, when the oil is contaminated, when there is no air filtration or when foreign material enters the air or exhuast systems. Poor workmanship and faulty parts also contribute.
The result can be heavy downtime costs if a faulty unit allows oil to escape into the exhaust to produce excessive black smoke.
In simple terms the turbocharger is a type of air pump which takes air at atmospheric pressure, compresses it and passes it into the cylinders via the inlet valves.
It operates by utilising the exhaust gases to drive a turbine wheel which is connected to a compressor wheel by a shaft. The compressor or air wheel sucks in air through the air filters and passes it into the engine. The expelled exhaust gases are directed to the turbine or hot wheel of the turbocharger and so complete the cycle.
Turbochargers revolve at very high speeds. A unit which rotates at 80,000rpm can have a compressor blade tip speed of 700mph and it rotates long after the engine has stopped.
Mechanics have been known to lose finger tips in discovering this.
At these very high turbocharger speeds it is essential that oil is delivered at the correct pressure and flow rate in order to lubricate the bearings and carry away excessive heat.
It is wrong to assume that oil filters remove foreign material before the oil reaches the turbocharger bearings. Dave Harlock, product manager at Serck Services, warns that these bearings are very likely to fail before the engine main bearings if the engine oil is contaminated.
Although oil technology has gone a long way towards providing good oil, the high temperatures present in modern diesel engines help to break down the oil, producing oxidisation, acids and sludge which all have detrimental effects on the turbocharger. Unburnt fuel and water also assist in breaking down oil.
Any material which enters the oil filtration and exhaust systems will undoubtedly affect the turbocharger and the engine.
To avoid a costly replacement operation from a failed unit or a resultant damaged engine, manufacturers lay down the correct procedures for drivers and service maintenance.
With lower early morning temperatures just around the corner, drivers of vehicles with supercharged engines should get the habit of allowing the engine to idle for several minutes from cold, not just to allow the air pressure build up.
When examining a turbocharger in operation, great care should be exercised not to allow fingers or other objects near the air intake. The drop in pressure can draw them in causing injury or damage to the vanes.
In many cases a malfunction can be detected when the usual noise level changes. A higher pitched noise can indicate an air intake or exhaust gas leak.
Serck says that a very small hole in an air intake can cause a 10 per cent drop in turbocharger efficiency.
With the engine running, uneven noises and vibrations can indicate a malfunction in the shaft and wheel assembly. If suspicious conditions are apparent, shut down the engine immediately to protect the unit and the engine from further damage.
Engine manufacturers include the checking and testing of this assembly in their service schedules.
Scania carries out a pressure test at 120,000km. If the output pressure is below their recommended figure, the unit is completely overhauled.
Cummins recommends strip and overhaul of its turbochargers at the 150,000 miles stage.
Analysis of units removed from service and overhauled by Serck Service shows that 40 per cent of defects are due to foreign material entering the turbine or compressor ducts.
An additional 40 per cent are due to lubrication failure and the remaining 20 per cent result from various causes.
Foreign matter which can cause damage comprises broken valve pieces, pieces of gasket material including excesses of liquid gasket, dropped nuts or washers and even pieces of rubber hose.
A badly replaced unit which begins to leak during the normal useage of the vehicle can, in a matter of minutes, drain the engine of oil, with disastrous results.
Operators who have limited repair facilities should certainly examine the economics of replacement turbochargers in relation to the possible down-time and repair costs involved, where faults arise with the assembly.
Very few turbochargers would fail if they were always supplied with an adequate supply of oil, if no foreign material were permitted to enter the turbine or compressor, and air and oil filtration was of a high standard.
If transport operators ensure that the driver and maintenance schedule recommendations are carried out correctly, the likelihood of profit being "blown" out of the garage doors is less likely.