Specifying success
Page 132
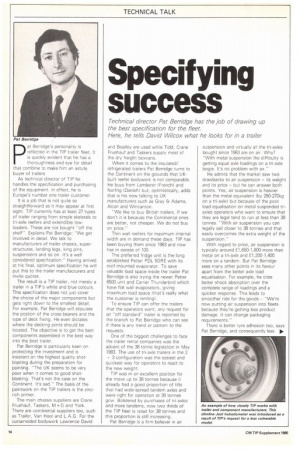
Page 135
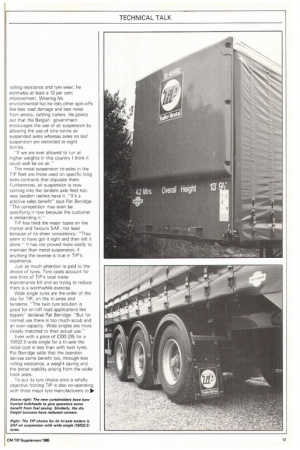
Page 138
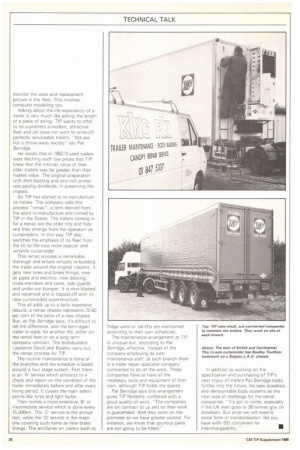
If you've noticed an error in this article please click here to report it so we can fix it.
Technical director Pat Berridge has the job of drawing up the best specification for the fleet.
Here, he tells David Wilcox what he looks for in a trailer
Pat Berridge's personality is reflected in the TIP trailer fleet. It is quickly evident that he has a thoroughness and eye for detail that combine to make him an astute buyer of trailers.
As technical director of TIP he handles the specification and purchasing of the equipment. In effect, he is Europe's number one trailer customer.
It is a job that is not quite so straightforward as it may appear at first sight. TIP currently has at least 27 types of trailer ranging from simple skeletals to tri-axle reefers and extendible lowloaders. These are not bought "off the shelf". Explains Pat Berridge: "We get involved in detail. We talk to manufacturers of trailer chassis, superstructures, landing legs, king pins, suspensions and so on, it's a well considered specification:" Having arrived at his final, optimum specification he will put this to the trailer manufacturers and invite quotes.
The result is a TIP trailer, not merely a trailer in a TIP's white and blue colours. This specification does not just cover the choice of the major components but gets right down to the smallest detail. For example, Pat Berridge will stipulate the postion of the cross-bearers and the type of deck fixing. He even dictates where the decking joints should be located. The objective is to get the best components assembled in the best way into the best trailer.
Pat Berridge is particularly keen on protecting the investment and is insistent on the highest quality shotblasting during the preparation for painting. "The UK seems to be very poor when it comes to good shotblasting. That's not the case on the Continent. It's sad." The basis of the paintwork on the TIP trailers is the zincrich primer.
The main chassis suppliers are Crane Fruehauf, Taskers, M +G and York. There are continental suppliers too, such as Trailor, Van Hool and L.A.G. For the curtainsided bodywork Lawrence David and Boalloy are used while Tidd, Crane Fruehauf and Taskers supply most of the dry freight boxvans.
When it comes to the insulated/ refrigerated trailers Pat Berridge turns to the Continent on the grounds that UKbuilt reefer bodywork is not comparable. He buys from Lamberet (French) and Norfrig.(Danishl but, optimistically, adds that is his now talking to UK manufacturers such as Gray Er Adams, Aldan and Wincanton.
"We like to buy British trailers. If we don't it is because the Continental ones are better, not cheaper. We do not buy on price."
Thin wall reefers for maximum internal width are in demand these days. TIP has been buying them since 1983 and now has in excess of 100.
The preferred fridge unit is the long established Petter PDL SORE with its roof-mounted evaporator. To save valuable load space inside the trailer Pat Berridge is also trying the newer Petter 6500 unit and Carrier Thunderbird which have flat wall evaporators, giving maximum load space (that's really what the customer is renting).
To ensure TIP can offer the trailers that the operators want, any request for an "off standard" trailer is reported by the branch to Pat Berridge who can see if there is any trend or pattern to the requests.
One of the biggest challenges to face the trailer rental companies was the advent of the 38 tonne legislation in May 1983. The use of tri-axle trailers in the 2 + 3 configuration was the easiest and quickest way for operators to react to the new weight.
TIP was in an excellent position for the move up to 38 tonnes because it already had a good proportion of tilts that had wide-spread tandem axles and were right for operation at 38 tonnes gcw. Bolstered by purchases of tri-axles and more tandems, now two thirds of the TIP fleet is rated for 38 tonnes and this proportion is still increasing.
Pat Berridge is a firm believer in air suspension and virtually all the tri-axles bought since 1983 are on air. Why? "With metal suspension the difficulty is getting equal axle loadings on a tri-axle bogie. It's no problem with air."
He admits that the market saw two drawbacks to air suspension its weight and its price but he can answer both points. Yes, air suspension is heavier than the metal equivalent (by 250-270kg on a tri-axle) but because of the poor load equalisation on metal suspended triaxles operators who want to ensure that they are legal tend to run at less than 38 tonnes. "With air suspension you can legally sail closer to 38 tonnes and that easily overcomes the extra weight of the suspension."
With regard to price, air suspension is typically around £1,650-1,800 more than metal on a tri-axle and £1,200-1,400 more on a tandem. But Pat Berridge sees many other points in its favour apart from the better axle load equalisation. For example, he cites better shock absorption over the corriplete range of loadings and a quicker response. This leads to smoother ride for the goods "We're now putting air suspension into fleets because they're getting less product damage. It can change packaging requirements."
There is better tyre adhesion too, says Pat Berridge, and consequently less 111. rolling resistance and tyre wear; he estimates at least a 10 per cent improvement. Wearing his environmental hat he lists other spin-offs like less road damage and less noise from empty, rattling trailers, He points out that the Belgian government encourages the use of air suspension by allowing the use of nine tonne air suspended axles whereas axles on leaf suspension are restricted to eight tonnes.
"If we are ever allowed to run at higher weights in this country I think it could well be on air."
The metal suspension tri-axles in the TIP fleet are those used on specific long term contracts that stipulate them. Furthermore, air suspension is now coming into the tandem axle fleet too; new tandem reefers have it. "It's a positive sales benefit" says Pat Berridge. "The competition may even be specifying it now because the customer is demanding it."
TIP has tried the major types on the market and favours SAF, not least because of its sheer consistency: "They seem to have got it right and then left it alone." It has not proved more costly to maintain than metal suspension; if anything the reverse is true in TIP's. experience.
Just as much attention is paid to the choice of tyres. Tyre costs account for one third of TIP's total trailer maintenance bill and so trying to reduce them is a worthwhile exercise.
Wide single tyres are the order of the day for TIP, on the tri-axles and tandems. "The twin tyre solution is good for on/off road applications like tippers" declares Pat Berridge. "But for normal use there is too much scrub and an over-capacity. Wide singles are more closely matched to their actual use."
Even with a price of £200-235 for a 15R22.5 wide single for a tri-axle the initial cost is less than with twin tyres. Pat Berridge adds that the operator derives some benefit too, through less rolling resistance, a weight saving and the better stability arising from the wider track axles.
To put its tyre choice onto a wholly objective footing TIP is also co-operating with three major tyre manufacturers to Ili. monitor the wear and replacement picture in the fleet. This involves computer modelling too.
Asking about the life expectancy of a trailer is very much like asking the length of a piece of string. TIP wants to offer to its customers a modern, attractive fleet and yet does not want to write-off perfectly serviceable trailers. "We are not a throw-away society" say Pat Berridge.
He recalls that in 1982/3 used trailers were fetching such low prices that TtP knew that the intrinsic value of their older trailers was far greater than their market value. The original preparation with shot-blasting and zinc-rich primer was paying dividends, in preserving the chassis.
So TIP has started to re-manufacture its trailers. The company calls this process "remac", a term derived from the word re-manufacture and coined by TIP in the States. The trailers coming in for a remac are the older tilts and flats and they emerge from the operation as curtainsiders. In this way TIP also switches the emphasis of its fleet from the tilt to the now more popular and versatile curtainsider.
This remac process is remarkably thorough and entails virtually re-building the trailer around the original l-beams. It gets new tyres and brake linings, new air pipes and electrics, new decking, cross-members and raves, side guards and under-run bumper. It is shot-blasted and repainted and is topped-off with its new curtainsided superstructure.
This all adds up to a fairly expensive rebuild; a remac chassis represents 70-80 per cent of the price of a new chassis But, as Pat Berridge says, it's difficult to tell the difference, and the born-again trailer is ready for another life, either on the rental fleet or on a long term company contract. The bodybuilders Lawrence David and Boalloy carry out the remac process for TIP.
The routine maintenance is done at the branches and the schedule is based around a four stage system. First there is an 'A' service which amounts to a check and report on the condition of the trailer immediately before and after every hiring period. It covers the main safety points like tyres and light bulbs.
Then comes a more extensive 'B' or intermediate service which is done every 15,000km. The 'C' service is the annual test, while the 'D' service is the major one covering such items as new brake linings. The ancillaries on trailers such as fridge units or tail-lifts are maintained according to their own schedules.
The maintenance arrangement at TIP is unusual but, according to Pat Berridge, effective. Instead of the company employing its own maintenance staff, at each branch there is a trailer repair specialist company contracted to do all the work. These companies have to have all the necessary tools and equipment of their own, although TIP holds the spares.
Pat Berridge says this arrangement gives TIP flexibility combined with a gaud quality of work. "The companies are on contract to us and so their work is guaranteed. And they work on the premises so we have greater control. For instance, we know that spurious parts are not going to be fitted." In addition to working oil the specification and purchasing of TIP's next imput of trailers Pat Berridge looks further into the future. He sees drawbars and demountable body systems as the next area of challenge for the rental companies. "It's got to come, especially if the UK ever goes to 38 tonnes gtyv on drawbars. But what we will need is some form of standardisation like you have with ISO containers for interchangeability."