Autogenous Welding by Means of the Oxy Acetylene Blowpipe.
Page 21
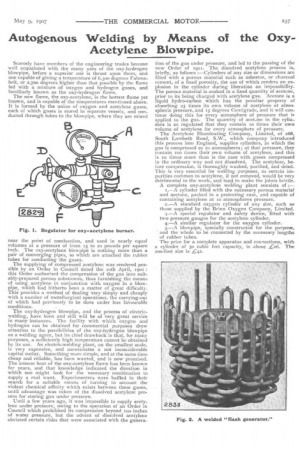
Page 22
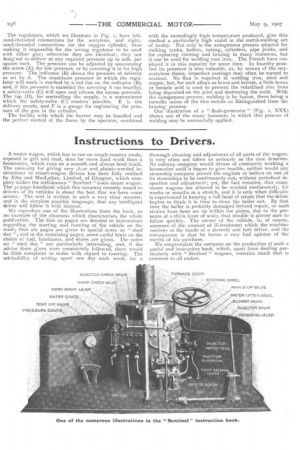
If you've noticed an error in this article please click here to report it so we can fix it.
Scarcely have members of the engineering trades become well acquainted with the many uses of the ox-hydrogen blowpipe, before a superior one is thrust upon them, and one capable of giving a temperature of 6,300 degrees Fahrenheit, or 2,700 degrees higher than that possible by the flame fed with a mixture of oxygen and hydrogen gases, and familiarly known as the oxy-hydrogen flame. The new flame, the oxy-acetylene, is the hottest flame yet known, and is capable of the temperatures mentioned above. It is formed by the union of oxygen and acetylene gases, each of which gases is stored in separate vessels, and conducted through tubes to the blowpipe, where they are mixed near the point of combustion, and used in nearly equal volumes at a pressure of from 15 tO 20 pounds per square inch. The oxy-acetylene blowpipe is nothing more than a pair of converging pipes, to which are attached the rubber tubes for conducting the gases. The supplying of compressed acetylene was rendered possible by an Order in Council dated the loth April, 1901 : this Order authorised the compression of the gas into suitably-prepared porous substances, thus furnishing the means of using acetylene in conjunction with oxygen in a blowpipe, which had hitherto been a matter of great difficulty. This provides a method of dealing very simply and cheaply with a number of metallurgical operations, the carrying-out of which had previously to be done under less favourable conditions.
The oxy-hydrogen blowpipe, and the process of electricwelding, have been and still will be of very great service in many instances. The facility with which oxygen and hydrogen can be obtained for commercial purposes drew attention to the possibilities of the oxy-hydrogen blowpipe as a welding agent, but its chief drawback is that, for many purposes, a sufficiently high temperature cannot be obtained by its use. An electric-welding plant, on the smallest scale, is very expensive, and necessitates a not inconsiderable capital outlay. Something more simple, and at the same time cheap and reliable, has been wanted, and is now promised. The intense heat of the oxy-acetylene flame has been known for years, and that knowledge indicated the direction in which one might look for the necessary combination to supply a real want. Experimenters were balled in their search for a suitable means of turning to account the violent chemical affinity which exists between these gases, until advantage was taken of the dissolved acetylene process for storing gas under pressure.
Until a few years ago, it was impossible to supply acetylene under pressure, owing to the operation of an Order in Council which prohibited its compression beyond too inches of water pressure, but the advent of dissolved acetylene obviated certain risks that were associated with the genera tion of the gas under pressure, and led to the passing of the new Order of 1901. The dissolved acetylene process is, briefly, as follows :—Cylinders of any size or dimensions are filled with a porous material such as asbestos, or charcoal cement, of a fixed porosity, the use of which renders an explosion in the cylinder during liberation an impossibinty. The porous material is soaked in a fixed quantity of acetone, prior to its being charged with acetylene gas. Acetone is a liquid hydro-carbon which has the peculiar property of absorbing 25 times its own volume of acetylene at atmospheric pressure, and is degrees Centigrade, and it will continue doing this for every atmosphere of pressure that is applied to the gas. The quantity of acetone in the cyliaders is so regulated that they contain to times their own volume of acetylene for every atmosphere of pressure.
The Acetylene illuminating Company, Limited, of 268, South Lambeth Road, S.W., which company introduced this process into England, supplies cylinders, in which the gas is compressed to to atmospheres; at that pressure, they contain too times their own volume of acetylene, and this is to times more than is the case with gases compressed in the ordinary way and not dissolved. The acetylene, before compression, is thoroughly washed, purified, and dried. This is very essential for welding purposes, as certain impurities common to acetylene, if not removed, would be very detrimental to the work, and tend to make the joints brittle.
A complete oxy-acetylene welding plant consists of :— I.—A cylinder filled with the necessary porous material
and acetone, packed in a protecting case, and capable of
containing acetylene at to atmospheres pressure.
2.—A standard oxygen cylinder of any size, such as those supplied by the Brinn Oxygen Company, Limited.
1.—A special regulator and safety device, fitted with two pressure gauges for the acetylene cylinder.
4.—A similar regulator for the oxygen cylinder.
5.—A blowpipe, specially constructed for the purpose, and the whole to be connected by the necessary lengths of rubber tubes.
The price for a complete apparatus and connections, with a cylinder of so cubic feet capacity, is about The zoo-foot size is 42.
The regulators, which we illustrate in Fig, t, have leftland-threaded connections for the acetylene, and rightnand-threaded connections for the oxygen cylinder, thus tnaking it impossible for the wrong regulator to be used with either gas; otherwise they are identical; they are desig3ed to deliver at any required pressure up to 2o1b. per square inch. The pressure can be adjusted by unscrewing the screw (A), for low pressure, or by screwing it in for high pressure. The indicator (B) shows the pressure of delivery as set by A. The maximum pressure at which the regulator will work is marked by a red line on the indicator (B), and, if this pressure is exceeded (by screwing A too heavily), a safety-valve (C) will open and release the excess pressure. The tap (D), for controlling the supply, is a convenience which the safety-valve (C) renders possible. E is the delivery nozzle, and F is a gauge for registering the pressure of the gas in the cylinder.
The facility with which the burner may be handled and the perfect control of the flame by the operator, combined with the exceedingly high temperature produced, give this method a particularly high stand in the metal-welding art of to-day. Not only is the autogenous process adapted for making tanks, boilers, tubing, cylinders, pipe joints, and for replacing riveting and brazing in many instances, but it can be used for welding cast iron. The French have employed it in this capacity for some time. In foundry practice its presence is also valuable, as, by means of the oxyacetylene flame, imperfect castings may often be turned to account. No flux is required in welding iron, steel and copper, but, for such alloys as brass and bronze, a little borax or boracic acid is used to prevent the volatilised zinc from being deposited on the joint and destroying the weld. With the autogenous process, welding is by fusion, there being a metallic union of the two metals as distinguished from the brazing process.
Our illustration of a " flash-generator " (Fig. 2, XXX) shows one of the many instances in which this process of welding may be successfully applied.