NEW PARTS FROM Oil ELECTRO-DEPOSITION
Page 26
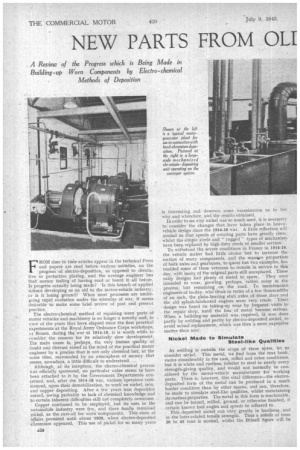
Page 27
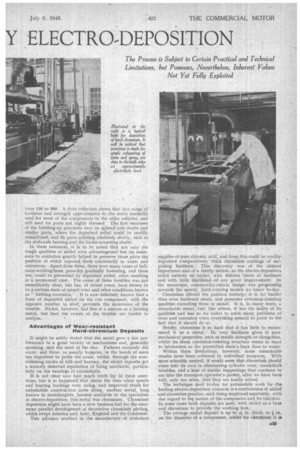
Page 28
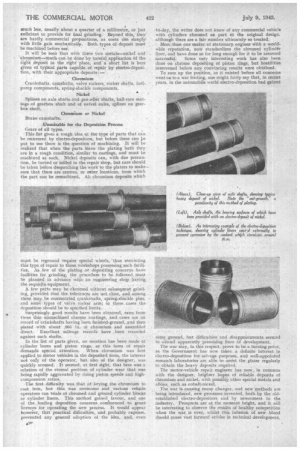
If you've noticed an error in this article please click here to report it so we can fix it.
A Review of the Progress which is Being Made in Building-up Worn Components by Electro chemical Methods of Deposition The Process is Subject to Certain Practical and Technical Limitations, but Possesses, Nevertheless, Inherent Values Not Yet Fully Exploited
FROM time to tinie articles appear in the technical Press and papers are read before various societies, on the progress of electro-deposition, as opposed to decorative or protective plating, and the average engineer has that uneasy feeling of having read or heard it all before. Is progress actually being made? Is this branch of applied science developing as an aid to the motor-vehicle industry, or is it losing ground? When most processes are undergoing rapid evolution under the stimulus of war, it seems desirable to make some brief review of past and present practice.
The electro-chemical method of repairing worn parts of motor vehicles and machinery is no longer a novelty and, in view of the years that have elapsed since the first practical experiments at the Royal Army Ordnance Corps workshops, at Rouen, during the war of 1914-18, it is worth while to consider the reasons for its relatively. slow • development. The main cause is, perhaps, the very human quality of doubt and distrust raised hi the mind of the practical motor engineer by a process that is not only chemical hilt, at the same time, surrounded by an atmosphere of secrecy that seems, nowadays, a little difficult to understand. ..
. Although, at its inception, the electro-chemical process was officially sponsored, no particular value seems to have been attached to it by the Government Department's concerned, and, after the 1914-18 war, various operators commenced, upon their demobilization, to work-on nickel, iron, and copper depositing. After a few years iron deposition ceased, owing probably to lack of chemical knowledge and to certain inherent difficulties still not completely overcome.
Copper continued to he employed, but its uses in the automobile industry were few, and there finally remained nickel, as the cure-all for Worn 'components. This state of affairs persisted until abbut 1928, when electro-deposited chromium appeared. This use of nickel for so many years is interesting and deserves some examination as to the why and wherefore, and the results obtained. • In order to sec why nickel was so much used, it is necessary to consider the changes that have taken place in heavyvehicle design since the 1914-18 war. A little reflection will remind us that speeds of rotating parts have greatly risen,. whilst the -simple steels and " rugged " types of mechanism have been replaced by high-duty steels of smaller section.
To withstand the severe conditions in France in 1914-18, the vehicle maker had little choice but to increase the section of many components, and the massiye proportion of baCk axles and gearboxes, to quote but two examples, has enabled some of these veterans to remain in serviceto this . day, with Many. of the original.parts still unreplaced. These early 'designs had 'plenty of metal to spare. V They were intended to wear, growing, perhaps, rather. noisy in the process, but remaining , on -.the road. To maintenance engineers of to-day, who think in terms of a few thousandths of an inch; the plain-bearinz stub axles of those days and the old splash-lubricated engines seem Very crude. Their design was based on taking-up Wear by frequent visits to the repair shop, Until the loss of metal became serious, When a bailding-up material was.required, it was done partly by welding and partly by electro-deposited nickel, to avoid actual replacement, which was then a more, expensive matter -than now.
Nickel Made to Simulate Steel-like Qualities
As welding isoutside the scope of these notes, let us consider nickel. This metal, we find from the text book, varies considerably in the cast, rolled and other conditions. but it is white and rustless, inferior to steel in nearly every strength-giving quality, and Would not normally be cons sidered by the motor-vehicle manufacturer for working parts. There is, however, this vital difference—the tlectrodeposited form of the metal can be produced in a much harder condition than by other means, and Gan, therefore, be made to simulate steel-like qualities, whilst maintaining its rustless properties. The metal in this form is machinable, and can be turned, milled, ground, or otherwise finished, if certain known tool angles and speeds be adhered to.
This deposited nickel can vary greatly in hardness, and in the inter-related tensile strength. Thus a tensile of from 30 to 45 tons is normal, whilst the Brinell figure will be from 130 to 300. A little reflection shows that this range of hardness and strength approximates to .the steels normally used for most of the components in the older vehicles, and still used for parts not highly stressed. The first successes of the building-up processes were on splined: axle shafts and similar parts, where the deposited metal could be readily remachined, and ttn parts rotating relatively slowly, such as the stub-axle bearing and the brake-actuating shafts'.
In these instance, it is to be noted that not only the tough qualities of nickel were advantageous$, but its resistance to oxidation greatly helped to preserve those peirts the position of which exposed them continuall3i to water and corrosives. Apart from these, there were many cases of ballraces working loose, press-fits gradually loosening, and these too, could be prevented by deposited nickel, often.resulting in a permanent cure. The cause of these troubles was .not immediately clear, but has, of recent years, been shown to be a curious state of mixed wear and other conditions known as " fretting corrosion." it is now definitely known that a layer of deposited nickel on the cue component, with the opposite number in steel, prevents the recurrence of the trouble. Nickel, 'however, had less of a success as a bearing metal, but here the causes. of the trouble are harder to analyse.
Advantages of Wear-resistant Hard-chromium Deposits
It might be safely stated that the metal gave a fair performance in a great variety of mechanisms and,generally speaking, .met the need of the day. Failures certainly did occur, and these, as usually happens, in the hands of users too impatient to probe the cause, whilst, through the everwidening circles of talk and hearsay, the nickel deposits got a scarcely deserved reputation of being unreliable, particularly on the bearings of crankshafts.
It is not clear now bow much truth lay in these assertions, but it so happened that about the time when Speeds and bearing loadings were rising, and improved steels for autorinobile construction came along, another metal, long known to metallurgists, became available to the speCialists in electro-deposition; this metal was chromium. Chromium deposition might have beep a slow business but for the enormous parallel development of decorative chromium plating, which swept America and, later, England and the Continent.
This advance resulted in the manufacture -of abundant supplies of pure chromic acid, and from this could be readily deposited comparatively thick chromium coatings of surprising hardness. This discovery was of the utmost importance and of a timely nature, as the electro-depositorsrelied entirely on nickel, with definite limits of hardness and with little likelihood of any great improvement. In the meantime, commercial-vehicle design was progressing towards the speedy, hard-wearing models we know to-day.
Chromium altered the position entirely; it is far harder than even hardened -steels, and possesses corrosion-resisting qualities exceeding those of nickel. It is, in many ways, a remarkable metal, hut, like others, it has the faults of its qualities and has so far failed -to solve many problems of wear and corrosion when everything seemed to point to the fact that it should do so.
Briefly, chromium is so hard that it has little to recommend it as a metal. Its very hardness gives it poor mechanical properties, such as tensile strength or elongation, whilst its. dense corrosion-resisting structure seems to react to lubrication as the proverbial duck's back does to water.
Within these limitations, however, some remarkable resultshave been achieved in individual instances. With more scientific control, it would seem that chromium „should coriie into its own in eliminating cylinder wear, crankshaft troubles, and a host of similar happenings that continue to eat into the transport operator's profits, after we have been told, only too often, that they are Imally solved, • The technique used to-day for automobile work by the leading eiectro-deposition concerns is a combination of nickel and chromitirn practice, each being employed separately, with due regard to the nature of the component and its function.
• In some eases both deposits are used, with nickel as a base and chromium to provide the working face.
The average nickel deposit is up to -116in, thick, or / in. on the diameter of a component, whilst far chromium it ia
much less, usually about a quarter of a millimetre, or just sufficient to provide for final grinding. Beyond this, they are hardly commercial propositions, as costs rise steeply with little gain mechanically. Both types of deposit must be machined before use
It will be seen that with these two metals—nickel and 'ehrotniuni—much can be done by careful application of the right deposit in the right place, and a short list is here given of typical parts capable of repair hy electro-deposition, with their appropriate deposits:—
Chromium Crankshafts, camshafts, valve rockers, rocker shafts, fuelpump components, spring-shackle components.
Nickel .
Splines on axle shafts and proleIler shafts, ball-race seatings of gearbox shaft and of swivel axles, splines on gearbox shaft.
Chromium or Nickel Brake camshafts.
Unsuitable for the Deposition Process Gears of all types.
This list gives a rough idea qt the type of parts that can be recovered by electro-deposition, but before these can he put to use there is the question of machining. It will be realized that when the parts leave the plating bath they are in a rough condition, similar to castings, and must be machined as such. Nickel deposits can, with due precaution, be turned or milled in the repair shop, but care should be taken before despatching the work to the platers to make sure that there are centres, or her locations, from which the part can be remachined. All chromium deposits which
must be reground require special wheels, 'thus restricting this type of repair to those workshops possessing such
As few of the plating or depositing concerns have facilities for grinding, the procedure to he followed must be planned in advance with an engineering . shop haying the requisite equipment.
. A few parts may be chromed without subsequent grind ing, provided that the tolerances are not close, andamong these may be enumerated crankshafts,spring-shackle pins, and some types of .valve rocker a.ruei -in these. cases the
deposition should be to specified limits, ; Surprisingly good results have been obtained, even from these thin unmachined chrome coatings, and. cases are on record of crankshafts having been finished-ground, and then plated with about ,00i in.oi chromium and assembled direct. Excellent mileage records have been recorded against such shafts.
In the list of parts given, no mention has been made ,of cylinder bores and piston rings, as this form of repair demands special. attention. , When chromium was first applied to motor vehicles in the deposited form, the interest not .only of the operator, but also of the designer, was quickly aroused. It seemed, at first sight, that here was a solution of the eteraral problem of cylinder wear that was being rapidly aggravated by rising piston speeds and highcompression ratios.
-The first difficulty was that of keying the chromium to
cast. iron, but this was overcome and . various vehicle operators ran trials of chromed and grOund cylinder blocks or cylinder liners. This method gained favour, and one of the .leading deposition concerns commenced to grant licences for operating the new process. It Would appear howeirer, that practical difficulties, and probably expense, prevented any general adoption of the idea, and, even
• to-day, the writer does not know of any commercial vehicle with cylinders chromed as part of the original design. although there are a fair number ultimately so treated.
More_than one maker-of stationary engines With a worldwide reputation, now standardizes the chromed cylinder liner, and have done so for long enough for it to be assumed successful. Some very interesting work has also been done on chrome depositing of piston rings, but hostilities intervened before any convincing results were obtained.
To sum up the position, as it existed before all concerns went on to a war footing, one might fairly say that, in recent years, in the automobile world electro-deposition had gained sOme, ground, but difficulties, and disappointments. seemed to attend apparently promising lines of development.
The war may, in this respect, prove to be a turning-point, as the Government has now taken a definite interest in electro-deposition foe salvage purposes, and well-appointed . research laboratories are able to assist the plater regularly to obtain the heavy deposits required_ The motor-vehicle repair engineer has now, in common with the designer, brighter .hopes of reliable deposits ofchromium and nickel, with possibly-other special metals and
allays, such as cobalt-nickel. .
The War is causing many changes, and new methods are being introduced, new processes invented.. both_ by the old-established electro-depositors and by newcomers to the industry. Prospects are at the moment bright, and it will be interesting to observe the results of healthy competition when the war is over, whilst this infusion of new blood should cause vast forward strides in technical development.