Metallurgy Aids Production Speed-up
Page 46
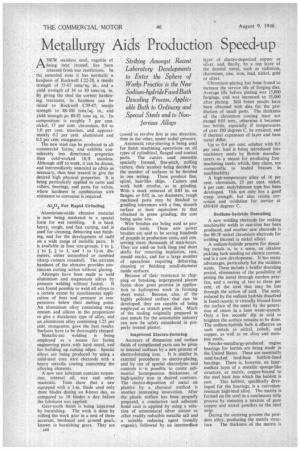
Page 47
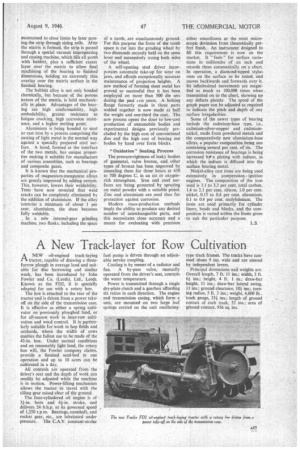
If you've noticed an error in this article please click here to report it so we can fix it.
Striking Amongst Recent Laboratory Developments to Enter the Sphere of Works Practice is the New Sodium-hydrideF used Bath Descaling Process, Applicable Both to Ordinary and .Special Steels and to Non ferrous Alloys
ANEW stainless steel, capable of being heat treated, has been released from war restrictions. In the annealed state it has normally a hardness of Rockwell C22-28, a tensile strength of 55-67 tons/sq. in., and a yield strength of 34 to 50 tons/sq. in. By giving the steel the correct hardening treatment, its hardness can be raised to Rockwell C39-47, tensile strength to 88-100 tons/sq. in., and yield strength 'to 80-93 tons sq. in. Its composition is roughly 7 per cent. nickel, 17 per cent. chromium, 0.4 to 1.0 per cent, titanium, and approximately 0.2 per cent aluminium and 0.5 per cent. manganese.
The new steel can be produced in all commercial forms, and exhibits considerably less directional properties than cold-worked 18/8 stainless. Although stiff to work, it can be drawn, and intermediately annealed as often as necessary, then heat treated to give the desired high physical properties. It is being particularly applied to cams and rollers, bearings, and parts for valves, where hardness in combination with resistance to corrosion is required.
AI203 For Rapid. Grinding
Aluminium-oxide abrasive material is now being marketed in a special
form for wet tumbling. It is hard, heavy, tough, and fast cutting, and is used for cleaning, deburring and finishing, and for the development of radii on a wide range of metallic parts. It is available in four size-groups, I to 1, Ito f, Ito 1, and 1 to 14-in, diameters, either untumbled or tumbled (sharp corners rounded). The extreme hardness of the abrasive provides continuous cutting action without glazing.
Attempts have been made to weld aluminium and magnesium alloys by pressure welding without fusion. It was found possible to weld all alloys to a certain extent by simultaneous application of heat and pressure at temperatures below their melting point. An aluminium alloy containing magnesium and silicon in the proportions to give a duralumin type of alloy; and an aluminium alloy containing 1.25 per cent. manganese, gave the best results. Surfaces have to be thoroughly cleaned.
Metallic-arc welding is being employed as a means for facing engineering parts with hard metal, and for building up cutting edges. Special alloys are being produced by using a mild-steel core wire electrode with a heavy metallic coating containing the alloying elements.
A new saw lubricant contains turpentine, mineral oil, wax and other materials. Tests show that a saw equipped with a 1-in, blade used only three blades during an 8-hour day, as compared to 10 blades a day before the lubricant was applied.
Gear-tooth finish is being improved by burnishing. The work is done by rolling the work gear in a nest of three accurate, hardened and ground gear's, known as burnishing gears. They are "44 caused to revolve first in one direction, then in the other, under radial pressure.
Automatic roto-shaving is being used for finish machining operations on all types of cylindrical, flanged and conical parts. The cutters used resemble specially formed, fine-pitch, milling cutters, their number being decided by the number of surfaces to be finished in one setting. These produce fine, spiral, hair-like chips. Cutters and work both revolve, as in grinding. With a stock removal of 0.01 in. on flanges, or 0.02 in. on diameters, rough machined parts may be finished to grinding tolerances with a fine, smooth surface at least equivalent to that obtained in green grinding, the cost being quite low.
Wire brushes are being used as production tools. These new power brushes are said to be saving hundreds of pounds in production costs, and con. serving many thousands of man-hours. They are used on both long and short shafts for removing insulation, rust, mould marks, and for a large number of operations requiring deburring, cleaning or finishing small-diameter inside surfaces.
Because of their resistance to chipping or breaking, impregnated plaster forms show great promise in application to hydropress work in forming sheet metal. Because, also, of the highly polished surface that can be developed, they are capable of being employed as stretch press dies. Much of the tooling originally prepared in cast metals for the automobile industry can now be safely considered in properly treated plaster.
Improved Electro-forming Accuracy of dimension and surface finish of complicated parts can be given to internal surfaces by a new process of electro-forming iron. It is similar in external procedures to electro-plating, and by use of special electrolytes and controls it is possible to create substantial homogeneous thicknesses of high-quality iron in desired contours. The electro-deposition of metal on plastics by a chemical method is another interesting innovation. After the plastic surface has been properly prepared, a conductive and adherent bond coat is applied by using a solution of ammoniacal silver nitrate or other readily reducible metallic salt and a suitable reducing agent (usually organic), followed by an intermediate layer of eleoro-deposited copper or silver, and, finally, by a top layer of the desired metal, such as cadmium, chromium, zinc, iron, lead, nickel, gold or silver.
Chromium-plating has been found to increase the service life of forging dies. Average life before plating was 15,000 forgings, and was increased to 35,000 after plating. Still better results have been obtained with dies for the production of small parts. The thickness of the chromium coating must not exceed 0.03 mm., otherwise it becomes too brittle, especially if temperatures of over 100 degrees C. be attained, and if thermal expansion of layer and base metal differ.
Up to 0.4 per cent. sulphur with 0.5 per cent. lead is being introduced into machinery steels by British manufacturers as a means for producing freemachining steels, which, they claim, are comparable to leaded brasses in mach ina bil ity.
A high-temperature alloy of 16 per cent. chromium, 25 per cent. nickel, 6 per cent. molybdenum type has been developed. This not only has a good creep strength, but also resists corrosion and oxidation for service at 650-810 degrees C'.
Sodium-hydride Descaling A new welding electrode for making machinable welds in cast-iron has been produced, and another new electrode is the 80-20 nickel chromium electrode for welding Inconel M nickel alloy).
A sodium-hydride process for descaling metals is, in a sense, an alkaline pickling bath needing no electric current, and is a new development. It has many advantages, particularly for the stainless steels. These include a briefer descaling period, elimination of the possibility of pitting the metal through careless practice, and a saving of two to three per cent. of the steel that may be lost through the action of acid. The scale, reduced by the sodium hydride dissolved in fused caustic, is virtually blasted from the surface of the metal by the generation of steam in a later water-quench. Only a few seconds' dip in acid to brighten the surface remains to be done. The sodium-hydride bath is effective on such metals as nickel, cobalt, and copper, as well as on alloy and stainless steels.
Powder-metallurgy-produced engine bearings for lorries are being made in the United States. These are essentially steel-backed lead-base babbitt-lined bearings. There is, however, an intermediate layer of a metallic sponge-like structure, or matrix, copper-brazed to the steel back into which the babbitt is
cast. This babbitt, specifically developed for the bearings, is a corrosionresistant high-lead alloy. The matrix is formed on the steel in a continuous strip process by sintering a mixture of pure copper and nickel powders to the steel strip.
During the sintering process the powders alloy, producing the matrix struc ture. The thickness of the matrix is maintained to close limits by later passing the strip through sizing rolls. After the matrix is formed, the strip is passed through a special vacuum impregnating and casting machine, which fills all porell with babbitt, plus a sufficient excess layer over the matrix to allow final machining of the bearing to finished dimensions, holding an extremely thin overlay over the matrix surface in the finished bearing.
The babbitt alloy is not only bonded chemically, but because of the porous nature of the matrix, is held mechanically in place. Advantages of the bearing are high conformability, high embedability, greatei resistance to fatigue cracking, high corrosion resistance, and a higher melting point.
Aluminium is being bonded to steel or cast iron by a process comprising the casting of light metal in the normal way against a specially prepared steel surface. A bond, formed at the interface of the two metals, has unique properties making it suitable for manufacture of various assemblies, such as bearings and composite gears.
It is known that the mechanical properties of magnesium-manganese alloys are greatly improved by adding cerium. This, however, lowers their weldability. Tests have now revealed that weld cracks can be completely eliminated by the addition of aluminium. if the alloy 'contains a minimum of about • 1 per cent. aluminium, the sheet becomes fully weldable.
In a new internal-gear grinding machine, two flanks, including the space of a tooth, are simultaneously ground. For this purpose the form of the tooth space is cut into the grinding wheel by two diamonds securely held on the same lever and successively truing both sides of the wheel.
A self-opening stud driver incorporates automatic take-up for wear on jaws, and affords exceptionally accurate maintenance -of projection heights. A new method of forming sheet metal has proved so successful that it has been employed on more than 500 die sets during the past wo years. A bolting flange formerly made in three parts welded together is now made at half the weight and one-third the cost. The new process opens the door to low-cost production of automobile bodies and experimental designs previously precluded by the high cost of conventional dies and the high cost of beating out bodies by hand over form blocks.
"Oxidation" Sealing Process The pressure-tightness of leaky bushes of gunmetal, valve bronze, and other types of bronze has been improved by annealing them for three hours at 650 to 700 degrees C. in an air or oxygenrich atmosphere. Iron and steel surfaces are being protected by spraying on metal powder with a suitable pistol. Zinc and aluminium are used thus for protection against corrosion.
Modern mass-production methods imply the ability to produce any desired number of interchangeable parts, and this necessitates close accuracy and a means for evaluating with precision either smoothness or the most microscopic deviation from theoretically perfect finish. An instrument designed to fill this requirement is now on the market. It " feels " for surface variations in millionths of an inch and records them automatically on a chart. In operation, a diamond-tipped stylus rests on the surface to be tested, and moves backwards and forwards over it. Its infinitesimal movements are magnified as much as 100,000 times when transmitted on to the chart, showing up any defects plainly. The speed of the graph paper can be adjusted as required to indicate the pitch and depth of any surface irreplarities. Some of the newer types of bearing include the cadmium-base type, i.e., cadmium-silver-copper and cadmiumnickel, made from powdered metals and the comparatively new aluminium-base alloys, a popular composition being one containing several per cent, of tin. The corrosion resistance of bearings is being increased by a plating with indium, in which the indium is diffused into the surface bearing metal.
Nickel-alloy cast irons are being used extensively in compression ignition engines. The composition of the iron used is 3.1 to 3.3 per cent. total carbon, 1.4 to 2.1 per cent. silicon. 1.0 per cent. nickel, 0.15 to 0.4 per cent. chromium, 0.1 to 0.4 per cent. molybdenum. The irons are used primarily for cylinder liners, heads and blocks, and the composition is varied within the 'limits given • to suit the particular purpose. L.S.