PURIFIED OIL FOR ENGINES
Page 38
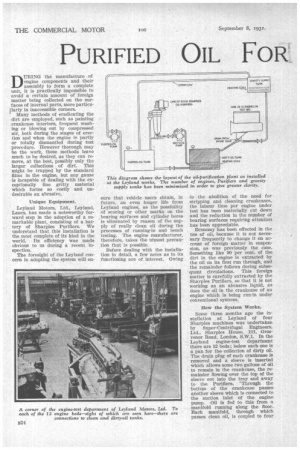
Page 39
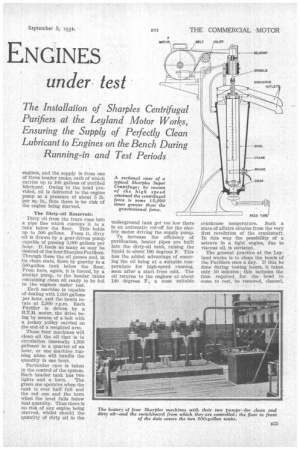
Page 40
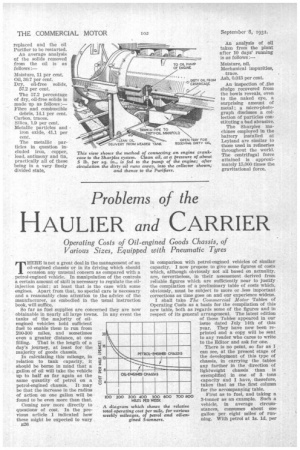
If you've noticed an error in this article please click here to report it so we can fix it.
under lest
DURING the manufacture of engine components and their assembly to form a complete unit, it is practically impossible to avoid a certain amount of foreign matter being collected on the surfaces of internal parts, more particularly in inaccessible corners.
' Many methods of eradicating the dirt are employed, such as painting crankcase interiors, frequent washing or blowing out by compressed air, both during the stages of erection and when the engine is partly or totally dismantled during test procedure. However thorough may be the work, these methods leave much to be desired, as they can remove, at the best, possibly only the larger collections of dirt. This might be trapped by the standard filter in the engine, but any gauze is incapable of dealing with the exceptionally fine gritty material which forms so costly and undesirable an abrasive.
Unique Equipment.
Leyland Motors, Ltd., Leyland, Lanes, has made a noteworthy forward step in the adoption of a remarkable plant, consisting of a battery of Sharpies Purifiers. We understand that this installation is the most complete of its kind in the world. Its efficiency was made obvious to us during a recent inspection.
The foresight of the Leyland concern in adopting the system will en
sure that vehicle users obtain, in future, an even longer life from Leyland engines, as the possibility of scoring or other marks on the bearing surfaces and cylinder bores is eliminated by reason of the supply of really clean oil during the processes of running-in and bench testing. The engine manufacturer, therefore, takes the utmost precaution that is possible.
Before dealing with the installation in detail, a few notes as to its functioning are of interest. Owing to the abolition of the need for stripping and cleaning crankcases, the labour time per engine under test has been materially cut down and the reduction in the number of bearing surfaces requiring attention has been appreciable.
Economy has been effected in the use of oil, because it is not necessary frequently to change it on account of foreign matter in suspension. as was previously the case. Something like 90 per cent. of the dirt in the engine is extracted by the oil on its first run through, and the remainder follows during subsequent circulations. This foreign matter is carefully extracted by the Sharpies Purifiers, so that it is not working as an abrasive liquid, as does the oil in the crankcase of an engine which is being run-in under conventional systems.
How the System Works.
Some three months ago the installation at Leyland of four Sharpies machines was undertaken by Super-Centrifugal Engineers, Ltd.. Sharpies House, 101, Grosvenor Road, London, S.W.1. in the Leyland engine-test department there are 12 beds ; below each one is a pan for the collection of dirty oil. The drain plug of each crankcase is removed and a sleeve is inserted which allows some two gallons of oil to remain in the crankcase, the remainder flowing over the top of the sleeve out into the tray and away to the Purifiers. 'Through the bottom of the crankcase passes another sleeve which is connected to the suction inlet of the engine pump. Oil is fed to this from a manifold running along the floor. Each manifold, through which passes clean oil, is coupled to four engines, and the supply is from one of three header tanks, each of which carries up to 100 gallons of purified lubricant. Owing to the head provided, oil is delivered to the engine pump at a pressure of about 5 lb. per sq. in., thus there is no risk of the engine being starved.
The Dirty-oil Reservoir.
Dirty oil from the trays runs into a pipe line which conveys it to a tank below the floor. This holds up to 500 gallons. From it, dirty oil is drawn by a gear-driven pump capable of passing 5,000 gallons per hour. It feeds as many as may be :desired of the four Sharpies Purifiers. Through these the oil passes and, in its clean state, ilows by gravity to a 500-gallon tank below the floor. From here, again, it is forced, by a similar pump, to the header tanks containing clean oil ready to be fed to the engines under test.
Each machine is capable of dealing with 1,000 gallons per hour, and the bowls rotate at 2,500 r.p.m. Each Purifier is driven by a B.T.H. motor, the drive being by means of a hell with a jockey pulley carried on the end of a weighted arm.
These four machines will clean all the oil that is in circulation (normally 1,300 gallons) in a quarter of an hour, or one machine running alone will handle the quantity in one hour.
Particular care is taken in the control of the system. Each header tank has two lights and a horn. The green one operates when the tank is over half full and the red one and the horn when the level falls below that quantity. Thus there is no risk of any engine being starved, whilst should the quantity of dirty oil in the underground tank get too low there is an automatic cut-off for the electric motor driving the supply pump.
To increase the efficiency of purification, heater pipes are built into the dirty-oil tank, raising the liquid to about 180 degrees F. This has the added advantage of ensuring the oil being at a suitable temperature for high-speed running, soon after a start from cold. The oil returns to the engines at about 140 degrees F.; a most suitable crankcase temperature. Such a state of affairs obtains from the very first revolution of the crankshaft. In this way the possibility of a seizure in a tight engine, due to viscous oil, is obviated.
The general practice at the Leyland works is to clean the bowls of the Purifiers once a day. If this be done during testing hours, it takes only 10 minutes ; this includes the time required for the bowl to come to rest, be removed, cleaned,
replaced and the oil Purifier to be restarted.
An average analysis of the solids removed from the oil is as follows:— Moisture, 11 per cent. Oil, 30.7 per cent.
Dry, oil-free solids, 57.2 per cent.
The 57.2 percentage of dry, oil-free solids is made up as follows :Fibre and combustible debris, 14.1 per cent. Carbon, traces.
Silica, 1.9 per cent. Metallic particles and iron oxide, 41.1 per cent.
The metallic particles in question included iron, copper, lead, antimony and tin, practically all of these being in a very finely divided state.
This view shows the method of connecting an engine crankcase to the Sharpies system. Clean oil, at a pressure of about 5 lb. per sq. in., is fed to the pump of the engine; after circulation the dirty oil runs away, into the collector shown;
An analysis of oil taken from the plant after 10 days' running is as follows:— Moisture, nil, Mechanical impurities, trace.
Ash, 0.013 per cent.
An inspection of the sludge recovered from the bowls reveals, even to the naked eye, a surprising amount of metal ; a micro-photograph discloses a collection of particles constituting a bad abrasive.
The Sharpies machines employed in the battery installed at Leyland are similar to those used in refineries throughout the world. The centrifugal force attained is approximately 15,000 times the gravitational force.