The best braking for artics
Page 68
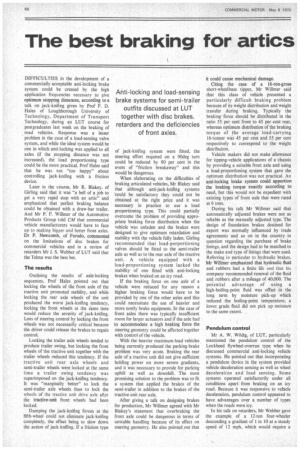
Page 69
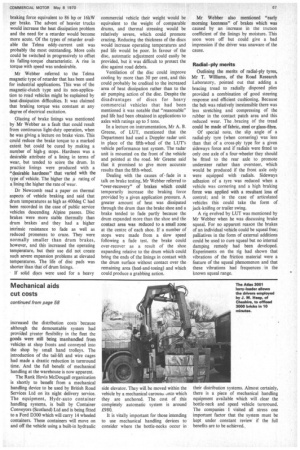
If you've noticed an error in this article please click here to report it so we can fix it.
Anti-locking and load-sensing • brake systems for semi-trailer outfits discussed at LUT together with disc brakes, retarders and the deficiencies of front axles.
DIFFICULTIES, in the development of a commercially acceptable anti-locking brake system could be created by the high application frequencies necessary to give optimum stopping distances, according to a talk on jack-knifing given by Prof F. D. Hales of Loughborough University of Technology, Department of Transport 'Technology, during an LUT course for postgraduates last week on the braking of road vehicles. Response was a lesser problem in the case of a load-sensing valve system, and while the ideal system would be one in which anti-locking was applied to all axles (if the stopping distance was not increased), the load proportioning type could be the more practical. Prof Hales said that he was not "too happy" about controlling jack-knifing with a friction device.
Later in the course, Mr R. Blakey, of Girling said that it was "a hell of a job to get a very rapid stop with an artic" and emphasized that perfect braking balance could be obtained with a draw-bar trailer. And Mr P. F. Willmer of the Automotive Products Group told CM that commercial vehicle manufacturers would have to face up to making bigger and better front axles. Dr P. Newcomb, , of Ferodo, commented on the limitations of disc brakes for commercial vehicles and in a review of retarders Mr J. S. Webber of LUT said that the Telma was the best bet.
The results Outlining the results of axle-locking sequences, Prof Hales pointed out that locking the wheels of the front axle of the tractive unit promoted stability, and while locking the rear axle wheels of the unit produced the worst jack-knifing tendency, locking the front wheels at the same time would reduce the severity of jack-knifing. Loss of steering control by locking the front wheels was not necessarily critical because the driver could release the brakes to regain control.
Locking the trailer axle wheels tended to
• produce trailer swing, but locking the front wheels of the tractive unit together with the trailer wheels reduced this tendency. If the tractive unit rear axle wheels and semi-trailer wheels were locked at the same time a trailer swing tendency was superimposed on the jack-knifing tendency. It was "marginally better" to lock the semi-trailer axle wheels than to lock the wheels of the tractive unit drive axle after the tractive-unit front wheels had been
locked. • Damping the jack-knifing forces at the fifth-wheel could not eliminate jack-knifing completely, the effect being to slow down the action of jack-knifing. If a friction type of jack-knifing system were fitted, the steering effort required on a 90deg turn could be reduced by 80 per cent in the event of "friction breakaway" and this would be dangerous.
When elaborating on the difficulties of braking articulated vehicles, Mr Blakey said that although anti-jack-knifing systems
'could be satisfactory they could not be obtained at the right price and it was
necessary in practice to use a load proportioning type_ This could partially overcome the problem of providing appro priate braking force distribution when the vehicle was unladen and the brakes were designed to give optimum retardation and stability with the vehicle fully laden. Girling recommended that load-porportioning valves should be fitted to the semi-trailer axle as well as to the rear axle of the tractive unit. A vehicle equipped with a load-proportioning system lacked the stability of one fitted with anti-locking brakes when braked on an icy road.
If the braking force on one axle of a vehicle were reduced for any reason a higher braking force would have to be provided by one of the other axles and this could necessitate the use of heavier and more costly brake equipment. In the case of front axles there was typically insufficient room for larger actuators and if the axle had to accommodate a high braking force the steering geometry could be affected together with Control of the vehicle.
With the heavier maximum-load vehicles being currently produced the parking-brake problem was very acute. Braking the rear axle of a tractive unit did not give sufficient holding power on more severe gradients, and it was necessary to provide for parking uphill as well as downhill. The most promising solution to the problem was to fit a system that applied the brakes of the semi-trailer in addition to the brakes of the tractive unit rear axle.
After giving a talk on designing brakes for production, Mr Willmer agreed with Mr Blakey's statement that overbraking the front axle could be dangerous in terms of unstable handling because of its effect on steering geometry. He also pointed out that it could cause mechanical damage.
Citing the case of a 16-ton-gross short-wheelbase tipper, Mr Willmer said that this class of vehicle presented a particularly difficult braking problem because of its weight distribution and weight transfer during braking. Typically the braking force should be distributed in the ratio 55 per cent front to 45 per .cent rear, whereas optimum distribution of the braking torque of the average load-carrying 16-tonner was 45 per cent and 55 per cent respectively to correspond to the weight distribution.
Vehicle makers did not make allowance for tipping-vehicle applications of a chassis by providing a suitable front axle and using a load-proportioning system that gave the optimum distribution was not practical. An anti-locking brake system could apportion the braking torque 'exactly according to need, but this would not be expedient with existing types of front axle that were rated at 6 tons.
During his talk Mr Willmer said that automatically adjusted brakes were not as reliable as the manually adjusted type. The design of foundation brakes destined for export was normally influenced by trade agreements and so on in the country in question regarding the purchase of brake linings, and the design had to be matched to the make and type of linings that were used. Referring in particular to hydraulic brakes, Mr Willmer emphasized that hydraulic fluid and rubbers had a finite life and that his company recommended renewal of the fluid and rubbers after a mileage of 40,000. The potential advantage of using a high-boiling-point fluid was offset in the tong term by moisture pick-up which reduced the boiling-point temperature; a lower, grade fluid did not pick up moisture to the same extent.
Pendulum control Mr A. W. Wildig, of LUT, particularly mentioned the pendulum control of the Lockheed flywheel-overrun type when he discussed commercial anti-locking vehicle systems. He pointed out that incorporating a pendulum device in the system provided vehicle deceleration sensing as well as wheel deceleration and load sensing. Some systems operated satisfactorily under all conditions apart from braking on an icy road. Because it was responsive to vehicle deceleration, pendulum control appeared to have advantages over a number of types when the roads were icy.
In his talk on retarders, Mr Webber gave the example of a 12-ton four-wheeler descending a gradient of 1 in 10 at a steady speed of 12 mph, which would require a braking force equivalent to 86 hp or 16kW per brake. The advent of heavier trucks would increase the heat dissipation problem and the need for a retarder would become more acute. Of the types of retarder available the Telma eddy-current unit was probably the most outstanding. More coils could be switched in progressively to offset its falling-torque characteristic. A rise in torque with speed was undesirable_
Mr Webber referred to the Telma magnetic type of retarder that has been used for industrial applications. This was of the magnetic-clutch type and its non-application to road vehicles might be explained by heat-dissipation difficulties. It was claimed that braking torque was constant at any degree of electrical excitation.
Glazing of brake linings was mentioned by Mr Webber as a fault that could result from continuous light-duty operation, when he was giving a lecture on brake vices. This could reduce the brake torque to a marked extent but could be cured by making a number of high-g stops. Hardness was a desirable attribute of a lining in terms of wear, but tended to score the drum. In practice linings were produced with a "desirable hardness" that varied with the type of vehicle. The higher the At rating of a lining the higher the rate of wear.
Dr Newcomb read a paper on thermal aspects of vehicle braking and said that drum temperatures as high as 400deg C had been recorded in the case of public service vehicles descending Alpine passes. Disc brakes were more stable thermally than drum brakes and they had a higher intrinsic resistance to fade as well as reduced proneness to craze_ They were normally smaller than drum brakes, however, and this increased the operating temperature, but their use did not create such severe expansion problems at elevated temperatures. The life of disc pads was shorter than that'of drum linings.
If solid discs were used for a heavy
commercial vehicle their weight would be equivalent to the weight of comparable drums, and thermal stressing would be relatively severe, which could promote crazing. Reducing the thickness of the discs would increase operating temperatures and pad life would be poor. In favour of the disc, automatic adjustment could easily be provided, but it was difficult to protect the disc against road debris.
Ventilation of the disc could improve cooling by more than 30 per cent, and this could probably be credited to the increased area of heat dissipation rather than to the air pumping action of the disc. Despite the disadvantages of discs for heavy commercial vehicles that had been mentioned it was notable that "reasonable" pad life had been obtained in applications to axles with ratings up to 5 tons.
In a lecture on instrumentation, Mr A. B. Greene, of LUT, mentioned that the Department had used a Doppler radar unit in place of the fifth-wheel of the LUT's vehicle performance test system. The radar unit is mounted on the front of the vehicle and pointed at the road. Mr Greene said that it promised to give more accurate results than the fifth-wheel.
Dealing with the causes of. fade in a talk on brake testing, Mr Webber referred to "over-recovery" of brakes which could temporarily increase the braking force provided by a given application pressure. A greater amount of heat was dissipated through the drum than the brake shoe and a brake tended to fade partly because the drum expanded more than the shoe and the contact area was reduced to a small zone at the centre of each shoe. If a number of stops were made from a slow speed following a fade test, the brake could over-recover as a result of the shoe expanding relative to the drum which could bring the ends of the linings in contact with the drum surface without contact over the remaining area (heel-and-toeing) and which could produce a grabbing action. Mr Webber also mentioned "early morning keenness" of brakes which was caused by an increase in the triction coefficient of the linings by moisture. This soon wore off but could give a bad impression if the driver was unaware of the cause.
Radial-ply merits Outlining the merits of radial-ply tyres, Mr T. Williams, of the Road Research Laboratory, pointed out that adding a bracing tread to radially disposed plies provided a combination of good steering response and efficient cushioning. Because the belt was relatively inextensible there was less stretching and compressing of the rubber in the contact patch area and this reduced wear. The bracing of the tread could be made of fabric, steel or glass-fibre.
Of special note, the slip angle of a radial-ply tyre (when cornering) was less than that of a cross-ply type for a given sideways force and if radials were fitted to only one axle of a four-wheeler they should be fitted to the rear axle to promote understeer rather than oversteer, which would be produced if the front axle only were equipped with radials. Sideways adhesion of a tyre was reduced when a vehicle was cornering and a high braking force was applied with a resultant loss of control; and in the case of articulated vehicles this could take the form of jack-knifing or trailer swing.
A rig evolved by LUT was mentioned by Mr Webber when he was discussing brake squeal. For no apparent reason the brakes of an individual vehicle could be squeal free; palliatives in the form of external additions could be used to cure squeal but no internal damping remedy had been developed. Experiments on the rig had shown that vibrations of the friction material were a feature of the squeal phenomenon and that these vibrations had frequences in the known squeal range.