Towards Constant Horsepower?
Page 58
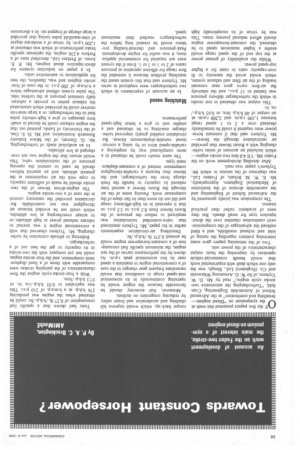
Page 59
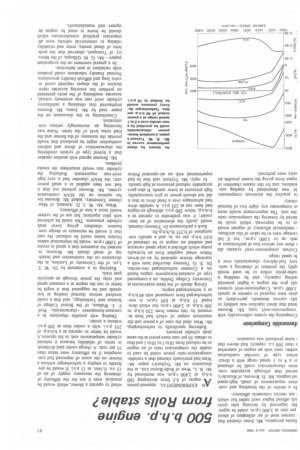
If you've noticed an error in this article please click here to report it so we can fix it.
By P. A. C. Brockington, AMIMechE OF the five papers presented this week at the symposium on "Diesel engines— breathing and combustion" at the Advanced School of Automobile Engineering, C ranfield, "Turbocharging the automotive twostroke cycle engine," read by Mr. D. W. Tryhorn, of Sir W. G. Armstrong Whitworth and Co. (Engineers) Ltd., Slough, was the only one which dealt with experimental work that would benefit commercial-vehicle operators by improving the basic output characteristics of the power unit.
Two of the remaining papers gave some interesting pointers regarding the tuning of inlet and exhaust manifolds, and a third outlined the advantages of the compressionswirl combustion chamber over the directinjection type for small diesels. But they were of academic rather than practical interest.
The symposium was jointly sponsored by the Advanced School of Engineering and the automobile division of the Institution of Mechanical Engineers. Appropriately, Mr. E. W. M. Britain, of Fodens Ltd., was chairman of the session in which Mr. Tryhom's paper was read.
After detailing development work on the Foden Mk. VII 4.8-litre two-stroke engine— which included an account of series turbocharging with a Roots blower that provided air recirculation through the blower— Mr. Tryhorn said that if constant horsepower were required it could be immediately obtained over a 2 to 1 speed range between 1,100 r.p.m. and 2,200 r.p.m. at an output of 40 b.h.p. litre, or 0.65 b.h.p. / cu. in.
This output was obtained in test results in which the turbocharger delivery pressure was limited to 15 p.s.i., and the relatively flat air-flow curve gave near constant loading of the air filter and exhaust system, which would avoid the necessity to fit over-capacity units to cater for a higher top-speed power.
Whilst the availability of greater power at the top end of the speed range would enable a higher maximum speed to be obtained, the constant-horsepower engine should afford reduced journey times. This was by virtue of its exceptionally high torque back-up, which would improve hill climbing and acceleration and foster safety by reducing congestion on inclines.
Moreover, fuel economy should be favourable because the engine would be operating continuously in its economical mid-speed range in conditions that would necessitate frequent gear changes in the case of a conventional engine to maintain a speed near its less economical peak r.p.m. As shown by the performance curves of the test engine, the minimum specific fuel consumption of a constant-horsepower engine would be around 0.375 lb. /b.h.p. /hr.
Describing air-circulation experiments earlier in his paper, Mr. Tryhorn mentioned that valve-controlled recirculation was employed to reduce the pressure of the Roots blower from 8.2 p.s.i. to 3.5 p.s.i. so that it operated in its high-efficiency range and did not do more than its fair share of the compresser work. Passing some of the air through the Roots blower a second time reduced its capacity to handle the fresh charge from the turbocharger, and the blower thus became a variable-throughput compressor instead of a constant-displacement type.
The same results could be obtained in a more complicated way by employing a variable-speed drive or by using a conventional variable-displacement blower. Recirculation enabled greatly improved turbocharger matching to be obtained and a smaller unit to give a better high-speed performance.
Matching eased In an account of experiments in which two turbochargers were employed in series Mr. Tryhorn said that this system eased the matching problem because it extended the flow range for efficient operation at pressure ratios of 2 to 1 to 3 to 1. Even if the system were not required for commercial applications, it was useful for engine development. Peak pressure and thermal-loading problems would be created long before the turbochargers reached their maximum speed. Tests had shown that a specific fuel consumption of 0.37 lb. /b.h.p. /hr. could be obtained when the engine was producing 276 b.h.p. at a b.m.e.p. of 210 p.s.i. This was equivalent to 0.95 b.h.p. /cu. in. or 57.5 b.h.p. /litre.
With a four-stroke-cycle engine the flow characteristics of the pumping strokes were comparable with those of a fixed displacement compressor, and the four-stroke engine could not yet compare with the two-stroke in its • capacity to get the best out of a turbocharger.
Referring to altitude correction by turbocharging, Mr. Tryhorn observed that with a conventional engine it was normal to tolerate reduced power at high altitudes or to accept overcharging at low altittides, which could not be avoided because air throughput was not controllable. Recirculation provided the necessary control in the case of a two-stroke engine.
The engine-driven blower of the twostroke should be made of sufficient capacity to cope with the air requirement at the greatest altitude, and an aneroid bellows should be used to control the opening pressure of the recirculation valve. This would ensure that the engine was not overcharged at low altitudes.
In an analytical study of turbocharging, Mr. G. Garratt, of the Motor Industry Research Association, and Mr. D. E. Gee, of the University of Leeds, pointed out that the engine exhaust could be ducted in smallbore passages to give a high-velocity pulse feed to the turbocharger, or a large reservoir receiver could be provided which attentuated the exhaust pulses to provide a substantially constant pressure at the turbine inlet. The pulse system offered advantages below a b.m.e.p. of 200 p.s.i. in the case of fourstroke engines and was, therefore, the best for applications to automotive units.
In a paper on induction systems for direct-injection diesel engines, Mr. P. E. Jones, of Perkins Ltd., described tests of a Perkins 4.236 engine, the optimum specific brake performance of which was obtained at 1,200 r.p.m. by virtue of a moderate degree of inlet-manifold pulse tuning that provided a large charge of trapped air. In a discussion future prospects, Mr. Jones claimed that current level of air utilization of about per cent at 2.800 r.p.m. could be apprebly improved by devising inlet ports ich offered higher swirl ratios but which not restrict volumetric efficiency.
In a review of the breathing and cornstion requirements of small, high-speed • sel engines, Mr. D. Broome, of Ricardo's, served that although acceptable cornstion characteristics could be obtained t.r a 4 to 1 speed range with a directection type of toroidal combustion amber, tests with an engine of somewhat s than 50Q c.c. capacity had shown that ; noise produced was excessive.
'favourable Comparison
Comparing the system unfavourably with compression-swirl type, Mr. Broome imed that direct injection was unlikely to isfy current demands, particularly as ;ines were required to operate at speeds 5,000 r.p.m. Compression-swirl systems uld give the engine a higher potential ;athing capacity, and by enabling a iable-pintle orifice to be used would iplify the problem of obtaining a satistoey fuel-delivery characteristic over a le speed range.
Current compression-swirl systems did t show any serious loss of performance at xds up to 5,000 r.p.m., but if full vantage were to be taken of this attribute, mechanical efficiency of engines would ve to be improved, which could be tieved by lowering the compression ratio the unit. The improvement would more m compensate any slight loss of thermal ciency.
In practice the minimum compression io was determined by starting conerations, and for this reason chambers of ripact form giving the lowest possible air ocity were preferred.