Getting the National accepted
Page 40
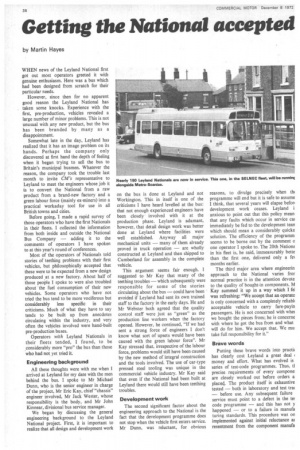
Page 41
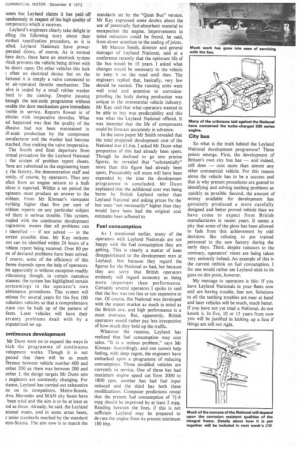
If you've noticed an error in this article please click here to report it so we can fix it.
by Martin Hayes WHEN news of the Leyland National first got out most operators greeted it with genuine enthusiasm. Here was a bus which had been designed from scratch for their particular needs.
However, since then for no apparent good reason the Leyland National has taken some knocks. Experience with the first, pre-production, vehicles revealed a large number of minor problems. This is not unusual with any new product, but the bus has been branded by many as a disappointment.
Somewhat late in the day, Leyland has realized that it has an image problem on its hands. Perhaps the company only discovered at first hand the depth of feeling when it began trying to sell the bus to Britain's municipal busmen. Whatever the reason, the company took the trouble last month to invite CM'S representative to Leyland to meet the engineers whose job it is to convert the National from a raw product from a brand-new factory and a green labour force (mainly ex-miners) into a practical workaday tool for use in all British towns and cities.
Before going, 1 made a rapid survey of those operators who have the first Nationals in their fleets. I collected the information from both inside and outside the National Bus Company — adding it to the comments of operators I have spoken to at this year's round of conferences.
Most of the operators of Nationals told stories of teething problems with their first vehicles, but philosophically accepted that these were to be expected from a new design produced at a new factory. About half of those people I spoke to were also troubled about the fuel consumption of their new vehicles. Some operators who have not tried the bus tend to be more vociferous but considerably less specific in their criticisms. Much of what they have to say tends to be built up from anecdotes circulating within the industry, and very often the vehicles involved were hand-built pre-production buses.
Operators with Leyland Nationals in their fleets tended, I found, to be considerably more "pro" the bus than those who had not yet tried it.
Engineering background All these thoughts were with me when I arrived at Leyland for my date with the men behind the bus. I spoke to Mr Michael Dunn, who is the senior engineer in charge of the project, Mr Eric Kay, chief "chassis" engineer involved, Mr Jack Wester, whose responsibility is the body, and Mr John Kinnear, divisional bus service manager.
We began by discussing the general engineering background to the Leyland National project. First, it is important to realize that all design and development work on the bus is done at Leyland and not Workington. This in itself is one of the criticisms I have heard levelled at the bus: that not enough experienced engineers have been closely involved with it at the production phase. Leyland is adamant, however, that detail design work was better done at Leyland where facilities were well established. Anyway all major mechanical units — many of them already proved in truck operation — are wholly constructed at Leyland and then shipped to Cumberland for assembly in the complete vehicle.
This argument seems fair enough. I suggested to Mr Kay that many of the teething troubles — which subsequently were responsible for some of the stories circulating about the bus — could have been avoided if Leyland had sent its own trained staff to the factory in the early days. He and Mr Webster both agreed that the quality control staff were just as "green" as the production line workers when the factory opened. However, he continued, "If we had sent a strong force of engineers I don't know what sort of upsets would have been caused with the green labour force". Mr Kay stressed that, irrespective of the labour force, problems would still have been caused by the new method of integral construction and the tools involved. The use of car-type pressed steel tooling was unique in the commercial vehicle industry. Mr Kay said that even if the National had been built at Leyland there would still have been teething troubles.
Development work The second significant factor about the engineering approach to the National is the fact that the development programme does not stop when the vehicle first enters service. Mr Dunn, was reluctant, for obvious reasons, to divulge precisely when till programme will end but it is safe to assume I think, that several years will elapse beforl development work ceases. Leyland i anxious to point out that this policy mean that any faults which occur in service cal immediately be fed to the development tean which should mean a considerably quicke solution. The efficiency of the programm seems to be borne out by the comment o one operator I spoke to. The 20th Nations in his fleet is, he said, immeasurably bette than the first one, delivered only a fel months earlier.
The third major area where engineerin approach to the National varies fror normal practice is in the attention devote to the quality of bought-in components. M Kay summed it up in a way which I fei was refreshing: "We accept that an operate is only concerned with a completely reliabl( acceptable vehicle to carry fare-payin passengers. He is not concerned with whei we bought the pieces from; he is concerne with where he got the bus from and what will do for him. We accept that. We mu take full responsibility for it."
Brave words Putting these brave words into practic has clearly cost Leyland a great deal 1 money and effort. What has evolved is series of test-code programmes. Thus, tl precise requirements of every compone are closely worked out before orders a placed. The product itself is exhaustive tested — both in laboratory and test trio — before use. Any subsequent failure service must point to a defect in the te! code programme — and this has not y happened — or to a failure in manufa turing standards. This procedure was on implemented against initial reluctance at resentment from the component manufa Airers but Leyland claims it has paid off iandsomely in respect of the high quality of :omponents which it receives.
Leyland's engineers clearly take delight in cuing the following story about their iroduct specification procedure, as it is !ailed. Leyland Nationals have poweroperated doors, of course. As is normal hese days, these have an interlock system vhich prevents the vehicle being driven with he doors open. On other vehicles this lock ; often an electrical device but on the 4/ational it is simply a valve connected to he air-operated throttle mechanism. The alve is sealed by a small rubber washer lued to the casting. Despite passing hrough the test-code programme without rouble the door mechanism gave immediate euble in service. Reports flowed in of chides with inoperative throttles. What ad happened was that the quality of the dhesive had not been maintained in ill-scale production by the component ianufacturer and the washer had become etached. thus making the valve inoperative. The fourth and final departure from ormal procedure for the Leyland National ; the system of problem report sheets. 'hese are submitted to the engineering team y the factory, the demonstration staff and iostly, of course, by operators. Thus any efect from an engine seizure to a bulb tilure is reported. Within a set period the ngineers must produce an answer to the roblem. From Mr Kinnear's viewpoint nything higher than five per cent of roblem reports on any particular subject nd there is serious trouble. This system, aupled with the continuous development rogramme, means that all problems can ! identified — if not solved — in the tortest possible time, Mr Kay reckons ost can be identified within 24 hours of a .oblem report being received. Over 80 per :tit of declared problems have been solved. f course, some of the efficiency of this theme depends upon the help of operators. his apparently is without exception readily rthcoming though, in certain nameless stances, the system has highlighted certain tortcomings in the operator's own aintenance procedures. This system will ontinue for several years for the first 100 eduction vehicles so that a comprehensive cture can be built up of the pattern of :fects. Later vehicles will have their arranty problems dealt with by a imputerized set-up.
ontinuous development Mr Dunn went on to expand the ways in hich the programme of continuous melopment works. Though it is not pected that there will be as much (Terence between vehicle number 400 and imber 200 as there was between 200 and Luther 1, the design targets Mr Dunn sets s engineers are constantly changing. For stance, Leyland has carried out exhaustive ;ts on its competitors. Metro-Scania, )1vo, Mercedes and MAN city buses have been tried and the aim is to be at least as iod as these. Already, he said, the Leyland ational meets, and in some areas beats, e noise standards reached by the standard etro-Scania. The aim now is to match the standards set by the "Quiet Bus" version. Mr Kay expressed some doubts about the use of potentially fuel-absorbent material to encapsulate the engine. Improvements in noise reduction could be found, he said, from closer attention to the sealing of joints.
Mr Marcus Smith, director and general manager of Leyland National, said at a conference recently that the optimum life of the bus would be 15 years. I asked what changes would be necessary to the vehicle to keep it on the road until then. The engineers replied that, basically, very few should be needed. The running units were well tried and attention to corrosionproofing the body during production was unique in the commercial vehicle industry. Mr Kay said that what operators wanted to be able to buy was predictability and this was what the Leyland National offered. It was intended that the life of components could be forecast accurately in advance.
In the same paper Mr Smith revealed that the total projected development cost of the National was £1.6m. I asked Mr Dunn what proportion of this had already been spent. Though he declined to go into precise figures, he revealed that "substantially" more than this figure had already been spent. Presumably still more will have been expended by the time the development programme is concluded. Mr Dunn explained that the additional cost was being borne by British Leyland rather than Leyland National and asking prices for the bus were "not necessarily" higher than they would have been had the original cost estimates been adhered to.
Fuel consumption As I mentioned earlier, many of the operators with Leyland Nationals are not happy with the fuel consumption they are getting. This is clearly a matter of keen disappointment to the development men at Leyland. Not because they regard the figures for the National as bad, but because they are sorry that British operators evidently still regard economy as being more important than performance. Certainly several operators I spoke to said that the bus was too fast or too expensive to run. Of course, the National was developed with the export market as much in mind as the British one, and high performance is a must overseas. But, apparently, British operators would rather pay less irrespective of how much they hold up the traffic.
Whatever the reasons, Leyland has realized that fuel consumption may cost sales. "It is a serious problem," says Mr Kinnear. Accordingly, and one cannot help feeling, with deep regret, the engineers have embarked upon a programme of reducing consumption. Three modified vehicles are currently in service. One of these has had maximum engine speed cut from 2000 to 1800 rpm, another has had fuel input reduced and the third has both these modifications. Computer predictions reveal that the present fuel consumption of 7mpg should be improved by at least 2 mpg. Reading between the lines, if this is not sufficient Leyland may be prepared to de-rate the engine from its present minimum 180 bhp. City bus So what is the truth behind the Leyland National development programme? Three points emerge. First, the development of Britain's own city bus has — and indeed, still does — cost more than almost any other commercial vehicle. For this reason alone the vehicle has to be a success and that is why present procedures are geared to identifying and solving teething problems as quickly as possible. Second, the amount of money available for development has genuinely produced a more carefully designed and better proved vehicle than we have come to expect from British manufacturers in recent years. It seems a pity that some of the gloss has been allowed to fade from this achievement by odd decisions like refusing to put trained personnel in the new factory during the early days. Third, despite rumours to the contrary, operators' views are being taken very seriously indeed.. An example of this is the current rethink on fuel consumption. I for one would rather see Leyland stick to its guns on this point, however, My message to operators is this: If you have Leyland Nationals in your fleets now and are having trouble, fear not. Solutions to all the teething troubles are near at hand and later vehicles will be much, much better. If you have not yet tried a National, do not knock it. In rive, 10 or 15 years from now you will be justified in kicking up a fuss if things are still not right.