The
Page 54
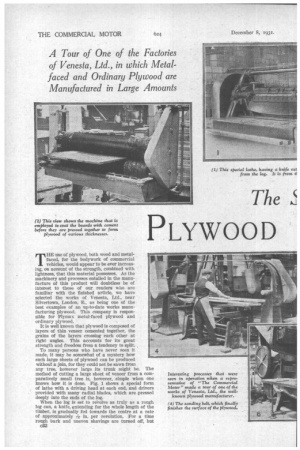
Page 55
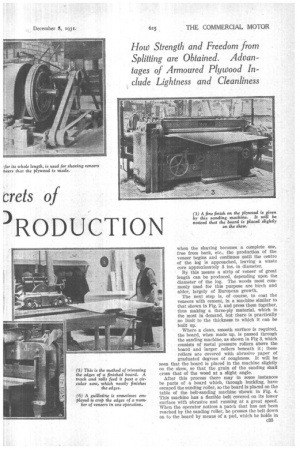
Page 56
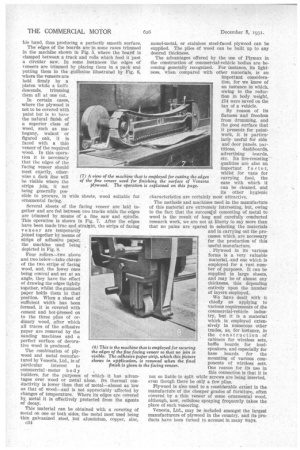
If you've noticed an error in this article please click here to report it so we can fix it.
crets of
PLYWOOD
3RODUCTION
A Tour of One of the Factories of Venesta, Ltd., in which Metalfaced and Ordinary Plywood are Manufactured in Large Amounts How Strength and Freedom from Splitting are Obtained. Advan tages of Armoured Plywood In clude Lightness and Cleanliness
THE use of plywood, both wood and metalfaced, for the bodywork of commercial vehicles, would appear to be ever increasing, on account of the strength, combined with lightness, that this material possesses. As the machinery and processes entailed in the manufacture of this product will doubtless be of interest to those of our readers who are familiar with the finished article, we have selected the works of Venesta, Ltd., near Silvertown, London. E., as being one of the best examples of an up-to-date works manufacturing plywood. This company is responsible for Plymax metal-faced plywood and ordinary plywood.
It is well known that plywood is composed of layers of thin veneer cemented together, the grains of the layers crossing each other at right angles. This accounts for its great strength and freedom from a tendency to split.
To many persons who have never seen it made, it may be somewhat of a mystery how such large sheets of plywood can be produced without a join, for they could not be sawn from any tree, however large its trunk might be. The method of cutting a large sheet of veneer from a comparatively small tree is, however, simple when one knows how it is done. Fig. 1 shows a special form of lathe with a driving head at each end, and drivers provided with many radial blades, which are pressed deeply into the ends of the log.
When the log is set to revolve as truly as a rough log can, a knife, extending for the whole length of the timber, is gradually fed towards the centre at a rate of approximately A in. per revolution. For a time rough bark and uneven shavings are turned off, but 0.32 when the shaving becomes a complete one, free from bark, etc., the production of the veneer begins and continues until the centre of the log is approached, leaving a waste core approximately 3 ins. in diameter. By this means a strip of veneer of great length can be produced, depending upon the diameter of the log. The woods most commonly used for this purpose are birch and alder, largely of European growth. The next step is, of course, to coat the veneers with cement, in a machine similar to that shown in Fig. 2, and press them together, thus making a three-ply material, which is the most in demand, but there is practically no limit to the thickness to which it can be built up. Where a clean, smooth surface is required, the board, when made up, is passed through the sanding machine, as shown in Fig 3, which consists of metal pressure rollers above the board and larger rollers beneath it ; these rollers are covered with abrasive paper of graduated degrees of roughness. It will be seen that the board is placed in the machine slightly on the skew, so that the grain of the sanding shall cross that of the wood at a slight angle. After this process there may in some instances
be parts of a board which, through buckling, have escaped the sanding roller, so the board is placed on the table of the belt-sanding machine -shown in Fig. 4. This machine has a flexible belt covered on its lower surface with abrasive and running at a great speed. When the operator notices a patch that has not been reached by the sanding roller, he presses the belt down on to the board by means of a pad, which he holds in
his hand, thus producing a perfectly smooth surface. The edges of the boards are in some cases trimmed in the machine shown in Fig. 5, where the board is clamped between a track and rolls which feed it past a circular saw. In some instances the edges of eneers are trimmed by placing them in a pack and putting them in the guillotine illustrated by Fig. 6, where the veneers are held firmly by a platen while a knife descends, trimming them all at one cut.
In certain cases, where the plywood is not to be covered with paint but is to have the natural finish of a superior class of wood, such as mahogany, walnut or figured oak, it is faced with a thin veneer of the required wood. In this operation it is necessary that the edges of the facing veneer should meet exactly, otherwise a dark line will be visible where the strips join, it not being generally possible to procure, in wide ornamental facing.
Several sheets of the facing veneer are laid together and are fed between two tracks while the edges are trimmed by means of a fine saw and spindle. This operation is shown in Fig. 7. After the edges have been made true and straitht, the strips of facing V eneer are temporarily joined together by means of strips of adhesive paper, the machine used being depicted in Fig. 8.
Four rollers—two above and two below—take charge of the two strips of facing wood, and, the lower ones being conical and set at an angle, they have the effect of drawing the edges tightly together, whilst the gummed paper holds them in that position. When a sheet of sufficient width has been formed, it is covered with cement and hot-pressed on to the three plies of ordinary wood, after which all traces of the adhesive paper are removed by the sanding machines and a perfect surface of decorative wood is produced.
The combination of plywood and metal manufactured by Venesta, Ltd., is of particular interest to commercial motor b od y builders, for the purposes of which it has advantages over wood or metal alone. Its thermal conductivity is lower than that of metal—almost as low as that• of wood—and is not appreciably affected by changes of tetuperature. Where its edges are covered by metal it is effectively protected from the agents of decay.
This material can be obtained with a covering of metal on one or both sides, the metal most used being thin galvanized steel, but aluminium, copper, zinc, sheets, wood suitable for monel-metal, or stainless steel-faced plywood can be supplied. The plies of wood can be built up to any desired thickness.
The advantages offered by the use of Plyrnax in the construction of commercial-vehicle bodies are becoming generally recognized. For instance, its lightness, when compared with other materials, is an important consideration, for we know of an instance in which, sowing to the reduction in body weight, £14 were saved on the tax of a vehicle.
By reason of its flatness and freedom from drumming, and the good surface that it presents for paintwork, it is particularly useful for side and door panels. partitions, dashboards, advertising boards, etc. Its fire-resisting qualities are also an important factor, whilst for vans for carrying food, the ease with which it can be cleaned, and its other hygienic characteristics are certainly most attractive.
The methods and machines used in the manufacture of this material are extremely interesting, but, owing to the fact that the succesgul cementing of metal to wood is the result of long and carefully conducted research work, we are not at liberty to say more than that no pains are spared in selecting the materials and in carrying out the processes which are necessary for the production of this useful manufacture.
Plywood in its various forms is a very valuable material, and one which is employed for a vast number of purposes. It can be supplied in large sheets, and may be of almost any thickness, this depending entirely upon the number of layers employed.
We have dealt with it chiefly as applying to various requirements of the commercial-vehicle industry, but it is a material which is employed extensively in numerous other trades, as, for instance, in the construction of cabinets for wireless sets, baffle boards for loudspeakers, and especially for base boards for the mounting of various components of wireless sets. One reason for its use in this connection is that it is not so liable to split while screws are being inserted, even though there be only a few plies.
Plywood is also used to a considerable extent in the manufacture of the cheaper grades of furniture, often covered by a thin veneer of some ornamental wood, although, now, cellulose spraying frequently takes the place of such veneering.
Venesta, Ltd., may be included amongst the largest manufacturers of plywood in the country, and its products have been turned to account in many ways.