costing for maximum profit
Page 46
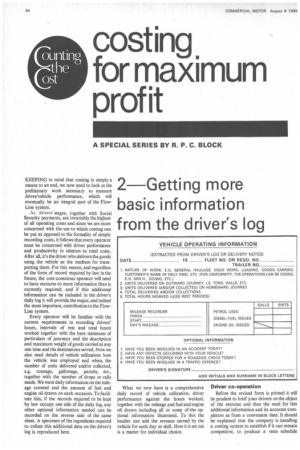
Page 47
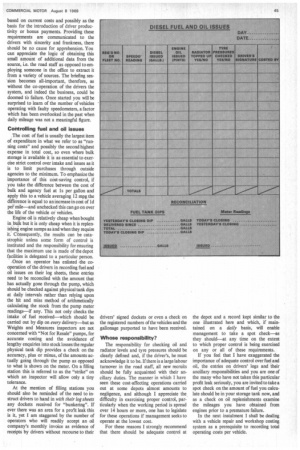
If you've noticed an error in this article please click here to report it so we can fix it.
KEEPING in mind that costing is simply a means to an end, we now need to look at the preliminary work necessary to measure driver/vehicle performance, which will eventually be an integral part of the FlowLine system.
As drivers' wages, together with Social Security payments, are invariably the highest of all operating costs and since we are more conc,erned with the use to which costing can be put as opposed to the formality of simply recording costs, it follows that every operator must be concerned with driver performance and productivity in relation to total costs. After all, it's the driver who delivers the goods using the vehicle as the medium for transporting them For this reason, and regardless of the form of record required by law in the future, the cost-conscious operator will need to have recourse to more information than is currently required; and if this additional information can be included in the driver's daily log it will provide the major, and indeed the most important, contribution to the FlowLine system.
Every operator will be familiar with the current requirements in recording drivers' hours, intervals of rest and total hours worked together with the bare minimum of particulars of journeys and the description and maximum weight of goods carried at any one time and the destinations served. Now we also need details of vehicle utilization: how the vehicle was employed and when, the number of units delivered and/or collected, e.g. tonnage, gallonage, parcels, etc., together With the number of drops or calls made. We want daily information on the mileage covered and the amount of fuel and engine oil drawn on each occasion. To facilitate this, if the records required to be kept by law occupy one side of the daily log, any other optional information needed can be recorded on the reverse side of the same sheet. A specimen of the ingredients required to collate this additional data on the driver's log is reproduced here.
What we now have is a comprehensive daily record of vehicle utilization, driver performance against the hours worked, together with the mileage and fuel and engine oil drawn including all or some of-the optional information illustrated. To this the haulier can add the revenue earned by the vehicle for each day or shift. How it is set out is a matter for individual choice.
Driver co-operation
Before the revised form is printed it will be prudent to brief your drivers on the object of the exercise and thus the need for this additional information and its accurate completion as from a convenient date. It should be explained that the company is installing a costing system to establish if it can remain competitive, to produce a rates schedule based on current costs and possibly as the basis for the introduction of driver productivity or bonus payments. Providing these requirements are communicated to the drivers with sincerity and frankness, there should be no cause for apprehension. You can appreciate the logic of obtaining this small amount of additional data from the source, i.e. the road staff as opposed to employing someone in the office to extract it from a variety of sources. The briefing session becomes all-important, therefore, as without the co-operation of the drivers the system, and indeed the business, could be doomed to failure. Once started you will be surprised to learn of the number of vehicles operating with faulty speedometers, a factor which has been overlooked in the past when daily mileage was not a meaningful figure.
Controlling fuel and oil issues The cost of fuel is usually the largest item of expenditure in what we refer to as "running costs" and possibly the second highest expense in total cost, so even where bulk storage is available it is as essential to exercise strict control over intake and issues as it is to limit purchases through outside agencies to the minimum. To emphasize the importance of this cost-saving control, if you take the difference between the cost of bulk and agency fuel at Is per gallon and apply this to a vehicle averaging 12 mpg the difference is equal to an increase in cost of Id per mile—and unchecked this can go on over the life of the vehicle or vehicles.
Engine oil is relatively cheap when bought in bulk but it is only cheap when it is replenishing engine sumps as and when they require it. Consequently, the results can be catastrophic unless some form of control is instituted and the responsibility for ensuring that the maximum use is made of the depot facilities is delegated to a particular person.
Once an operator has enlisted the cooperation of the drivers in recording fuel and oil issues on their log sheets, these entries need to be reconciled with the amount that has actually gone through the pump, which should be checked against physical tank dips at daily intervals rather than relying upon the hit and miss method of arithmetically calculating the stock from the pump meter readings—if any. This not only checks the intake of fuel received—which should be carried out by dip on every delivery—but as Weights and Measures inspectors are not concerned with "Not for Resale" pumps, for accurate costing and the avoidance of lengthy enquiries into stock losses the regular physical tank dip provides a check on the accuracy, plus or minus, of the amounts actually going through the pump as opposed to what is shown on the meter. On a filling station this is referred to as the "strike" on which an inspector will allow only a tiny tolerance.
At the mention of filling stations you should also be reminded of the need to instruct drivers to hand in with their log sheets any dockets received for "bunkering". If ever there was an area for a proit leak this is it, yet I am staggered by the number of operators who will readily accept an oil company's monthly invoice as evidence of receipts by drivers without recourse to their drivers' signed dockets or even a check on the registered numbers of the vehicles and the gallonage purported to have been received.
Whose responsibility?
The responsibility for checking oil and radiator levels and tyre pressures should be clearly defined and, if the driver's, he must acknowledge it to be. If there is a large labour turnover in the road staff, all new recruits should be fully acquainted with their ancillary duties. The manner in which I have seen these cost-affecting operations carried out at some depots almost amounts to negligence, and although I appreciate the difficulty in exercising proper control, particularly when the working period is spread over 14 hours or more, one has to legislate for these operations if management seeks to operate at the lowest cost.
For these reasons I strongly recommend that there should be adequate control at the depot and a record kept similar to the one illustrated here and which, if maintained on a daily basis, will enable management to take a spot check—as they should—at any time on the extent to which proper control is being exercised on any or all of these requirements.
If you feel that I have exaggerated the importance of adequate control over fuel and oil, the entries on drivers' logs and their ancillary responsibilities and you are one of the many who have not taken this particular profit leak seriously, you are invited to take a spot check on the amount of fuel you calculate should be in your storage tank now, and as a check on oil replenishments examine the mileages you have obtained from engines prior to a premature failure.
In the next instalment I shall be dealing with a vehicle repair and workshop costing system as a prerequisite to recording total operating costs per vehicle.