TRANSFER SYSTEM
Page 50
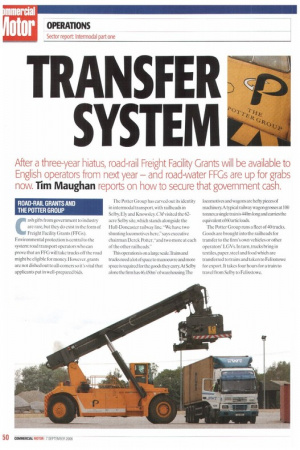
Page 51
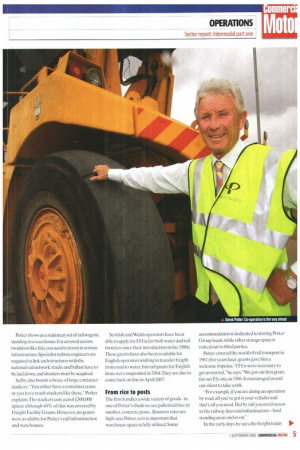
Page 52
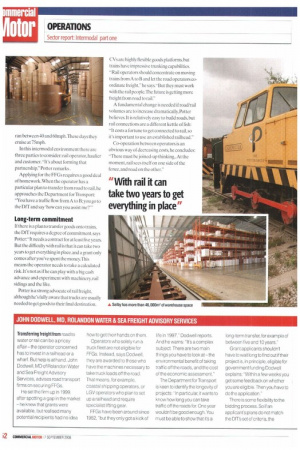
Page 53
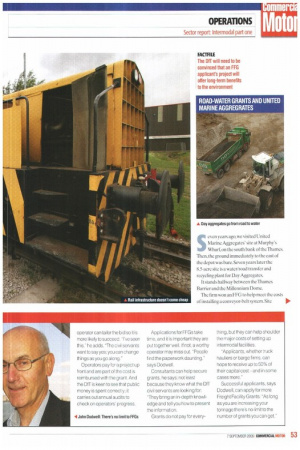
Page 54
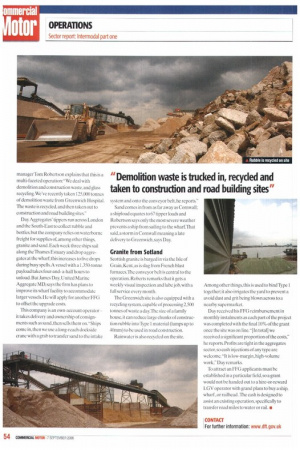
If you've noticed an error in this article please click here to report it so we can fix it.
After a three-year hiatus, road-rail Freight Facility Grants will be available to
English operators from next year — and road-water FFGs are up for grabs now. Tim Maughan reports on how to secure that government cash.
ROAD-RAIL GRANTS AND THE POTTER GROUP Cash gifts from government to industry are rare, but they do exist in the form of Freight Facility Grants (FFGs). Environmental protection is central to the system:road transport operators who can prove that an FFG will take trucks off the road might be eligible for money. However, grants are not dished out to all-comers so it's vital that applicants put in well-prepared bids. The Potter Group has carved out its identity in intermodal transport, with railheads in Selby, Ely and Knowsley. CM visited the 62acre Selby site, which stands alongside the Hull-Doncaster railway line. "We have two shunting locomotives here," says executive chairman Derek Potter, "and two more at each of the other railheads."
This operation is on a large scale.Trains and trucks need a lot of space to manoeuvre and more space is required for the goods they carry.At Selby alone the firm has 46,450m2 of warehousing.The locomotives and wagons are hefty pieces of machinety.A typical railway wagon grosses at 1(X) tonnes; a single train is 44.0m long and carries the equivalent of 60artic loads.
The Potter Group runs a fleet of 40 trucks. Goods are brought into the railheads for transfer to the firm's own vehicles or other operators' LGVs. In turn, trucks bring in textiles, paper, steel and food which are transferred to trains and taken to Felixstowe for export. It takes four hours for a train to travel from Selby to Felixstowe.
Potter shows us a stationary set of rail wagons, standing in a warehouse. For covered accommodation like this, you need to invest in serious infrastructure. Specialist railway engineers are required to link such structures with the national rail network:tracks and ballast have to he laid down, and shunters must be acquired.
Selby also boasts a brace of large container stackers. "You either have a container crane or you have reach stackers like these," Potter explains. The stackers cost a cool £300,000 apiece although 40% of that was covered by Freight Facility Grants. However, no grants were available for Potter's rail infrastructure and warehouses. Scottish and Welsh operators have been able to apply for FFGs for both water and rail transfers since their introduction in the 1980s. These grants have also been available for English operators wishing to transfer freight from road to water,but rail grants for English firms were suspended in 2004.They are due to come back on line in April 2007.
From rice to posts The firm handles a wide variety of goods in one of Potter's sheds we see palletised rice; in another, concrete posts.. Business rates are high, says Potter, so it is important that warehouse space is fully utilised. Some accommodation is dedicated to storing Potter Group loads, while other storage space is rented out to third parties.
Potter entered the world of rail transport in 1981: five years later, grants gave him a welcome impetus."FEGs were necessary to get us started," he says. "We got our first grant, for our Ely site, in 1986. It encouraged us and our client to take a risk.
"For example, if you are doing an operation byroad. all you've got is your vehicles and that's all you need. But by rail you need access to the railway lines and infrastructure — hard standing areas and so on."
In the early days, he says„the freight trains ran between 40 and 60mph.These days they cruise at 75mph.
In this intermodal environment there are three parties to consider: rail operator, haulier and customer."Ies about forming that partnership." Potter remarks .
Applying for the FFGs requires a good deal of homework.When the operator has a particular plan to transfer from road to rail, he approaches the Department for Transport: "You have a traffic flow from A to B; you go to the DfT and say 'how can you assist me?"' Long-term commitment
If there is a plan to transfer goods onto trains, the DfT requires a degree of commitment. says Potter: "It needs a contract for at least five years But the difficulty with rail is that it can take two years to get everything in place, and a grant only comes after you've spent the money.This means the operator needs to take a calculated risk. It's not as if he can play with a big cash advance and experiment with machinery, rail sidings and the like.
Potter is a strong advocate of rail freight, although he's fully aware that trucks are usually needed to get goods to their final destination. CVs are highly flexible goods platforms,but trains have impressive trunking capabilities. "Rail operators should concentrate on moving trains from A to B and let the road operators coordinate freight," he says. "But they must work with the rail people.The future is getting more freight from road to rail."
A fundamental change is needed if road/rail volumes are to increase dramatically, Potter believes. It is relatively easy to build roads,but rail connections are a different kettle of fish: "It costs a fortune to get connected to rail, so it's important to use an established railhead."
Co-operation between operators is an obvious way of decreasing costs, he concludes: "There must be joined-up thinking..At the moment, rail sees itself on one side of the fence, and road on the other." ROAD-WATER GRANTS AND UNITED MARINE AGGREGRATES even years ago, we visited United Marine Aggregates' site at Murphy's 11IV::: Wharf, on the south bank of the Thames. Then, the ground immediately to the east of the depot was bare. Seven years later the 8.5-acre site is a water/road transfer and recycling plant for Day Aggregates.
It stands halfway between the Thames Barrier and the Millennium Dome.
The firm won an HU to help meet the costs of installing a conveyor-belt system. Site managerTom Robertson explains that this is a multi-faceted operation:"We deal with demolition and construction waste. and glass recycling. We've recently taken 125,000 tonnes of demolition waste from Greenwich Hospital. The waste is recycled, and then taken out to construction and road building sites" Day Aggregates' tippers run across London and the South-East to collect rubble and bottles, but the company relies on waterborne freight for supplies of, among other things. granite and sand. Each week three ships sail along the Thames Estuary and drop aggregates at the wharf; this increases to five drops during busy spells A vessel with a 1,350-tonne payload takes four-anda-half hours to unload. But James Day, United Marine Aggregate MD, says the firm has plans to improve its wharf facility to accommodate larger vessels. He will apply for another FFG to offset the upgrade costs This company is an own-account operator — it takes delivery and ownership of consignments such as sand, then sells them on."Ships come in, then we use a long-reach dockside crane with a grab to transfer sand to the intake system and onto the conveyor belt, he reports" Sand comes in from as far away as Cornwall; a shipload equates to 67 tipper loads and Robertson says only the most severe weather prevents a ship from sailing to the wharf. That said, a storm in Cornwall meaning a late delivery to Greenwich,says Day.
Granite from Sotland scot iish grani ic is barged in via the Isle of Grain. Kent, as is slag from French blast fumaces.The conveyor belt is central to the operation. Roberts remarks that it gets a weekly visual inspection and lube job, with a full service every month.
The Greenwich site is also equipped with a recycling system, capable of processing 2,500 tonnes of waste a day.The size of a family house, it can reduce large chunks of construction rubble into Type 1 material (lumps up to 40mm) to be used in road construction.
Rainwater is also recycled on the site. Among other things this is used to bind Type 1 together; it also irrigates the yard to prevent a avoid dust and grit being blown across to a nearby supermarket.
Day received his FFG reimbursement in monthly instalments as each part of the project was completed with the final 10% of the grant once the site was on line. "[In total] we received a significant proportion of the costs," he reports. Profits are tight in the aggregates sector,so cash injections of any type are welcome."It is low-margin, high-volume work," Day remarks.
To attract an FFG applicants must be established in a particular field,so a grant would not be handed out to a hire-or-reward LGV operator with grand plans to buy a ship, wharf ,or railhead The cash is designed to assist an existing operation, specifically to transfer road miles to water or rail. •