A SIMULATOR TO MAKE THE ADRENALIN FLOW
Page 45
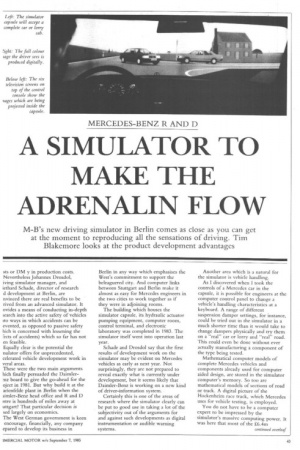
Page 44
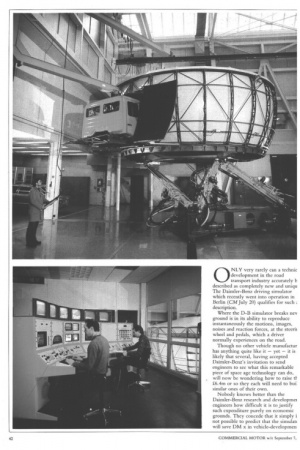
Page 46
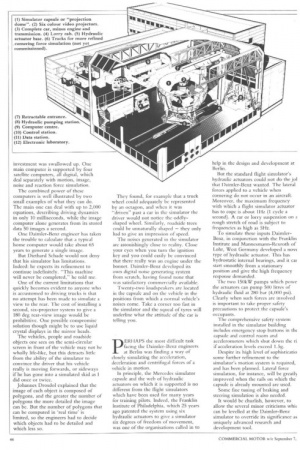
If you've noticed an error in this article please click here to report it so we can fix it.
M-B's new driving simulator in Berlin comes as close as you can get at the moment to reproducing all the sensations of driving. Tim Blakemore looks at the product development advantages
QNLY very rarely can a technic development in the road transport industry accurately h described as completely new and uniqu The Daimler-Benz driving simulator which recently went into operation in Berlin (CM July 20) qualifies for such description.
Where the D-B simulator breaks nev ground is in its ability to reproduce instantaneously the motions, images, noises and reaction forces, at the steed' wheel and pedals, which a driver normally experiences on the road. Though no other vehicle manufactur has anything quite like it — yet — it is likely that several, having accepted Daimler-Benz's invitation to send engineers to see what this remarkable piece of space age technology can do, will now be wondering how to raise t] £6.4m or so they each will need to buii similar ones of their own.
Nobody knows better than the Daimler-Benz research and developmei engineers how difficult it is to justify such expenditure purely on economic grounds. They concede that it simply i not possible to predict that the simulan will save DM x in vehicle-developmen
sts or DM y in production costs. Nevertheless Johannes Drosdol, iving simulator manager, and
iethard Schade, director of research d development at Berlin, are
nvinced there are real benefits to be rived from an advanced simulator. It ovides a means of conducting in-depth iearch into the active safety of vehicles ito ways in which accidents can be evented, as opposed to passive safety hich is concerned with lessening the :-ects of accidents) which so far has not en feasible.
Equally clear is the potential the nulator offers for unprecedented, celerated vehicle development work in veral areas.
These were the two main arguments hich finally persuaded the Daimler:nz board to give the go-ahead for the oject in 1981. But why build it at the arienfelde plant in Berlin when the aimler-Benz head office and R and D ntre is hundreds of miles away at uttgart? That particular decision is sed largely on economics.
The West German government is keen encourage, financially, any company epared to develop its business in Berlin in any way which emphasises the West's commitment to support the beleaguered city. And computer links between Stuttgart and Berlin make it almost as easy for Mercedes engineers in the two cities to work together as if they were in adjoining rooms.
The building which houses the simulator capsule, its hydraulic actuator pumping equipment, computer room, control terminal, and electronic laboratory was completed in 1983. The simulator itself went into operation last year.
Schade and Drosdol say that the first results of development work on the simulator may be evident on Mercedes vehicles as early as next year. Not surprisingly, they are not prepared to reveal exactly what is currently under development, but it seems likely that Daimler-Benz is working on a new kind of driver-information system.
Certainly this is one of the areas of research where the simulator clearly can be put to good use in taking a lot of the subjectivity out of the arguments for and against such developments as digital instrumentation or audible warning systems. Another area which is a natural for the simulator is vehicle handling.
As I discovered when I took the controls of a Mercedes car in the capsule, it is possible for engineers at the computer control panel to change a vehicle's handling characteristics at a keyboard. A range of different suspension damper settings, for instance, could be tried out in the simulator in a much shorter time than it would take to change dampers physically and try them on a "real" car or lorry and "real" road. This could even be done without ever actually manufacturing a component of the type being tested.
Mathematical computer models of complete Mercedes vehicles and components already used for computer aided design, are stored in the simulator computer's memory. So too are mathematical models of sections of road or track. A digital picture of the Hockenheim race track, which Mercedes uses for vehicle testing, is employed. You do not have to be a computer expert to be impressed by the simulator's massive computing power. It was here that most of the £6.4m investment was swallowed up. One main Computer is supported by four satellite computers, all digital, which deal separately with motion, image, noise and reaction force simulation.
The combined power of these computers is well illustrated by two small examples of what they can do. The main one can deal with up to 2,000 equations, describing driving dynamics in only 10 milliseconds, while the image computer alone generates from its stored data 50 images a second.
One Daimler-Benz engineer has taken the trouble to calculate that a typical home computer would take about 65 years to generate a single image.
But Diethard Schade would not deny that his simulator has limitations. Indeed: he expects its refinement to continue indefinitely. "This machine will never be completed," he told me.
One of the current limitations that quickly becomes evident to anyone who is accustomed to driving trucks is that no attempt has been made to simulate a view to the rear. The cost of installing a second, six-projector system to give a 180 deg rear-view image would, be prohibitive. One possible compromise solution though might be to use liquid crystal displays in the mirror heads.
The vehicles, people and roadside objects one sees on the semi-circular screen in front of the vehicle may not be wholly life-like, but this detracts little from the ability of the simulator to convince the driver that his vehicle really is moving forwards, or sideways if he has gone into a simulated skid as did once or twice.
Johannes Drosdol explained that the image of each object is composed of polygons, and the greater the number of polygons the more detailed the image can be. But the number of polygons that can be computed in 'real time' is limited, so the engineers had to decide which objects had to be detailed and which less so. They found, for example that a truck wheel could adequately be represented by an octagon, and when it was "driven" past a car in the simulator the driver would not notice the oddlyshaped wheel. Similarly, roadside trees could be unnaturally shaped — they only had to give an impression of speed.
The noises generated in the simulator are astonishingly close to reality. Close your eyes when you turn the ignition key and you could easily be convinced that there really was an engine under the bonnet. Daimler-Benz developed its own digital noise generating system from scratch, having found none that was satisfactory commercially available.
Twenty-two loudspeakers are located in the capsule and on the vehicle in the positions from which a normal vehicle's noises come. Take a corner too fast in the simulator and the squeal of tyres will underline what the attitude of the car is telling you.
IDERHAPS the most difficult task facing the Daimler-Benz engineers at Berlin was finding a way of closely simulating the acceleration, deceleration and centrifugal forces of a vehicle in motion.
In principle, the Mercedes simulator capsule and the web of hydraulic actuators on which it is supported is no different from the flight simulators which have been used for many years for training pilots. Indeed, the Franklin Institute of Philadelphia, which 25 years ago patented the system using six hydraulic actuators to give a simulator six degrees of freedom of movement, was one of the organisations called in to help in the design and development at Berlin.
But the standard flight simulator's hydraulic actuators could not do the jol that Daimler-Benz wanted. The lateral forces applied to a vehicle when cornering do not occur in an aircraft. Moreover, the maximum frequency with which a flight simulator actuator has to cope is about 1Hz (1 cycle a second). A car or lorry suspension on rough stretch of road is subject to frequencies as high as
To simulate these inputs DaimlerBenz, in conjunction with the Franklin Institute and Mannesmann-Rexroth of Lohr, West Germany developed a novt type of hydraulic actuator. This has hydrostatic internal bearings, and it car start smoothly from a stationary position and give the high frequency response demanded.
The two 150kW pumps which powe the actuators can pump 500 litres of hydraulic fluid at 280 bar (4,000 psi). Clearly when such forces are involved is important to take proper safety precautions to protect the capsule's occupants.
The comprehensive safety system installed in the simulator building includes emergency stop buttons in thc capsule and control room and accelerometers which shut down the ri if acceleration levels exceed 1.5g.
Despite its high level of sophisticatio some further refinement to the simulator's motion system is required, and has been planned. Lateral force simulation, for instance, will be greatly improved when the rails on which the capsule is already mounted are used.
Some fine tuning of braking and steering simulation is also needed.
It would be churlish, however, to allow the several Minor criticisms whit can be levelled at the Daimler-Benz simulator to override its significance as uniquely advanced research and development tool.