BEARINGS and BEARING METALS in the MAKING A NT1MONY, copper, lead
Page 46
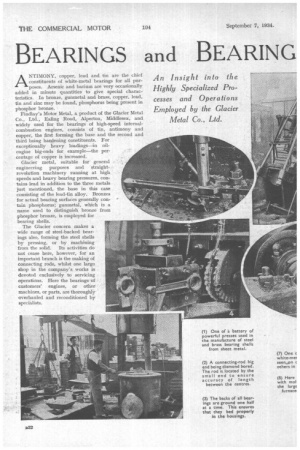
Page 47
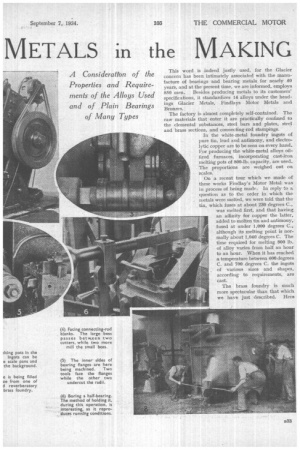
Page 48
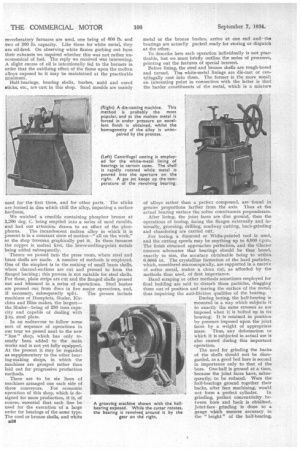
Page 49
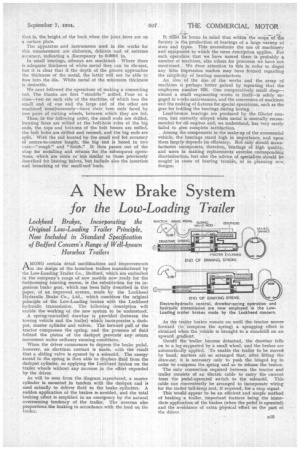
If you've noticed an error in this article please click here to report it so we can fix it.
and tin are the chief constituents of white-metal bearings for all purposes. Arsenic and barium are very occasionally added in minute quantities to give special characteristics. In bronze, gunmetal and brass, copper, lead, tin and zinc may be found, phosphorus being present in phosphor bronze.
Findlay's Motor Metal, a product of the Glacier Metal Co., Ltd., Ealing Road, Alperton, Middlesex, and widely used for the bearings of high-speed internalcombustion engines, consists of tin, antimony and copper, the first forming the base and the second and third being hardening constituents. For exceptionally heavy loadings—in oilengine big-ends for example--the percentage of copper is increased.
Glacier metal, suitable for general engineering purposes and straightrevolution machinery running at high speeds and heavy bearing pressures, contains lead in addition to the three metals just mentioned, the base in this case consisting of the lead-tin alloy. Bronzes for actual bearing surfaces generally contain phosphorus; gunmetal, which is a name used to distinguish bronze from phosphor bronze, is employed for bearing shells.
The Glacier concern makes a wide range of steel-backed bear
ings also, forming the steel shells by pressing, or by machining from the solid. Its activities do not cease here, however, for an important branch is the making of connecting rods, whilst one large shop in the company's works is devoted exclusively to servicing operations. Here the bearings of customers' engines, or other machines, or parts, are thoroughly overhauled and reconditioned by specialists.
This word is indeed justly used, for the Glacier concern has been intimately associated with the manu facture of bearings and bearing metals for nearly 40 years, and at the present time, we are informed, employs 850 men. Besides producing metals to its customers' specifications, it standardizes 14 alloys under the headings Glacier Metals, Findlays Motor Metals and Bronzes.
The factory is almost completely self-contained. The raw materials that enter it are practically confined to the elemental substances, steel bars and. plates, steel and brass sections, and connecting-rod stampings.
In the white-metal foundry ingots of pure tin, lead and antimony, and electro
lytic copper are to be seen on every hand. For producing the white-metal alloys oilfired furnaces, incorporating cast-iron melting pots of 800-lb. capacity, are used.
• The proportions are weighed out on scales.
On a recent tour which we made of these works Findlay's Motor Metal was in process of being made. In reply to a question as to the order in which the utetals were melted, we were told that the tin, which fuses at about 230 degrees C., was melted first, and that having an affinity for copper the latter, added to molten tin and antimony, fused at under 1,000 degrees C., although its melting point is nor mally about 1,040 degrees C. The time required for melting 800 lb.
of alloy varies from half an hour to an hour. When it has reached a. temperature between 600 degrees C. and 700 degrees C. the ingots of various sizes and shapes, according to requirements, are cast.
The brass foundry is much more spectacular than that which we have just described. Here reverberatory furnaces are used, one being of 600 lb. and two of 300 lb. capacity. Like those for white metal, they are oil-fired. On observing white flames gushing out from their exhausts we inquired whether this was not rather uneconomical of fuel. The reply we received was interesting. A slight excess of oil is intentionally fed to the burners in order that the oxidizing effect of the flame upon the molten alloys exposed to it may be maintained at the practicable minimum.
Half-bearings, bearing shells, bushes, solid and cored sticks, etc., are cast in this shop. Sand moulds are mainly
used for' the, first three, and forother parts. The sticks are formed in dies which chill the alloy, imparting a surface hardness.
We watched a crucible containing phosphor bronze at 1,200 deg. C. being emptied into a series of sand moulds, and had our attention drawn to an effect of the phos phorus. The incandescent molten alloy in which it is present is in a constant state of motion----" all on the Work," as the shop foreman graphically put it. In these furnaces the copper is melted first, the lower-melting-point metals being added subsequently.
Thence we passed into the press room, where steel and brass shells are made. A number of methods is employed. One of the simplest is in the making of small brass shells, where channel-sections are cut and pressed to form the flanged backing ; this process is not suitable for steel shells. For these, plain strips are cut and the flanged shells pressed out and trimmed in a_series of operations. Steel bushes are pressed out from discs in five major operations, and,
if necessary, subsequently split. The presses include machines of Humphris, Shuler, Kirchies and Bliss makes, the largest— the ShuIer—being of 250 tons capacity and capable of dealing with a-in. steel plate.
In an endeavour to follow some sort of sequence of operations in our tour we passed next to the new "line" shop, which has only recently been added to the main works and is not yet fully equipped. At the present it may be regarded as supplementary to the other bearing-making shops, in which the machines are grouped rather than laid out for progressive production methods.
There are to be six lines of machines arranged one each side of three conveyors. For economic operation of this shop, which is designed for mass production, it is, of course, essential that each line be used for the execution of a large order for bearings of the same type. The steel or bronze shells, and white metal or the bronze bushes, arrive at one end and' the bearings are actually packed ready for storing or•dispatch at the other.
To describe here each operation individually is not practicable, hut we must briefly outline the series of processes, pointing out the features of special interest. Before lining, the steel and bronze shells are rough-bored and turned. MEI white-metal linings are die-cast or centrifugally cast into them. The former is the more usual; an interesting point in connection with the latter is that the harder constituents of the metal, which is a mixture of alloys rather than a perfect compound, are, found in greater proportions farther from the axis. Thus at the actual bearing surface the softer constituents preponderate.
After lining, the joint faces are dis6 ground, then the operations of boring, facing the flanges externally and internally, grooving, drilling, mudway cutting, hack-grinding and chamfering are carried out, •
For baring, a diamond or Widia-pointed tool is used, and the cntting speeds may be anything up to 4,000 r.p.m. The finish obtained approaches perfection, and the Glacier concern advocates that bearings should he thus bored, exactly to size, the accuracy obtainable being to within 0.0005 in. The crystalline formation of the hard particles, which, considered microscopically, are supported in a matrix of softer metal, makes a clean cut, as afforded by the methods thus used, of first importance.
Hand scraping or other methods sometimes employed for final bedding are said to disturb these particles, dragging them out of position and tearing the surface of the metal, thus impairing the anti-friction qualities of the bearing. During boring, the half-bearing is mounted in a way which subjects it to exactly the same stresses as are imposed when it is bolted up in its housing. It is retained in position by pressure imposed upon the joint faces by a weight of appropriate mass. Thus, any deformation to which it is subjected in actual use is also caused during this important operation.
The need for grinding the backs of the shells should not be disregarded, as a good bed here is second in importance only to that of the bore. One-half is ground at a time, because the joint faces have, subsequently, to be reduced. Were the half-bearings ground together their backs, after face machining, would not form a perfect cylinder. In grinding, perfect concentricity between bore and back is obtained. Joint-face grinding is done to a gauge whiel ensures accuracy in the "height" of the half-bearing, that is, the height of the bacle,when the joint faces are on a surface plate.
The apparatus and instruments used in the works for this measurement are elaborate, delicate and of extreme accuracy, indicating a discrepancy to 0.0001 in.
In small bearings, oilways are machined. Where there is adequate thickness of white metal they can be die-cast, hut it is clear that if the depth of the groove approaches the thickness of the metal, the latter will not be able to flow into the die. White metal of the minimum thickness is desirable_
We next followed the operations of making a connecting rod. The blanks are first "straddle" milled. Four at a time—two on each side of the machine, of which two the small end of one and the large end of the other are machined simultaneously—have their boss ends faced by two pairs of cutting wheels, between which they are fed.
Then; in the following order, the small ends are drilled, locating faces are milled at the bolt-bole sides of the big ends, the tops and bottoms of the bolt bosses are milled, the bolt holes are drilled and reamed, and the big ends are split. With the rod located by the small end for accuracy of centre-to-centre length, the big end is bored in two cuts—" rough" and "finish." It then passes out of the shop for metalling and returns for the subsequent operations, which are more or leSs.similar to those previously described for bearing halves, but include also the insertion and broaching of the small-end bush.
It must be borne in mind that within the scope of the factory is the production of bearings of a large variety of sizes and types. This necessitates the use of machinery . and equipment to which the same description applies. For each operation that we have named there is probably a number of machines, also others for processes we have not mentioned. We draw attention to this in order to dispel any false impression readers may have formed regarding the simplicity of bearing manufacture, An idea of the size of the works and the array of machines is perhaps better gained by repeating that the employees number Sae One comparatively small shop— almost a small engineering works in itself—is solely engaged in works maintenance, and the conversion of machines and the making of fixtures for special operations, such as the gear for holding the bearings during boring.
Lead-bronze bearings are produced by the Glacier concern, but correctly alloyed white metal is normally recommended for oil engines and, we understand, has 'very rarely failed to give complete satisfaction.
. Among the components in the make-up of the commercial vehicle, the bearings stand high in importance, and upon them largely depends its efficiency. Not Only should manufacturers incorporate, therefore, bearings of high quality, and users in making replacements exercise corresponding, discrimination, but also the advice of specialists should be sought in cases of hearing trouble, Of in planning new, designs.