BREATHE EASIER
Page 66

Page 67
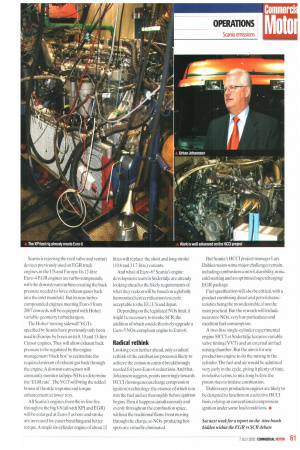
If you've noticed an error in this article please click here to report it so we can fix it.
Scania researchers are already looking towards
life after Euro-6. Alan Bunting reports.
There's no let-up in the controversy about how best to meet the Euro-4,5 and 6 emission limits.The debate hinges on the most effective way of cutting nitrous oxide (NOx): selective catalytic reduction (SCR) and exhaust gas recirculation (EGR) are vying for supremacy.
The champions of EGR, led by MAN, with Scania now falling in behind, concede that SCR is more efficient in neutralising a given amount of NOx. But they point out that if the quantity of NOx leaving the engine can be reduced through 'internal' means, including EGR, then SCR after-treatment is unnecessary. Supporters of EGR also draw attention to the cost, weight and space penalties of the AdBlue urea compound that SCR relies on, as well as supply problems.
In practice, say MAN and Scania, SCR is ideal for making good the shortcomings of older engine designs which tend to produce high quantities of NOx. But new diesel technologies are emerging with ever higher injection pressures leading to more efficient combustion. In combination with cooled EGR they can reduce NOx formation to the 2g/kWh Euro-5 limit andprobably even to the expected Euro-6 level of lg/kWh. "There is no ceiling above which we would gain no emission, fuel economy or performance advantages," says Scania powertrain supremo Urban Johansson. Its XPI fuel system technology, being developed in collaboration with Cummins in a follow-up to the HPI programme, will herald the vital injection pressure breakthrough.
However. HPI and XPI have little in common.The former is an engine camshaft actuated electronic unit-injector (EUI) system, though its 'open nozzle' injector tip and use of pressure intensifiers contrasts with the older 'closed nozzle' EU I design from Bosch (inherited from Detroit Diesel) which is found on most Scania engines.
Basic principles
But XPI is a common-rail system, the basic principles of which are now well known. Full rail pressure is available at any engine speed or load, right down to clutch-engagement conditions, where torque can be greatly enhanced. Until now the highest pressure available from a truck diesel common rail system (from I3osch,on MAN's 1)20 and Cummins' latest ISBe engines) is around 1,600 bar. However, the XPI system will boost potential common rail-pressure to 2,200 bar (32,300psi).
Jonas Hofstedt, Scania's head of engine development, reports that, unlike the nextgeneration Bosch APCRS common-rail system for trucks (which will be used by DaimlerChrysler on its all-new 9.9,12.8,14.8 and 15.6 Litre inline sixes due in 2007) X PI does not feature stepped-piston pressure intensification/ amplification.APCRS has a 2.5:1 intensifier for each injector, so a modest 900-bar rail pressure can generate 2250 bar at the nozzle. Common-rail technology has advanced to the point where durability concerns have been overcome. Higher-grade steels and greater machining precision allow tighter joint and seal tolerances to obviate leaks.
The XPI fuel system, which is scheduled to be introduced on a revised range of Euro-5 Scania engines in 2007, will radically affect the company's NOx emission control strategy. The use of SCR at Euro-4 on 16-litre V8 R-Series chassis, and on non-turbo-compound in-line-engined models, will be abandoned in favour of the XPI-EGR combination.
Hofstedt says these two 'engine internal' technologies will work together to match SCR's performance on NOx reduction and, crucially, fuel consumption. But there will be some trade-off in speed of injection. because advantage will also be taken of the generous pressure to 'force' the fuel through smaller nozzle spray holes, leading to better fuel atomisation and more complete combustion, in the interests of particulate emissions and fuel consumption.
Oxidation catalyst
Scania does not expect to need a DPF (diesel particulate filter) at Euro-5,but it will probably fit an oxidation catalyst to 'mop up' VOCs (volatile organic compounds),— non-solids measured under the heading of particulates.
Quicker injection will allow the start of injection to be delayed, so the peak of the fuelbum also occurs further beyond top-deadcentre, when the piston is falling.This will shift combustion-generated peak pressures away from the 'mechanically' created peaks caused by the rising piston. In turn maximum pressures and the resulting temperatures on which NOx formation depends, will fall. Less NOx is formed so the more modest NOx control capability of R (compared with SCR) will be sufficient to meet Euro-5.
EGR is a fairly straightforward principle, but the practicality of transferring gas at low exhaust system pressure into the turbopressurised inlet manifold is a challenge.
It could be avoided by introducing the exhaust gas upstream of the turbo, where there would be no adverse pressure gradient, but that would mean recirculated exhaust gas having to pass through the compressor wheel of the turbocharger and then through the air passageways of the charge-cooler. This, in turn, would risk a gradual build-up of' carbon hampering the flow anclioracidic corrosion, even from the exhaust of a 'clean' Euro-4 or 5 engine. Scania is rejecting the reed valve and venturi devices previously used on EGR truck engines, in the US and Europe. Its 12-litre Euro-4 EGR engines are turbo-compounds, with the downstream turbine creating the back pressure needed to force exhaust gases back into the inlet manifold. But its non-turbocompounded engines, meeting Euro-5 from 2007 onwards, will be equipped with Holset variable-geometry turbochargers.
The Ho[set:moving sidevvall' VGTs specified by Scania have previously only been used in Europe by Iveco on its 8,10 and 13-litre Cursor engines. They will allow exhaust back pressure to be regulated by the engine management 'black box to recirculate the required amount of exhaust gas back through the engirte.A downstream sensor will constantly monitor tailpipe NOx to determine the `EGR rate'. The VGT will bring the added bonus of throttle response and torque enhancement at lower revs.
All Scania's engines, from the in-line five through to the big V8 (all with XPI and EGR) will be enlarged at Euro-5 as bore and stroke are increased for easier breathing and better torque.A single six-cylinder engine of about 12 litres will replace the short and long-stroke (10.6 and 11.7-litre) variants.
And what of Euro-6? Scania's engine development team in Sadertalje are already looking ahead to the likely requirements of what they reckon will be based on a globally harmonised test/certification test cycle acceptable to the ELL US and Japan.
Depending on the legislated NOx limit, it might be necessary to invoke SCR, the addition of which could effectively upgrade a Euro-5 NOx-compliant engine to Euro-6.
Radical rethink Looking even further ahead, only a radical rethink of the combustion process is likely to achieve the emission control breakthrough needed for post-Euro-6 reductions. And that, Johansson suggests, points unerringly towards HCCI (homogeneous charge compression ignition) technology: the essence of which is to mix the fuel and air thoroughly before ignition begins. Then it happens simultaneously and evenly throughout the combustion space, without the traditional flame front moving through the charge, so NOx-producing hotspots are virtually eliminated. But Scania's HCCI project manager Lars Dahlen warns some major challenges remain, including combustion con trol, durabili ty, noise, cold starting and an optimised supercharging! EGR package.
Fuel specification will also be critical, with a product combining diesel and petrol characteristics being the most desirable, if not the most practical. But the rewards will include near-zero NOx, very low particulates and excellent fuel consumption.
A two-litre single-cylinder experimental engine HCCI at SOderiiilje features variable valve timing (VVT) and an external air/fuel mixing chamber. But the aim is for any production engine to do the mixing in the cylinder.The fuel and air would be admitted very early in the cycle, giving it plenty of time, in relative terms, to mix; long before the piston rises to initiate combustion.
Dahlen says production engines are likely to he designed to function on a selective HCCI basis, relying on conventional compression ignition under some load conditions. si See next week for a report on the time bomb hidden within the EGR vs SCR debate