Given the amount of legislation thrown at them each year,
Page 32
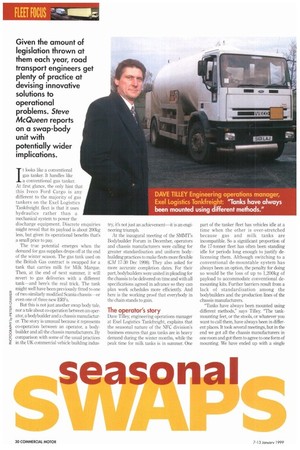
Page 33
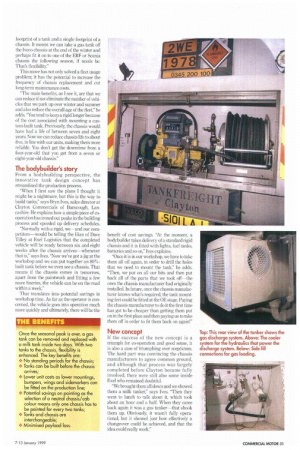
If you've noticed an error in this article please click here to report it so we can fix it.
road transport engineers get plenty of practice at devising innovative solutions to operational problems. Steve McQueen reports on a swap-body unit with potentially wider implications.
/t looks like a conventional gas tanker. It handles like a conventional gas tanker. At first glance, the only hint that this Iveco Ford Cargo is any different to the majority of gas tankers on the Exel Logistics Tankfreight fleet is that it uses hydraulics rather than a mechanical system to power the discharge equipment. Discrete enquiries might reveal that its payload is about 200kg less, but given its operational benefits that's a small price to pay.
The true potential emerges when the demand for gas supplies drops off at the end of the winter season. The gas tank used on the British Gas contract is swapped for a tank that carries milk for Milk Marque. Then, at the end of next summer, it will revert to gas deliveries with a different tank and here's the real trick. The tank might well have been previously fitted to one of two similarly modified Scania chassis—or even one of three new ERFs.
But this is not just another swap body tale, nor a tale about co-operation between an operator, a bodybuilder and a chassis manufacturer. The story is unusual because it represents co-operation between an operator, a bodybuilder and all the chassis manufacturers. By comparison with some of the usual practices in the UK commercial vehicle building indus
try, it's not just an achievement—it is an engineering triumph.
At the inaugural meeting of the SMMT's Bodybuilder Forum in December, operators and chassis manufacturers were calling for greater standardisation and uniform bodybuilding practices to make fleets more flexible (CM 17-30 Dec 1998). They also asked for more accurate completion dates. For their part, bodybuilders were united in pleading for the chassis to be delivered on time and with all specifications agreed in advance so they can plan work schedules more efficiently. And here is the working proof that everybody in the chain stands to gain.
The operator's story
Dave Tilley, engineering operations manager at Exel Logistics Tankfreight, explains that the seasonal nature of the NFC division's business ensures that gas tanks are in heavy demand during the winter months, while the peak time for milk tanks is in summer. One part of the tanker fleet has vehicles idle at a time when the other is over-stretched because gas and milk tanks are incompatible. So a significant proportion of the 17-tormer fleet has often been standing idle for periods long enough to justify delicensing them. Although switching to a conventional de-mountable system has always been an option, the penalty for doing so would be the loss of up to 1,200kg of payload to accommodate conventional demounting kits. Further barriers result from a lack of standardisation among the bodybuilders and the production lines of the chassis manufacturers.
"Tanks have always been mounted using different methods," says Tilley. "The tankmounting feet, or the stools, or whatever you want to call them, have always been in different places. It took several meetings, but in the end we got all the chassis manufacturers in one room and got them to agree to one form of mounting. We have ended up with a single footprint of a tank and a single footprint of a chassis. It means we can take a gas tank off the Iveco chassis at the end of the winter and perhaps fit it on to one of the ERF or Scania chassis the following season, if needs be. That's flexibility."
This move has not only solved a fleet usage problem; it has the potential to increase the frequency of chassis replacement and cut long-term maintenance Lusts.
"The main benefits, as I see it, are that we can reduce if not eliminate the number of vehicles that we park up over winter and summer and also reduce the overall age of the fleet," he adds. "You tend to keep a rigid longer because of the cost associated with mounting a custom-built tank. Previously, the chassis would have had a life of between seven and eight years. Now we can reduce chassis life to about five, in line with our units, making them more reliable, You don't get the downtime from a four-year-old that you get from a seven or eight-year-old chassis."
The bodybuilder's story
From a bodybuilding perspective, the innovative tank design concept has streamlined the production process.
"When I first saw the plans I thought it might be a nightmare, but this is the way to build tanks," says Bryn Ives, sales director at Clayton Commercials of Burscough, Lancashire. He explains how a simple piece of cooperation has ironed out peaks in the building process and speeded up delivery schedules.
"Normally with a rigid, we—and our competitors—would be telling the likes of Dave Tilley at Exel Logistics that the completed vehicle will be ready between six and eight weeks after the chassis arrives—whenever that is," says Ives. "Now we've got a jig at the workshop and we can put together an 80%built tank before we even see a chassis. That means if the chassis comes in tomorrow, apart from the paintwork and fitting a few more fineries, the vehicle can be on the road within a week."
That translates into potential savings in workshop time. As far as the operator is concerned, the vehicle goes into operation much more quickly and ultimately, there will be the benefit of cost savings. "At the moment, a bodybuilder takes delivery of a standard rigid chassis and it is fitted with lights, fuel tanks, batteries and so on," Ives explains.
"Once it is in our workshop, we have to take them all off again, in order to drill the holes that we need to mount the tank," he adds. "Then, we put on all our bits and then put back all of the parts that we took off—the ones the chassis manufacturer had originally installed. In future, once the chassis manufacturer knows what's required, the tank mounting feet could be fitted at the OE stage. Paying the chassis manufacturer to do it the first time has got to be cheaper than getting them put on in the first place and then paying us to take them off in order to fit them back on again!"
New concept
If the success of the new concept is a triumph for co-operation and good sense, it is also a case of triumphing over scepticism. The hard part was convincing the chassis manufacturers to agree common ground, and although that process was largely completed before Clayton became fully involved, there were still also some inside Exel who remained doubtful.
"We brought them all down and we showed them a milk tanker," says Ives. "Then they went to lunch to talk about it, which took about an hour and a half. When they came back again it was a gas tanker—that shook them up. Obviously, it wasn't fully operational, but it showed just how effectively a changeover could be achieved, and that the idea could really work."