Purle in the waste disposal oyster
Page 81
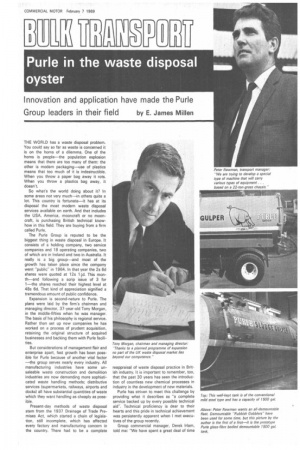
Page 82
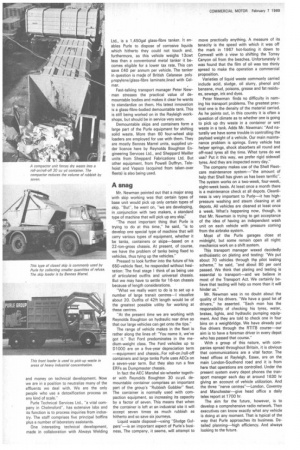
If you've noticed an error in this article please click here to report it so we can fix it.
Innovation and application have made the Purle
Group leaders in their field by E. James Millen
THE WORLD has a waste disposal problem. You could say so far as waste is concerned it is on the horns of a dilemma. One of the horns is people—the population explosion means that there are too many of them: the other is modem packaging—use of plastics means that too much of it is indestructible. When you throw a paper bag away it rots. When you throw a plastics bag away, it doesn't.
So what's the world doing about it? In some areas not very much—in others quite a lot. This country is fortunate—it has at its disposal the most modern waste disposal services available on earth. And that includes the USA. America, rnooncraft or no mooncraft, is purchasing British technical knowhow in this field. They are buying from a firm called Purle.
The Purle Group is reputed to be the biggest thing in waste disposal in Europe. It consists of a holding company, two service companies and 18 operating companies, two of which are in Ireland and two in Australia. it really is a big group—and most of the growth has taken place since the company went "public" in 1964. In that year the 2s 6d shares were quoted at 12s 11d. This month—and following a scrip issue of 3 for 1—the shares reached their highest level at 48s 6d. That kind of appreciation signified a tremendous amount of public confidence.
Expansion is second-nature to Pude. The plans were laid by the firm's chairman and managing director. 37-year-old Tony Morgan, in the middle-fifties when he was manager. The basis of his philosophy is regional service. Rather than set up new companies he has worked on a process of prudent acquisition, retaining the original structure of acquired businesses and backing them with Purle facilities.
But considerations of management flair and enterprise apart, fast growth has been possible for Purle because of another vital factor —the group serves nearly every industry. All manufacturing industries have some unsaleable waste construction and demolition industries are now demanding more sophisticated waste handling methods; distributive services (supermarkets, railways, airports and docks) all have substantial quantities of waste which they want handling as cheaply as possible.
Present-day methods of waste disposal stem from the 1937 Drainage of Trade Premises Act, which started a chain of legislation, still incomplete, which has affected every factory and manufacturing concern in the country. There had to be a complete reappraisal of waste disposal practice in British industry. It is important to remember, too, that the past 30 years has seen the introduction of countless new chemical processes in industry in the development of new materials.
Purle has striven to meet this challenge by providing what it describes as "a complete service backed up by every possible technical aid". Technical proficiency is dear to their hearts and this pride in technical achievement was persistently apparent when I met executives of the group recently.
Group commercial manager, Derek !dam, told me: –We have spent a great deal of time
and money on technical development. Now we are in a position to neutralize many of the effluents we deal with. We are the only people who use a detoxification process on any kind of scale."
Purle Technical Services Ltd., "a vital company in Chelmsford-, has extensive labs and its function is to process inquiries from industry. The staff comprises five principal boffins plus a number of laboratory assistants.
One interesting technical development, made in collaboration with Always Welding Ltd., is a 1,450ga1 glass-fibre tanker. It enables Purle to dispose of corrosive liquids which hitherto they could not touch and, furthermore, as this vehicle weighs 13cwt less than a conventional metal tanker it becomes eligible for a lower tax rate. This can save £40 per annum per vehicle. The tanker in question is made of British Celanese poly propylene/glass-fibre laminate,lined with Celmar.
Fast-talking transport manager Peter Newman stresses the practical value of demountable bodies and makes it clear he wants to standardize on them. His latest innovation is a glass-fibre-bodied demountable tank. This is still being worked on in the Rayleigh workshops, but should be in service very soon.
Demountable skips and containers form a large part of the Purle equipment for shifting solid waste. More than 60 four-wheel skip loaders are employed for use with them. They are mostly Bennes Marrel units, supplied under licence here by Reynolds Boughton Engineering Services Ltd., and Sheppard MeiIler units from Sheppard Fabrications Ltd. But other equipment, from Powell Duffryn, Telehoist and Vapsco (acquired from taken-over fleets) is also being used.
Mr. Newman pointed out that a major snag with skip working was that certain types of base unit would pick up only certain types of skip. "But", he went on, "we are developing, in .conjunction with two makers, a standard type of machine that will pick up any skip:' "The most important thing that Purle is trying to do at this time," he said, "is to develop one special type of machine that will carry various types of equipment, whether it be tanks, containers or skips—based on a 22-ton-gross chassis. At present, of course, we have the problem of tanks being fixed to vehicles, thus tying up the vehicles."
Pressed to look further into the future of his 650-vehicle fleet, he responded without hesitation: The final stage I think of as being use of articulated outfits and universal chassis. But we may have to settle for 16-ton chassis because of length considerations.
'What we really want to do is to set up a number of large transit centres— I visualize about 20. Outfits of 42ft length would be of the greatest possible utility for working at these centres.
"At the present time we are working with Reynolds Boughton on hydraulic rear drive so that our large vehicles can get onto the tips."
The range of vehicle makes in the fleet is rather along the lines of: "You name it, we've got it." But Ford predominates in the medium-weight class. The Ford vehicles up to D1000 are on a five-year depreciation term —equipment and chassis. For roll-on /roll-off containers and large tanks Purle uses AECs on a seven-year term. But they also run a few ERFs as Dumpmaster chassis.
In fact the AEC Marshal six-wheeler together with Reynolds Boughton 30 cu.yd, demountable container comprises an important part of the group's "Rubbish Gobbler" fleet. The container is normally used with compaction equipment, so increasing its capacity by a factor of seven. This means that when the container is left at an industrial site it will accept seven times as much rubbish as hitherto and so save six journeys.
Liquid waste disposal—using "Sludge Gulpers"—is an important aspect of Purle's business. The company, it seems, will attempt to move practically anything. A measure of its tenacity is the speed with which it was off the mark in 1967 hot-footing it down to Cornwall with a view to shifting the Torrey Canyon oil from the beaches. Unfortunately it was found that the film of oil was too thinly spread to make the operation a commercial proposition.
Varieties of liquid waste commonly carried include acid, sludge, oil slurry, phenol and benzene, mud, poisons, grease and fat residues, sewage, ink and dyes.
Peter Newman finds no difficulty in naming his transport problems. The greatest practical one is the density of the material carried. As he points out, in this country it is often a question of climate as to whether one is going to pick up dry waste in a container or wet waste in a tank. Adds Mr. Newman: "And naturally we have some trouble in controlling the payload weight of a vehicle. Our main maintenance problem is springs. Every vehicle has helper springs, shock absorbers all round and off-road tyres all the time. What tyres do we use? Put it this way, we prefer rigid sidewall tyres. And they are inspected every day."
The company makes use of the Shell Fleetcare maintenance system—"the amount of help that Shell has given us has been terrific", The system works on a two-week, four-week, eight-week basis. At least once a month there is a maintenance check at all depots. Cleanliness is very important to Purle—it has highpressure washing and steam cleaning at all depots. All vehicles are cleaned at least once a week. What's happening now, though, is that Mr. Newman is trying to get acceptance of the idea of having an independent wash unit on each vehicle with pressure coming from the airbrake system.
Most of the Purle garages close at midnight, but some remain open all night: mechanics work on a shift system.
This transport manager waxed decidedly enthusiastic on plating and testing: 'We put about 70 vehicles through the pilot testing scheme," he said, "and about 80 per cent passed. We think that plating and testing is essential to transport—and we believe in most of the Transport Act. We certainly believe that testing will help us more than it will hinder us."
Mr. Newman was in no doubt about the quality of his drivers. "We have a good lot of drivers," he asserted. "Each man has the responsibility of checking his tyres, water, brakes, lights, and hydraulic pumping equipment. And they are told to check one in four bins on a weighbridge. We have already put five drivers through the RTITB course—our aim is to have a foreman driver in every depot who has passed that course."
With a group of this nature, with companies spread throughout Britain, it is obvious that communications are a vital factor. The head offices at Rayleigh, Essex, are on the main London-Southend road and it is from here that operations are controlled. Under the present system every depot phones the transport manager each day at around 1630 hr giving an account of vehicle utilization. And the three "nerve centres"—London, Coventry and Manchester—give head office a daily telex report at 1700 hr.
The aim for the future, however, is to develop a comprehensive radio network. Then executives can know exactly what any vehicle is doing at any moment. That is typical of the way that Purle approaches its business. Detailed planning—high efficiency. And always looking to the future.