The best for bulk powder?
Page 58
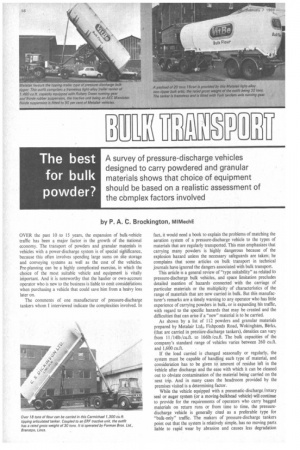
Page 59
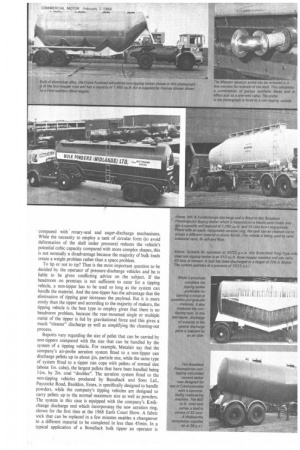
Page 60
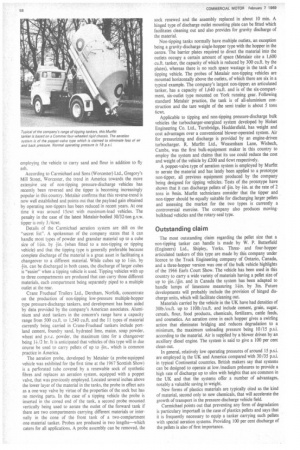
If you've noticed an error in this article please click here to report it so we can fix it.
by P. A. C. Brockington, MIMechE
OVER the past 10 to 15 years, the expansion of bulk-vehicle traffic has been a major factor in the growth of the national economy. The transport of powders and granular materials in vehicles with a power-discharge system is of special significance, because this often involves spending large sums on site. storage and conveying systems as well as the cost of the vehicles. Pre-planning can be a highly complicated exercise, in which the choice of the most suitable vehicle and equipment is vitally important. And it is noteworthy that the haulier or own-account operator who is new to the business is liable to omit considerations when purchasing a vehicle that could save him from a heavy loss later on.
The comments of one manufacturer of pressure-discharge tankers whom I interviewed indicate the complexities involved. In fact, it would need a book to explain the problems of matching the aeration system of a pressure-discharge vehicle to the types of materials that are regularly transported. This man emphasizes that carrying many powders is highly dangerous because of the explosion hazard unless the necessary safeguards are taken; he complains that some articles on bulk transport in technical journals have ignored the dangers associated with bulk transport.
This article is a general review of "type suitability" as related to pressure-discharge bulk vehicles, and space limitation precludes detailed mention of hazards connected with the carriage of particular materials or the multiplicity of characteristics of the range of materials that are now carried in bulk. But this manufacturer's remarks are a timely warning to any operator who has little experience of carrying powders in bulk, or is expanding his traffic, with regard to the specific hazards that may be created and the difficultieS that can arise if a "new" material is to be carried.
As shown by a list of 112 powders and granular materials prepared by Metalair Ltd., Fishponds Road, Wokingharn, Berks, (that are carried in pressure-discharge tankers), densities can vary from 11 /141b /cu.fi. to 166113/cu.ft. The bulk capacities of the company's standard range of vehicles varies between 260 tuft. and 1,600 cult.
If the load carried is changed seasonally or regularly, the system must be capable of handling each type of material, and consideration has to be given to amount of residue left in the vehicle after discharge and the ease with which it can be cleaned out to obviate contamination of the material being carried on the next trip. And in many cases the headroom provided by the premises visited is a determining factor.
While the vehicle equipped with a pneumatic-discharge /rotary seal or auger system (or a moving-bulkhead vehicle) will continue to provide for the requirements of operators who carry bagged materials on return runs or from time to time, the pressuredischarge vehicle is generally cited as a preferable type for "bulk-only" traffic. The makers of 'pressure-discharge tankers point out that the system is relatively simple, has no moving parts liable to rapid wear by abrasion and causes less degradation compared with rotary-seal and auger-dischargemechanisms. While the necessity to employ a tank of circular form (to avoid deformation of the shell •under pressure) reduces the vehicle's potential cubic capacity compared with more complex shapes, this is not normally a disadvantage because the majority of bulk loads create a weight problem rather than a space problem.
To tip or not to tip? That is the most important question to be decided by the operator of pressure-discharge vehicles and he is liable to be given conflicting advice on the subject. If the headroom on premises is not sufficient to cater for a tipping vehicle, a non-tipper has to be used so long as the system can handle the material. And the non-tipper has the advantage that the elimination of tipping gear increases the payload. But it is more costly than the tipper and according to the majority of makers, the tipping vehicle is the best type to employ given that there is no headroom problem, because the rear-mounted single or multiple outlet of the tipper is fed by gravitational force and this gives a much "cleaner" discharge as well as simplifying the cleaning-out process.
Reports vary regarding the size of pellet that can be carried by non-tippers compared with the size that can be handled by the system of a tipping vehicle. For example, Metalair say that the company's air-probe aeration system fitted to a non-tipper can discharge pellets up to.about kin. particle size, while the same type of system fitted to a tipper can cope with pellets of normal size (about lin. cube), the largest pellets that have been handled being by 2in. coal "doubles". The aeration system fitted to the non-tipping vehicles produced by Bonallack and Sons Ltd., Paycocke Road, Basildon, Essex, is specifically designed to handle powders, while the company's tipping vehicles are designed to carry pellets up to the normal maximum size as well as powders. The system in this case is equipped with the company's Kwikchange discharge end which incorporates the new aeration ring, shown for the first time at the 1968 Earls Court Show. A fabric sock that can be replaced in a few minutes enables a changeover to a different material to be completed in less than 45min. In a typical application of a Bonallack bulk tipper an operator is employing the vehicle to carry sand and flour in addition to fly ash.
According to Carmichael and Sons (Worcester) Ltd., Gregory's Mill Street, Worcester, the trend in America towards the more extensive use of non-tipping pressure-discharge vehicles has recently been reversed and the tipper is becoming increasingly popular in this country. Metalair confirms that this reverse-trend is now well established and points out that the payload gain obtained by operating non-tippers has been reduced in recent years. At one time it was around 15cwt with maximum-load vehicles. The penalty in the case of the latest Metalair-bodied 30/32-ton g.v.w. tipper is only 3 /4cwt.
Details of the Carmichael aeration system are Still on the "secret list". A spokesman of the company states that it can handle most types of powder and granular material up to a cube size of 14-in, by -in. (when fitted to a non-tipping or tipping vehicle) and that the tipping type is generally preferable because complete discharge of the material is a great asset in facilitating a changeover to a different material. While cubes up to 44n. by ;-in. can be discharged in both cases, the discharge of larger cubes is "easier" when a tipping vehicle is used. Tipping vehicles with up to three compartments are produced that can carry three different materials, each compartment being separately piped to a multiple outlet at the rear.
Crane Fruehauf Trailers Ltd., Dereham. Norfolk, concentrate on the production of non-tipping low-pressure multiple-hopper type pressure-discharge tankers, and development has been aided by data provided by the company's American associates. Aluminium and steel tankers in the concern's range have a capacity range from 500 cu.ft. to 1,540 cu.ft. and the 11 types of material currently being carried in Crane-Fruehauf tankers include portland cement, foundry sand, hydrated lime, maize, soap powder, wheat and p.v.c. powder, the maximum time for a changeover being 4/2 hr. It is anticipated that vehicles of this type will in due course be used to carry pellets of up to;lin., which is common practice in America.
The aeration probe, developed by Metalair (a probe-equipped vehicle was exhibited for the first time at the 1967 Scottish Show) is a perforated tube covered by a renewable sock of synthetic fibres and replaces an aeration system, equipped with a poppet valve, that was previously employed. Located several inches above the lower layer of the material in the tanks, the probe in effect acts as a one-way valve by virtue of the properties of the sock but has no moving parts. In the case of a tipping vehicle the probe is inserted in the coned end of the tank, a second probe mounted vertically being used to aerate the outlet of the forward tank if there are two compartments carrying different materials or internally in the cone of the front tank of a two-compartment one-material tanker. Probes are produced in two lengths—which caters for all applications. A probe assembly can be removed, the sock renewed and the assembly replaced in about 10 min. A hinged type of discharge outlet mounting plate can be fitted which facilitates cleaning out and also provides for gravity discharge of the material.
Non-tipping tanks normally have multiple outlets, an exception being a gravity-discharge single-hopper type with the hopper in the centre. The barrier plates required to direct the material into the outlets occupy a certain amount of space (Metalair cite a 1,600 cu.ft. tanker, the capacity of which is reduced by 300 cu.ft. by the plates), whereas there is no such space wastage in the tank of a tipping vehicle. The probes of Metalair non-tipping vehicles are mounted horizontally above the outlets, of which there are six in a typical example. The company's largest non-tipper; an articulated tanker, has a capacity of 1,640 cu.ft. and is of the six-compartment, six-outlet type mounted on York running gear. Following standard Metalair practice, the tank is of all-aluminium construction and the tare weight of the semi trailer is about 5 tons 6cwt.
Applicable to tipping and non-tipping pressure-discharge bulk vehicles the turbocharger-energized system developed by Ho!set Engineering Co. Ltd., Turnbridge, Huddersfield, has weight and cost advantages over a conventional blower-operated system. Air for pressurizing and discharge is provided by an engine-driven turbocharger. R. Murfitt Ltd., Weasenham Lane, Wisbech, Cambs, was the first bulk-equipment maker in this country to employ the system and claims that its use could reduce the cost and weight of the vehicle by £200 and 6cwt respectively.
A poppet-valve, type of aeration system is employed by Murfitt to aerate the material and has lately been applied to a prototype non-tipper, all previous equipment produced by the company being designed for tipping vehicles. Tests of the prototype have shown that it can discharge pellets of -kin. by 4-in, at the rate of 2 tons in 9min. Murfitt technicians consider that the tipper and non-tipper should be equally suitable for discharging larger pellets and assessing the market for the two types is currently a controversial exercise. The company also produces movingbulkhead vehicles and the rotary-seal type.
Outstanding claim
The most outstanding claim regarding the pellet size that a non-tipping tanker can handle is made by W. P. Butterfield (Engineers) Ltd., Shipley, Yorks. Threeand four-hopper articulated tankers of this type are made by this company under licence to the Truck Engineering company of Ontario, Canada, and a three-hopper version was one of the bulk vehicle highlights of the 1966 Earls Court Show. The vehicle has been used in this country to carry a wide variety of materials having a pellet size of up to +in. /in. and in Canada the system has been adapted to handle lumps of limestone measuring 14-in, by 3in. Future developments will probably include the provision of hinged discharge units, which will facilitate cleaning out.
Materials carried by the vehicle in the UK have had densities of 301b /cult. up to 1101b /cu.ft. and include cement, grain, sugar, cereals, flour, food products, chemicals, fertilizers, cattle feeds, and cosmetics. An aeration cone in each hopper gives a swirling action that eliminates bridging and reduces degradation to a minimum, the maximum unloading pressure being 10/15 p.s.i. according to the material. Air is supplied by a blower driven by an auxiliary diesel engine. The system is said to give a 100 per cent clean-out.
In general, relatively low operating pressures of around 15 p.s.i. are employed in the UK and America compared with 30/35 p.s.i. in typical Continental countries. British makers say that systems can be designed to operate at low /medium pressures to provide a high rate of discharge up to silos with heights that are common in the UK and that the systems offer a number of advantages, notably a valuable saving in weight.
New forms of plastics materials are typically cited as the kind of material, second only to new chemicals, that will accelerate the growth of transport in the pressure-discharge vehicle field.
Carmichael points out that preventing any form of degradation is particulary important in the case of plastics pellets and says that it is frequently necessary to equip a tanker carrying such pellets with special aeration systems. Providing 100 per cent discharge of the pellets is also of first importance.