Tanker stability trials: a first-hand report
Page 56
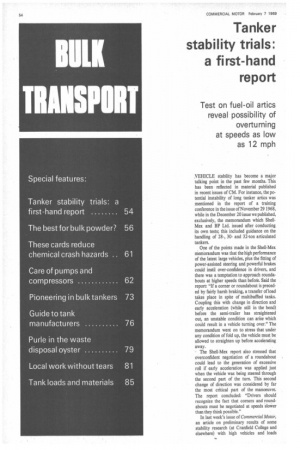
Page 57
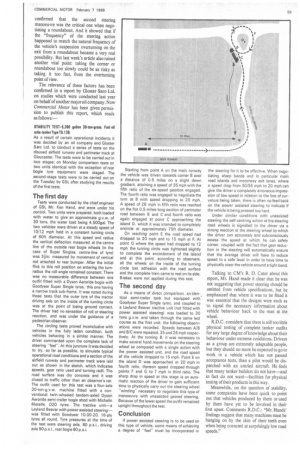
If you've noticed an error in this article please click here to report it so we can fix it.
VEHICLE stability has become a major talking point in the past few months. This has been reflected in material published in recent issues of CM. For instance, the potential instability of long tanker artics was mentioned in the report of a training conference in the issue of November 29 1968, while in the December 20 issue we published, exclusively, the memorandum which ShellMex and BP Ltd. issued after conducting its own tests; this included guidance on the handling of 28-, 30and 32-ton articulated tankers.
One of the points made in the Shell-Mex memorandum was that the high performance of the latest large vehicles, plus the fitting of power-assisted steering and powerful brakes could instil over-confidence in drivers, and there was a temptation to approach roundabouts at higher speeds than before. Said the report: "If a corner or roundabout is preceded by fairly harsh braking, a transfer of load takes place in spite of multibaffled tanks. Coupling this with change in direction and early acceleration (while still in the bend) before the semi-trailer has straightened out, an unstable condition can arise which could result in a vehicle turning over." The memorandum went on to stress that under any condition of fold up, the vehicle must be allowed to straighten up before accelerating away.
The Shell-Mex report also stressed that overconfident negotiation of a roundabout could lead to the generation of excessive roll if early acceleration was applied just when the vehicle was being steered through the second part of the turn. This second change of direction was considered by far the most critical part of the manoeuvre. The report concluded: "Drivers should recognize the fact that corners and roundabouts must be negotiated at speeds slower than they think possible."
In last week's issue of Commercial Motor, an article on preliminary results of some stability research (at Cranfield College and elsewhere) with high vehicles and loads confirmed that the second steering manoeuvre was the critical one when negotiating a roundabout. And it showed that if the "frequency" of the steering action happened to match the natural frequency of the vehicle's suspension overturning on the exit from a roundabout became a very real possibility. But last week's article also raised another vital point: taking the corner or roundabout too slowly could be as risky as taking it too fast, from the overturning point of view.
The relevance of these factors has been confirmed in a report by Gloster Saro Ltd. on studies which were conducted last year on behalf of another major oil company. Now Commercial Motor has been given permission to publish this report, which reads as follows:—
STABILITY TEST-5,300 gallon 30-ton-gross. Fuel oil artic-tanker Type TS.138.
As a result of certain operational incidents it was decided by an oil company and Gloster Saro Ltd. to conduct a series of tests on the disused airfield runway and perimeter track at Gloucester. The tests were to be carried out in two stages: on Monday comparison tests on two units identical with the exception of rear bogie tyre equipment were staged. The second-stage tests were to be carried out on the Tuesday by GSL after studying the results of the first tests.
The first day
Tests were conducted by the chief engineer of GSL Mr. Ken Hand, and were under his control. Two units were prepared, both loaded with water to give an approximate g.v.w. of 30 tons, the water load being 4,500gal. The two vehicles were driven at a steady speed of 10/12 mph held in a constant turning circle of 60ft diameter. At this speed and radius the vertical deflection measured at the centre line of the outside rear bogie wheels (in the case of Super Singles, centre-line of tyre) was 3-1-in. measured by movement of vertical rod attached to rear bumper. After the initial flick to this roll position on entering the turnradius the roll-angle remained constant. There was no measurable difference between one outfit fitted with a Dyson Aeroride bogie with Goodyear Super Single tyres. this one having a narrow track sub-frame. It was noted during these tests that the outer tyre of the tractor driving axle on the inside of the turning circle was at the point of losing ground contact. The driver had no sensation of roll or steering reaction, and was under the guidance of a pedestrian observer.
The circling tests proved inconclusive with vehicles in the fully laden condition, both vehicles behaving in a similar manner. The driver commented upon the complete lack of steering "feel". At this juncture it was decided to try, so far as possible, to simulate typical operational road conditions and a section of the airfield runway and perimeter track were laid out as shown in the sketch, which indicates speeds, gear ratio used and turning radii. The road surface was dry concrete and it was closed to traffic other than an observer's car. The outfit used for this test was a four-axle 30-ton-g.v.w. machine fitted with a conventional twin-wheeled tandem-axled Dyson Aeroride semi-trailer bogie shod with Michelin Metallic D20 tyres. The tractive unit—a Leyland Beaver with power assisted steering— was fitted with Goodyear 10.00-20, 16-ply tyres all round. Tyre pressures at the time of the test were steering axle, 80 p.s.i., driving axle 90 p.s.i., rear bogie 80 p.s.i. Starting from point A on the main runway the vehicle was driven towards corner B over a distance of 0.5 miles on a slight down gradient, attaining a speed of 35 mph with the fifth ratio of the six-speed gearbox engaged. The fourth ratio was engaged to negotiate the turn at B with speed dropping to 20 mph. A speed of 26 mph in fifth ratio was reached on the flat 0,5-miles-long section of perimeter road between B and C and fourth ratio was again engaged at point C approaching the island D, which it was intended to completely encircle at approximately 75ft diameter.
On reaching point E the road speed had dropped to 20 mph and to 15 mph at F. At point G where the speed had dropped to 12 mph the turning circle was tightened slightly to complete the encirclement of the island and at this point, according to observers, all the wheels on the inside of the turning circle lost adhesion with the road surface and the complete train came to rest on its side. Brakes were not applied during this test.
The second day
As a means of direct comparison, an identical semi-trailer tank but equipped with Goodyear Super Single tyres, and coupled to a Leyland Beaver tractive unit (not fitted with power assisted steering) was loaded to 30 tons g.v.w. and taken through the same test course as the first unit. the following observations were recorded. Speeds between A/B and B/C were repeated, 35 and 26 mph respectively. At the turning B, it was necessary to make several hand movements on the steering wheel as compared with a single action with the power assisted unit, and the road speed of the vehicle dropped to 15 mph. Point E on the island D was approached at 20 mph in fourth ratio, thereon speed dropped through points F and G to 7 mph in third ratio. The sharp drop in speed at this stage is an automatic reaction of the driver to gain sufficient time to physically carry out the steering wheel "winding" necessary to negotiate this type of manoeuvre with unassisted geared steering. Because of the lower speed the outfit remained upright throughout the test.
Conclusion
If power assisted steering is to be used on this type of vehicle, some means of achieving a degree of "feel" must be incorporated in the steering for it to be effective. When negotiating sharp bends and in particular main road islands and motorway exit lanes, where a speed drop from 50/55 mph to 20 mph can give the driver a completely erroneous impression of low speed in relation to the line of curvature being taken, there is often no feed back on the power assisted steering to indicate if the vehicle is being pressed too hard.
Under similar conditions with unassisted steering the self-centring action of the steering road wheels is signalled to the driver via a strong reaction at the steering wheel by which the driver can accurately and subconsciously assess the speed at which he can safely corner, coupled with the fact that gear reduction in the steering will automatically ensure that the average driver will have to reduce speed to a safe level in order to have time to physically steer the vehicle around a tight bend.
Talking to CM's R. D. Cater about this report, Mr. Hand made it clear that he was not suggesting that power steering should be omitted from vehicle specifications, but he emphasized that where it was to be fitted it was essential that the designs were such as to signal the necessary information about vehicle behaviour back to the man at the wheel.
R.D.C. considers that there is still too little physical testing of complete tanker outfits for any large degree of knowledge about their behaviour under extreme conditions. Drivers as a group are extremely adaptable people, but they should no more be expected to go to work in a vehicle which has not passed acceptance tests, than a pilot would be dispatched with an untried aircraft. He feels that many tanker builders do not have—and in fact do not want—facilities for physical testing of their products in this way.
Meanwhile, on the question of stability, some companies have been quick to point out that vehicles produced by them or used by them have yet to be involved in their first upset. Comments R.D.C.: "Mr. Hands' findings suggest that many machines must be hanging on by the skin of their teeth even when being cornered at surprisingly low road speeds."