road and workshop
Page 42
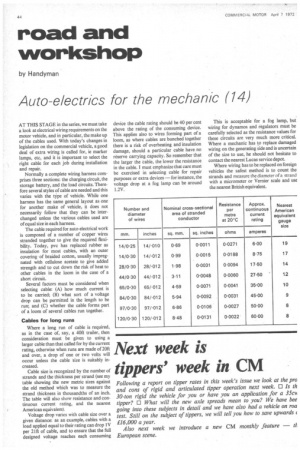
If you've noticed an error in this article please click here to report it so we can fix it.
by Handyman
Auto-electrics for the mechanic (14)
AT THIS STAGE in the series, we must take a look at electrical wiring requirements on the motor vehicle, and in particular, the make up of the cables used. With today's changes in legislation on the commercial vehicle, a good deal of extra wiring is called for, ie marker lamps, etc, and it is important to select the right cable for each job during installation and repair.
Normally a complete wiring harness comprises three sections: the charging circuit, the storage battery, and the load circuits. Therefore several styles of cable are needed and this varies with the tYpe of vehicle. While one harness has the same general layout as one for another make of vehicle, it does not necessarily follow that they can be interchanged unless the various cables used are of equal size in each harness.
The cable required for auto-electrical work is composed of a number of copper wires stranded together to give the required flexi bility. Today, pvc has replaced rubber as insulation for most cables, with an outer covering of braided cotton, usually impregnated with cellulose acetate to give added strength and to cut down the risk of heat to other cables in the loom in the case of a short circuit.
Several factors must be considered when selecting cable: (A) how much current is to be carried; (B) what sort of a voltage drop can be permitted in the length to be run; and (C) whether the cable forms part of a loom of several cables run together.
Cables for long runs Where a long run of cable is required, as in the case of, say, a 40ft trailer, then consideration must be given to using a larger cable than that called for by the current rating, otherwise when runs are made of 20ft and over, a drop of one or two volts will occur unless the cable size is suitably increased.
Cable size is recognized by the number of strands and the thickness per strand (see my table showing the new metric sizes against the old method which was to measure the strand thickness in thousandths of an inch. The table will also show resistance and continuous current rating, and the nearest American equivalent).
Voltage drop varies with cable size over a given distance: as an example, cables with a load applied equal to their rating can drop 1V per 21ft of cable, and to ensure that the full designed voltage reaches each consuming device the cable rating should be 40 per cent above the rating of the consuming device. This applies also to wires forming part of a loom, as where cables are bunched together there is a risk of overheating and insulation damage, should a particular cable have no reserve carrying capacity. So remember that the larger the Cable, the lower the resistance in the cable. I must emphasize that care must be exercised in selecting cable for repair purposes or extra devices for instance, the voltage drop at a fog lamp can be around 1.2V. This is acceptable for a fog lamp, but wiring for dynamos and regulators must be carefully selected as the resistance values for these circuits are very much more critical. Where a mechanic has to replace damaged wiring on the generating side and is uncertain of the size to use, he should not hesitate to contact the nearest Lucas service depot.
Where wiring has to be replaced on foreign vehicles the safest method is to count the strands and measure the diameter of a strand with a micrometer or Vernier scale and use the nearest British equivalent.