FLOATING ON AIR
Page 59
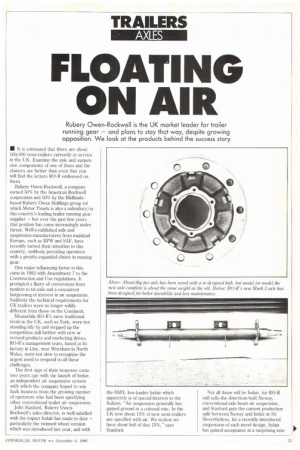
Page 60
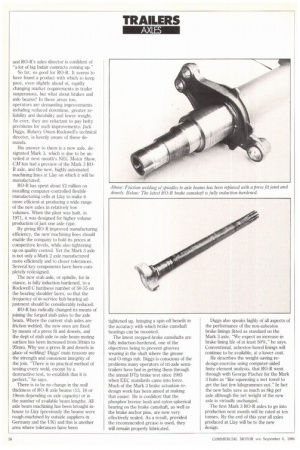
If you've noticed an error in this article please click here to report it so we can fix it.
Rubery Owen-Rockwell is the UK market leader for trailer running gear — and plans to stay that way, despite growing opposition. We look at the products behind the success story.
IN It is estimated that there are about 160,000 semi-trailers currently in service in the UK. Examine the axle and suspension components of one of them and the chances are better than even that you will find the letters RO-R embossed on them.
Rubery Owen-Rockwell, a company owned 50% by the American Rockwell corporation and 50% by the Midlandsbased Rubery Owen Holdings group (of which Motor Panels is also a subsidiary) is this country's leading trailer running gear supplier — but over the past few years that position has come increasingly under threat. Well-established axle and suspension manufacturers from mainland Europe, such as BPW and SAF, have recently turned their attention to this country, suddenly providing operators with a greatly-expanded choice in running gear.
One major influencing factor in this came in 1983 with Amendment 7 to the Construction and Use regulations. It prompted a flurry of conversions from tandem to tri-axle and a concurrent burgeoning of interest in air suspension. Suddenly the technical requirements for UK trailers were no longer wildly different from those on the Continent.
Meanwhile RO-R's more traditional rivals in the UK, such as York, were not standing idly by and stepped up the competition still further with new or revised products and marketing drives. RO-R's management team, based at its factory in Llay, near Wrexham in North Wales, were not slow to recognise the urgent need to respond to all these challenges.
The first sign of their response came two years ago with the launch of Indair, an independent air suspension system with which the company hoped to win back business from the growing number of operators who had been specifying other conventional trailer air suspension.
John Stanford, Rubery OwenRockwell's sales director, is well satisfied with the impact Indair has made to date — particularly the twinned wheel version which was introduced last year, and with the BMX, low-loader Indair which apparently is of special interest to the Italians. "Air suspension generally has gained ground at a colossal rate. In the UK now about 15% of new semi-trailers are specified with air. We reckon we have about half of that 15%," says Stanford. Not all those will be Indair, for RO-R still sells the American-built Neway, conventional axle beam air suspension, and Stanford puts the current production split between Neway and Indair at 50. Nevertheless, for a recently-introduced suspension of such novel design, lndair has gained acceptance at a surprising rate and RO-R's sales director is confident of "a lot of big Indair contracts coming up."
So far, so good for RO-R. It seems to have found a product with which to keep pace, even slightly ahead of, rapidly changing market requirements in trailer suspensions, but what about brakes and axle beams? In these areas too, operators are demanding improvements including reduced downtime, greater reliability and durability and lower weight. As ever, they are reluctant to pay hefty premiums for such improvements. Jack Diggs, Rubery Owen-Rockwell's technical director, is keenly aware of these demands.
His answer to them is a new axle, designated Mark 3, which is due to be unveiled at next month's NEC Motor Show. CM has had a preview of the Mark 3 ROR axle, and the new, highly-automated machining lines at Llay on which it will be manufactured.
RO-R has spent about ,e2 million on installing computer-controlled flexible manufacturing cells at Llay to make it more efficient at producing a wide range of the new axles in relatively low volumes. When the plant was built, in 1971, it was designed for higher volume production of just one axle type.
By giving RO-R improved manufacturing efficiency, the new machining lines should enable the company to hold its prices at competitive levels, while also tightening up on quality control. Yet the Mark 3 axle is not only a Mark 2 axle manufactured more efficiently and to closer tolerances. Several key components have been completely redesigned.
The new stub axle, or spindle, for instance, is fully induction-hardened, to a Rockwell C hardness number of 50-55 on the bearing shoulder faces, so that the frequency of in-service hub bearing adjustment should be considerably reduced.
RO-R has radically changed its means of joining the forged stub axles to the axle beam. Where the current stub axles are friction welded, the new ones are fixed by means of a press fit and dowels, and the dent of stub axle to axle beam mating surface has been increased from 30mm to 95mm. Why use a press fit and dowels in place of welding? Diggs' main reasons are the strength and consistent integrity of the join. "There is no practical method of testing every weld, except by a destructive test, to establish that it is perfect," he says.
There is to be no change in the wall thickness of RO-R axle beams (13, 16 or 19mm depending on axle capacity) or in the number of available beam lengths. All axle beam machining has been brought inhouse to Llay (previously the beams were rough-machined by outside suppliers in Germany and the UK) and this is another area where tolerances have been tightened up, bringing a spin-off benefit in the accuracy with which brake camshaft bearings can be mounted.
The latest stepped-brake camshafts are fully induction-hardened, one of the objectives being to prevent grooves wearing in the shaft where the grease seal 0-rings rub. Diggs is conscious of the problems many operators of tri-axle semitrailers have had in getting them through the annual DTp brake test since 1983 when EEC standards came into force. Much of the Mark 3 brake actuation redesign work has been aimed at making that easier. He is confident that the phosphor bronze bush and nylon spherical bearing on the brake camshaft, as well as the brake anchor pins, are now very effectively sealed. As a result, provided the recommended grease is used, they will remain properly lubricated. Diggs also speaks highly of all aspects of the performance of the non-asbestos brake linings fitted as standard on the Mark 3 axle. "We expect an increase in brake lining life of at least 50%," he says. Conventional, asbestos-based linings will continue to be available, at a lower cost.
He describes the weight-saving redesign exercise using computer-aided finite element analysis, that R0-R went through with George Fischer for the Mark 3 hubs as "like squeezing a wet towel to get the last few kilogrammes out." In fact the new hubs save as much as 8kg per axle although the net weight of the new axle is virtually unchanged.
The first Mark 3 RO-R axles to go into production next month will be rated at ten tonnes. By the end of this year all axles produced at Llay will be to the new design.