MORE ROOM ON TOP!
Page 51
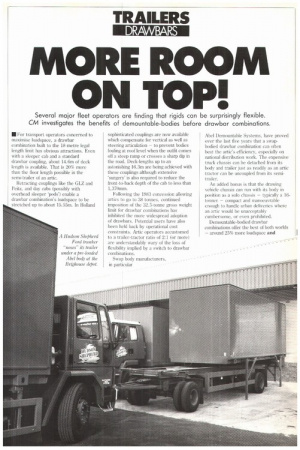
Page 52
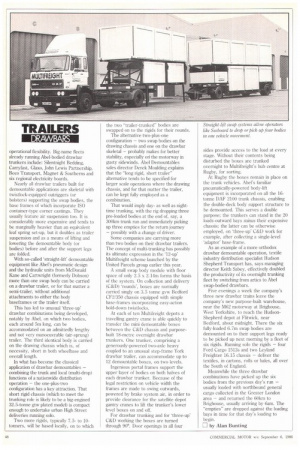
If you've noticed an error in this article please click here to report it so we can fix it.
Several major fleet operators are finding that rigids can be surprisingly flexible. CM investigates the benefits of demountable-bodies before drawbar combinations.
• For transport operators concerned to niaximise loadspace, a drawbar combination built to the 18-metre legal length limit has obvious attractions. Even with a sleeper cab and a standard drawbar coupling, about 14.6m of deck length is available. That is 20% more than the floor length possible in the semi-trailer of an artic.
Retracting couplings like the GLZ and Peitz, and day cabs (possibly with overhead sleeper 'pods') enable a drawbar combination's loadspace to be stretched up to about 15.55m. In Holland sophisticated couplings are now available which compensate for vertical as well as steering articulation — to prevent bodies fouling at roof level when the outfit comes off a steep ramp or crosses a sharp dip in the road. Deck-lengths up to an astonishing 16.3m are being achieved with these couplings although extensive 'surgery' is also required to reduce the front-to-back depth of the cab to less than 1,370mm.
Following the 1983 concession allowing artics to go to 38 tonnes, continued imposition of the 32.5-tonne gross weight limit for drawbar combinations has inhibited the more widespread adoption of drawbars. Potential users have also been held back by operational cost constraints. Artic operators accustomed to a trailer-tractor ratio of 2:1 (or more) are understandably wary of the loss of flexibility implied by a switch to drawbar combinations.
Swap body manufacturers, in particular Abel Demountable Systems, have proved over the last five years that a swapbodied drawbar combination can often beat the artic's efficiency, especially on national distribution work. The expensive truck chassis can be detached from its body and trailer just as readily as an artic tractor can be uncoupled from its semitrailer.
An added bonus is that the drawing vehicle chassis can run with its body in position as a solo chassis — typically a 16tonner — compact and manoeuvrable enough to handle urban deliveries where an artic would be unacceptably cumbersome, or even prohibited.
Demountable-bodied drawbar combinations offer the best of both worlds — around 25% more loadspace and
operational flexibility. Big-name fleets already running Abel-bodied drawbar trunkers include: Silentnight Bedding, Carryfast, Glaxo, John Lewis Partnership, Bees Transport, Magnet & Southenis and six regional electricity boards.
Nearly all drawbar trailers built for demountable applications are skeletal with twistlock-equipped outriggers (or bolsters) supporting the swap bodies, the base frames of which incorporate ISO container-type corner castings. They usually feature air suspension too. It is considerably more expensive and tends to be marginally heavier than an equivalent leaf spring set-up, but it doubles as trailer suspension and as a means of lifting and lowering the demountable body (or bodies) before and after the support legs are folded.
With so-called 'straight-lift' demountable equipment like Abel's pneumatic design and the hydraulic units from McDonald Kane and Cartwright (formerly Dobson) more than one swap body can be carried on a drawbar trailer, or for that matter a semi-trailer, without additional attachments to either the body baseframes or the trailer itself.
This has led to unusual 'three-up' drawbar combinations being developed, notably by Abel, on which two bodies, each around 5m long, can be accommodated on an admittedly lengthy and not very manoeuvrable (air-sprung) trailer. The third identical body is carried on the drawing chassis which is, of necessity, short in both wheelbase and overall length.
In what has become the classical application of drawbar demountables — combining the trunk and local (multi-drop) functions of a nationwide distribution operation — the one-plus-two configuration has a key attraction. That short rigid chassis (which to meet the trunking role is likely to be a big-engined 32.5-tonne gtw plated model) is compact enough to undertake urban High Street deliveries running solo.
Two more rigids, typically 7.5to 10tonners, will be based locally, on to which
the two "trailer-trunkedbodies are swapped on to the rigids for their rounds.
The alternative two-plus-one configuration — two swap bodies on the drawing chassis and one on the drawbar skeletal — probably makes for better stability, especially on the motorway in gusty sidewinds. Abel Demountables sales director Derek Moulding explains that the "long rigid, short trailer" alternative tends to he specified for larger scale operations where the drawing chassis, and for that matter the trailer, can be kept fully employed as a combination.
That would imply dayas well as nighttime trunking, with the rig dropping three pre-loaded bodies at the end of, say, a 300km trunk run and immediately picking up three empties for the return journey — possibly with a change of driver.
Some companies are carrying more than two bodies on their drawbar trailers. The concept of multi-trunking has possibly its ultimate expression in the '12-up' Multifreight scheme launched by the United Parcels group earlier this year.
A small swap body module with floor space of only 2.5 x 2,14m forms the basis of the system. On collection and delivery (C&D) 'rounds', boxes are normally carried singly on 3.5 tonne gvw Bedford CF2/350 chassis equipped with simple base-frames incorporating easy-action hold-down twistlocks.
At each of ten Multifreight depots a travelling gantry crane is able quickly to transfer the mini demountable boxes between the C&D chassis and purposebuilt 18-metre overnight drawbar trunkers. One trunker, comprising a generously-powered two-axle heavy coupled to an unusual step-frame York drawbar trailer, can accommodate up to 12 demountable boxes, on two levels.
Ingenious portal frames support the upper layer of bodies on both halves of each drawbar trunker. Because of the legal restriction on vehicle width the frames are made to swing outwards, powered by brake system air, in order to provide clearance for the satellite depot gantry cranes to lift the trunker's lower level boxes on and off.
For drawbar trunking and for 'three-up' C&D working the boxes are turned through 90°. Door openings in all four sides provide access to the load at every stage. Without their contents being disturbed the boxes are trunked overnight to Multifreight's hub centre at Rugby, for sorting.
At Rugby the boxes remain in place on the trunk vehicles. Abel's familiar pneumatically-powered body-lift equipment is incorporated on all the 16tonne DAF 2100 trunk chassis, enabling the double-deck body support structure to be demounted. This serves a double purpose; the trunkers can stand in the 20 loads-outward bays minus their expensive chassis; the latter can be otherwise employed, on 'three-up' C&D work for example, after collecting a single-level 'adaptor' base-frame.
As an example of a more orthodox drawbar demountable operation, textile industry distribution specialist Hudson Shepherd Transport has, says managing director Keith Sabey, effectively doubled the productivity of its overnight trunking fleet by switching from artics to Abel swap-bodied drawbars.
Five evenings a week the company's three new drawbar trains leave the company's new purpose-built warehouse, near the M62 motorway at Brighouse, West Yorkshire, to reach the HudsonShepherd depot at Flitwick, near Bedford, about midnight. There the six fully-loaded 6.7m swap bodies are demounted on to their support legs ready to be picked up next morning by a fleet of six rigids. Running solo the rigids — four Ford Cargo 1513s and two Leyland Freighter 16.15 chassis — deliver the textiles, in cartons, rolls or bales, all over the South of England.
Meanwhile the three drawbar combinations have picked up the six bodies from the previous day's run — usually loaded with northbound general cargo collected in the Greater London area — and returned the 60km to Brighouse, usually arriving by 6am. The "empties" are dropped against the loading bays in time for that day's loading to begin.
El by Alan Bunting