About Plantation Rubber.
Page 16
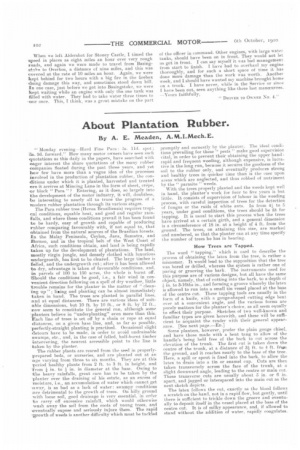
Page 17
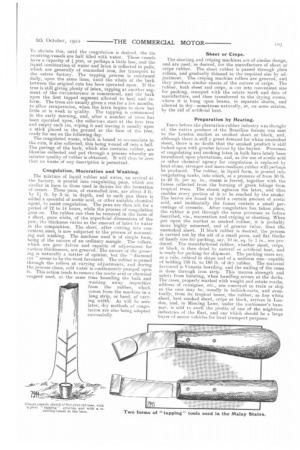
If you've noticed an error in this article please click here to report it so we can fix it.
By A. E. Meaden,
" Monday evening—Hard Fine _Para s. lid. st ; Zs. 9d. forward." How many motor owners have seen such quotations as this daily in the papers, have searched with eager interest the share quotations of the many rubber companies floated during the past three years, and yet bow few have more than a vague idea of the processes involved in the production of plantation rubber, the conditions under which it is planted, harvested and treated ere it arrives at Mincing Lane in the form of sheet, crepe, or block " Para " ? Entering, as it does, so largely into the development of the motor industry, it will, doubtless, be interesting to nearly all to trace the progress of a ituodern rubber plantation through its various stages. The Para rubber tree (Herea T1raziliensis) requires tropical conditions, equable heat, and good and regular rainfalls, and where these conditions prevail it has been found to be hardy, easy of growth and capable of producing rubber comparing favourably with, if not equal to, that obtained from the natural sources of the Brazilian forests. In the Malay Peninsula, Ceylon, Java, Sumatra, and Borneo, and in the tropical belt of the West Coast of Africa, such conditions obtain, and land is being rapidly taken up for the development of plantations. The land, mostly virgin jungle, and densely clothed with luxurious undergrowth, has first to be cleared. The large timber is felled, and the undergrowth cut ; after it has been allowed to dry, advantage is taken of favourable conditions. and. in parcels of 100 to 150 acres, the whole is burnt off. Should the conditions be good, i.e., a fair wind in convenient direction following on a spell of dry weather, little trouble remains for the planter in the matter of "cleaning up " ; lilting and planting can be almost immediately taken in hand. The trees are planted in parallel lines. and at equal distances. There are various ideas of suitable dimensions, but 10 ft. by 10 ft., or 8 ft. by 12 ft., now seem to constitute the general run, although some 'planters believe in "underplanting" even more than this. Each line of trees is set off by a chain or rope at equitl distances, on a given base line, and, as far as possible, -perfectly-straight planting is practised. Occasional slight detours have to be made, in order to avoid undrainahle swamps, etc., and, in the case of felled, half-burnt timber intervening, the nearest accessible point to the line is taken by the planter.
The rubber plants are reared from the seed in properlyprepared beds, or nurseries, and are planted out at an age varying from three to six months. They are at this period healthy plants from 2 ft. to 3 ft. in height, and
'from t in. to in. in diameter at the 'base. Owing to the heavy rainfalls, great care has to be taken by the planter over the draining of his estate, as an excess of moisture, i.e., an accumulation of water which cannot get • saway, is as bad as a lack of water: swampy conditions rare detrimental to the growth of trees. On hilly ground 'with loose soil, good drainage is very essential, in order to carry off excessive rainfall, which would otherwise Nvash away the soil from the roots of young trees, and .eventually expose and seriously injure them. The rapid -growth of weeds is another difficulty which must be tackled promptly and earnestly by the planter. The ideal conditions prevailing for these " pests " make good supervision vital, in order to prevent their obtaining the upper hand : rapid and frequent weeding, although expensive, is lucrative in the long run, because it secures the goodness of the soil to the rubber only, and eventually produces strong and healthy trees in quicker time than is the ease upon areas which are neglected, and thus robbed of nutriment by the " parasite " weeds.
With the trees properly planted and the weeds kept well in hand, the planter's work for four to five years is but little. It consists of supervision of labour in the weeding process, with careful inspection of trees for the detection of fungus or the raids of white ants. In from 44 to 5 years, under good conditions, the trees should be fit for tapping. It is usual to start. this process when the trees have arrived at a certain girth, and a general dimension is a circumference of 18 in. at a height of 4 ft. from the ground. The trees, on attaining this size, are marked and numbered, so that the planter can at any time specify the number of trees he has in bearing.
How Trees are Tapped.
The word " tapping," which is used to describe the process of obtaining the latex from the tree, is rather a misnomer. It would lead to the supposition that the tree was bored or drilled, whereas the system is rather one of paring or grooving the bark. The instruments used for this purpose are of various designs, but all have the same object, namely, that of cutting into the bark, to a depth of h in. to 3-16ths in., and forming a groove whereby the latex is allowed to run into a small tin vessel placed at the base of the centre cut. These tapping tools are usually in the form of a knife, with a gouge-shaped cutting edge bent over at a convenient angle, and the various forms are purely matters for the planter's choice, as all seem equally to effect their purpose. Sketches of two well-known and familiar types are given herewith, and these will be sufficient to acquaint the reader with their general appearance. [See next page.—ED.]
Some planters, however, prefer the plain gouge chisel, and have these made with a bent tang to allow of the handle's being held free of the bark to cut across the elevation of the trunk. The first cut is taken down the centre of the trunk, at a distance of ai ft. to 4 ft. fesial the ground, and it reaches nearly to the base of the tree. Here, a spill or spout is fixed into the bark, to allow the latex to drain into a tin or enamel cup. Cuts are then taken transversely across the face of the trunk, at a slight downward angle, leading to the centre or main cut. These transverse cuts are usually about 5 in. or 6 in. apart, and jagged or interspaced into the main cut as the next sketch depicts. The latex follows the cut, exactly as the blood follows a scratch on the hand, not in a rapid flow, but gently, until there is sufficient to trickle down the groove and eventually to deposit itself in the vessel placed at the base of the centre cut. It is of milky appearance, and, if allowed to stand without the addition of water, rapidly coagulates.
To obviate this, until the coagulation is desired, the tin receiving-vessels are half filled with water. These vessels have a capacity of pint, or perhaps a little less, and the liquid combination of water and latex is collected in pails, which are generally of enamelled iron, for transport to the estate factory. The tapping process is continued daily, upon the same lines, until the whole of the bark between the original cuts has been operated upon. If the tree is still giving plenty of latex„ tapping at another segment of the circumference is Commenced, and the bark upon the first tapped segment allowed to heal and reform. The trees are usually given a rest for a few months, to allow recuperation, when the latex begins to show but little or is weak in quality. The tapping is commenced in the early morning, and, after a number of trees has been operated upon, the collectors start at the first tree and empty each tin, wiping it and leaving it usually upon a stick placed in the ground at the base of the tree, ready for use on the following day.
The coagulated waste, which is bound to accumulate in the cuts, is also collected, this being wound off into a ball. The parings of the bark, which also contains rubber, are likewise collected and put through a process whereby an inferior quality of rubber is obtained. It will thus be seen that no waste of any description is permitted.
Coagulation, Maceration and Washing.
The mixture of liquid rubber and water, on arrival at the factory, is poured into coagulating pans, which are similar in form to those used in dairies for the formation of cream. These pans, of enamelled iron, are about 3 ft. by 1"i ft. by 3 in. in depth, and to each pan there is added a spoonful of acetic acid, or other suitable chemical agent, to assist coagulation. The pans are then left for a period of 12 to 14 hours, while the process of coagulation goes on. The rubber can then be removed in the form of a sheet, pure white, of the superficial dimensions of the pan ; the thickness varies as the amount of latex to water in the composition. The sheet, after cutting into convenient sizes, is now subjected to the process of macerating and washing. The machine used is of simple form, being of the nature of an ordinary mangle. The rollers, which are gear driven and capable of adjustment for various thicknesses, are grooved. The nature of the grooving is naturally a matter of opinion, but the " diamond cut "seems to be the most favoured. The rubber is passed through the rollers at varying adjustments, and during the process clean, cold water is continuously pumped upon it. This action tends to remove the acetic acid or chemical reagent used, at the same time kneading the bulk and washing away impurities from the rubber, which comes from the machine in a long strip, or band, of varying width. As will be seen later, dry methods of coagulation are also being adopted successfully_
Sheet or Crepe.
The sheeting and creping machines are of similar design, and are used, as desired, for the manufacture of sheet or crepe rubber. The sheet rubber is passed through plain rollers, and gradually thinned to the required size by adjustment. The creping machine rollers are grooved, and they produce similar sheets of the nature of crepe. The rubber, both sheet and crepe, is cut into convenient size for packing, stamped with the estate mark and date of manufacture, and then transferred to the drying rooms; where it is hung upon beams, in separate sheets, and allowed to dry—sometimes naturally, or, on some estates, by the aid of artificial heat.
Preparation by Heating.
Years before the plantation-rubber industry was thought of, the native produce of the Brazilian forests was sent to the London market as smoked sheet or block, and, although there is still a great demand for white unsmoked sheet, there is no doubt that the smoked product is still looked upon with greater favour by the buyers. Processes of coagulating and smoking latex in bulk have lately been introduced upon plantations, and, as the use of acetic acid or other chemical agency for coagulation is replaced by heat, alone, stronger and more-resilient rubber will perhaps be produced. The rubber, in liquid form, is poured into coagulating tanks, into which, at a pressure of from 30 lb. to 40 lb. per sq. in., steam is forced, together with the fumes collected front the burning of green foliage from tropical trees. The steam agitates the latex, and thus enables every portion of it to be reached by the smoke. The leaves are found to yield a certain amount of acetic acid, and incidentally the fumes contain a small percentage of creosote. After coagulation has taken place, the rubber is put through the same processes as before described, viz., maceration and creping or sheeting. When put upon the market as smoked rubber, it is probably more highly esteemed, and of greater value, than the unsmoked sheet. If block rubber is desired, the process is carried out by the aid of a small press, and flat blocks of handy size for packing, say, 10 in. sq. by 1 in., are produced. The manufactured rubber, whether sheet, crepe, or block, is then dried by natural or artificial heat, and is ready for packing fur shipment. The packing cases are, as a rule, cubical in shape and of a uniform size—capable of holding 150 lb. to 180 lb. of dry rubber. The material favoured is Venesta boarding, and the nailing of the cases is done through iron strip. This insures strength and safety from bursting, when handling occurs at the docks. The eases, properly marked with weight and estate marks, address of consignee, etc., are convoyed to train or ship as the case may be, usually in bullock-carts, and eventually-, from its tropical home, the rubber, as fine white sheet, best smoked sheet, crepe or block, arrives in London, and, in Mincing Lane, under the auctioneer's hammer, is sold to swell the profits of one of the mightiest industries ef the East, and one which should be a large buyer of 'memr vehicles for local transport purposes.