Operators' Co-operation Before Sall
Page 52
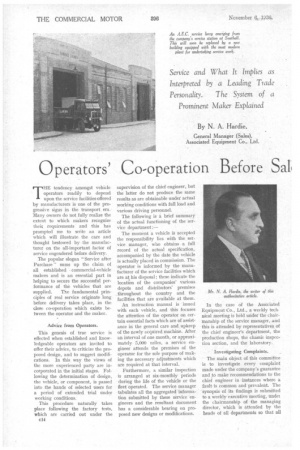
Page 53
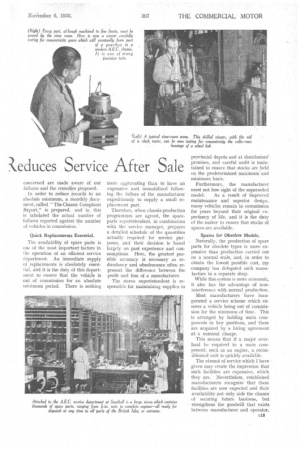
If you've noticed an error in this article please click here to report it so we can fix it.
..educes Service After Sale
• By N. A. Hardie,
THE tendency amongst vehicle operators readily to depend upon the service facilities offered by manufacturers is one of the progressive signs in the transport era. Many owners do not fully realize the extent to which makers recognize their requirements and this has prompted me to write an article which will illustrate the care and thought bestowed by the manufacturer on the all-important factor of service engendered before delivery.
The popular slogan "Service after Purchase " sums up the claim of all established commercial-vehicle makers and is an essential part in helping to secure the successful performance of the vehicles that are
supplied. The fundamental principles of real service originate long before delivery takes place, in the close co-operation which exists between the operator and the maker.
Advice from Operators.
This genesis of true service is effected when established and knowledgeable operators are invited to offer their advice, to criticize the proposed design, and to suggest modifications. In this way the views of the more experienced party are incorporated in the initial stages. Following the determination of design, the vehicle, or component, is passed into the hands of selected users for a period of extended trial under working conditions.
This procedure naturally takes place following the factory tests, which are carried out under the c14 supervision of the chief engineer, but the latter do not produce the same results as are obtainable under actual working conditions with full load and various driving personnel.
The following is a brief summary of the actual functioning of the service department:— The moment a vehicle is accepted the responsibility lies with the service manager, who obtains a full record of the actual specification, accompanied by the date the vehicle is actually placed in commission. The operator is informed by the manufacturer of the service facilities which are at his disposal; these indicate the location of the companies' various depots and distributors' premises throughout the country and the facilities that are available at them.
An instruction manual is issued with each vehicle, and this focuses the attention of the operator on certain essential facts which are of assistanc,e in the general care and upkeep of the newly acquired machine. After an interval of one month, or approximately 5,000 miles, a service engineer attends the premises of the operator for the sole purpose of making the necessary adjustments which are required at that interval.
Furthermore, a similar inspection is arranged at six-monthly periods during the life of the vehicle or the fleet operated. The service manager tabulates all the aggregated information submitted by these service engineers and the resultant document has a considerable bearing on proposed new designs or modifications. In the case of the Associated Equipment Co., Ltd., a weekly technical meeting is held under the chairmanship of the service manager,and this is attended by representatives of the chief engineer's department, the production shops, the chassis inspection section, and the laboratory.
Investigating Complaints.
The main object of this committee is to investigate every complaint made under the company's guarantee and ,to make recommendations to the chief engineer in instances where a fault is common and prevalent. The synopsis of its findings is submitted to a weekly executive meeting, under the chairmanship of the managing director, which is attended by the heads of all departments so that all
concerned are made aware of our failures and the remedieS proposed.
In order to reduce record to an absolute minimum, a monthly docunient, called " The Chassis Complaint Report," is prepared, and in this i5 tabulated the actual number of failures reported against the number of vehicles in commission.
Quick Replacements Essential.
The availability of spare parts is one of the most important factors in he operation of an efficient Service department. An immediate supply of replacements is absolutely essential, and it is the duty of this department to ensure that the vehicle is out of commission for an absolute minimum period. There is nothing more aggravating than to have an expensive unit immobilized following the failure of the manufacturer expeditiously to supply a small replacement part.
Therefore, when chassis-production programmes are agreed, the spareparts superintendent, in combination with the service manager, prepares a detailed schedule of the quantities actually required • for service purposes, and their decision is based largely on past experience and consumptions. Here, the, greatest possible accuracy is necessary as redundancy and obsolescence often represent the difference between the profit and loss of a manufacturer.
The stores superintendent is responsible for maintaining supplies in provincial depots and at distributors' premises, and careful audit is maintained to ensure that stocks are held on the predetermined maximum and minimum basis.
Furthermore, the manufacturer must not lose sight of the superseded
model. As a result of improVed maintenance and superior design, many vehicles remain in commission for years beyond their original expectancy of life, and it is the duty of the maker to ensure that stocks of spares are available.
Spares for Crbsofete Models.
Naturally, the production of spare parts for obsolete types is more expensive than production carried out on a normal scale, and, in order to obtain the lowest possible cost, my company has delegated such manufacture to a separate shop.
While this system is more ecOnoinic, it also has the advantage of noninterference with normal production.
Most manufacturers have inaugurated a service scheme which ensures a vehicle being out of commission for the minimum of time. This is arranged by holding main components in key positions, and these are acquired by a hiring agreement at a nominal charge.
This means that if a major overhaul be required to a main component, such as an engine, a reconditioned unit is quickly available.
The résumé of service which I have given may create the impression that such facilities are expensive, which they are. Nevertheless, established manufacturers recognize that these facilities are now expected and their availability not only aids the chance of securing future business, but strengthens the goodwill that exists between manufacturer and operator.