Giving Them the Works
Page 17
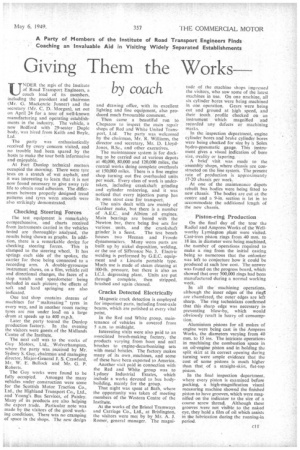
If you've noticed an error in this article please click here to report it so we can fix it.
by coach
UNDER the &gis of the Institute of Road Transport Engineers, a coach load of its members, including the president and chairman (Mr. G. Mackenzie Junner) and the secretary (Mr. C. D. Morgan), set out on April 24 for a tour of well-known manufacturing and operating establishments in the industry. The vehicle, a new Bedford with 29-seater Duple body, was hired from Keith and Boyle,
The party was enthusiastically received by every concern visited, and no trouble had been spared by the hosts to make the tour both informative and enjoyable.
At Fort Dunlop technical matters occupied the morning. There were tyre tests on a stretch of wet asphalt, and it was interesting to learn that it is not now found necessary to give away tyie life to obtain road adhesion. The differences between properly designed tread patterns and tyres worn smooth were also strikingly demonstrated.
Checking Steering Forces Fite test equipment is remarkably comprehensive, and charts received from instruments carried in the vehicles tested are thoroughly. analysed, the results being shown as graphs. In addition, there is a remarkable device for checking steering forces. This is clamped to the steering wheel. It has springs each side of the spokes, the • carrier for these being connected to a recording arm. A double-gyroscope instrument shows, on a film, vehicle roll and directional changes, the faces of a • stop watch and speedometer being included in each picture; the effects of soft, and hard springing are also indicated. .
One test shop contains dozens of machines for " maltreating " tyres in every way, and in another room racing tyres are run under load on a large . drum at speeds up to 400 m.p.h.
Later the party toured the Dunlop production factory. In the evening the visitors were guests of the Midlands Centre of the Institute.
The next call wis to the works of Guy Motors, Ltd., Wolverhampton, where the party was received by Mr. Sydney S. Guy, chairman and managing director, Major-General J. S. Crawford, Mr. W. E. Bullock and Mr. G. P. Roberts.
The Guy works were found to be fully occupied. Amongst the many vehicles under construction were some for the Scottish Motor. Traction Co., Ltd., the Highland Transport Co., Ltd., and Young's Bus Services, of Paisley. Many of its products are also helping the export trade. Particular note was • made by the visitors of the good working conditions. There was no cramping of space in the shops. The new design and drawing office, with its excellent lighting and fine equipment, also produced much favourable comment.
Then came a beautiful run to Chepstow to inspect the main repair shops of Red and White United Transport, Ltd. The party was welcomed by the chairman, Mr. R. Williams, the director and secretary, Mr. D. LloydJones, B.Sc., and other executives.
The maintenance system is for docking to be carried out at various depots at 40,000, 80,000 and 120,000 miles, the central works doing complete overhauls at 150,000 miles. There is a fine engine shop turning out five overhauled units per week. Every class of work is undertaken, including crankshaft grinding and cylinder resleeving, and it was noticed that every injection pump has its own stout case for transport.
The units dealt with are mainly of Gardner make, but there is a number of A.E.C. and Albion oil engines. Main bearings are bored with the Newton bar, there being five sets for various units, and the crankshaft grinder, is a Seest. The test bench houses two Heenan and Fronde dynamometers. Many worn parts are built up by nickel deposition, welding, or the use of Sifbronze No. 3. Electric welding is performed by G.E.C. equipment and a Lincoln portable type. Much use is made of steam cleaning at 100-1b. pressure, but there is also an I.C.I. degreasing plant. Units are put through complete, then stripped, brushed and again cleaned.
Cracks Detected Electrically • Magnetic crack detection is employed for important parts, including front-axle beams, which are polished at every vital point.
In the Red and White group, maintenance of vehicles is covered from 5 a.m. to midnight.
Interesting visits were also paid to an associated brush-making factory, the products varying from boot and nail brushes to engine-decarbonizing sets with metal bristles: The factory makes many of its own , machines, and some of these have been exported to America.
Another visit paid in connection with the Red and White group was to Lydney Industrial Estates, which include a works devoted to bus bodybuilding, mainly for the group.
That night was spent at Bath, where the opportunity was taken of meeting members of the Western Centre of the Institute.
At the works of the Bristol Tramways and Carriage 'Co., Ltd., at Brislington, the visitors were met by by Mr. A. J. Romer, general manager. The magni
tude of the machine shops impressed the visitors, who saw some of the latest machines in use. On one muchine, all six cylinder bores were being machined in one operation. Gears were being cut and ground at high speed, and their tooth profile checked on an instrument which magnified and recorded any defects or machining marks.
In the inspection department, engine cylinder bores and brake cylinder bores were being checked for size by a Solex hydro-p,neumatic gauge. This instrument gives a visual indication of bore size, ovality or tapering.
A brief visit was made to the assembly shops, where chassis are constructed on the line system. The present rate of production is approximately 17-20 chassis per week.
• At one of the maintenance depots rebuilt bus bodies were being fitted to new chassis, The bodies are cut at the centre and a 9-in. section is let in to accommodate the additional length of the new chassis.
Piston-ring Production
On the final day of the tour the Radial and Ampress Works of the Wellworthy Lymington plant were visited. Cast-iron piston rings from 40 mm. to 18 ins, in diameter were being machined, the number of operations required to make a ring from the initial casting being so numerous that the onlooker was left to conjecture how it could be produced at such low cost. The answer was found on the progress board, which showed that over 300,000 rings had been manufactured during a normal working week.
In all the 'machining operations, although the inner edges of the ring are chamfered, the outer edges are left sharp. The ring technicians confirmed that this sharp edge was necessary in preventing blow-by, which would obviously result in heavy oil consumption.
Aluminium pistons for all makes of engine were being cast in the Ampress Works, the diameters varying from 40 mm. to 15 ins. The intricate operations in machining the combustion space in an oil-engine piston and in holding the split skirt at its correct opening during turning were ample evidence that the cost of some pistons is much higher than that of a straight-skirt, flat-top piston.
In the final inspection department, where every piston is examined before packing, a high-magnification visual measuring machine showed the finished piston to have grooves, which were magnified on the indicator to the size of a coarse screw thread. Although these grooves were not visible to the naked eye, they hold a film of oil which assists in the lubrication during the running-in period.