ROADLITE: TECHNICAL BREAKDOWN • CM recently gained an exclusive preview
Page 21
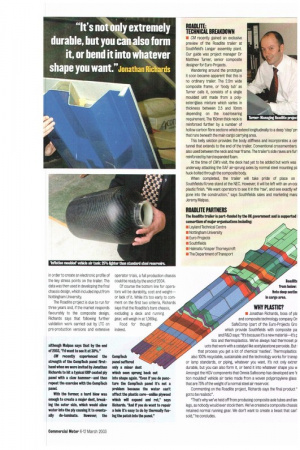
If you've noticed an error in this article please click here to report it so we can fix it.
of the Roadlite trailer at Southfield's Langer assembly plant. Our guide was project manager Dr Matthew Turner, senior composite designer for Euro-Projects.
Wandering around the prototype it soon became apparent that this is no ordinary trailer. The 2.5m wide composite frame, or 'body tub' as Turner calls it, consists of a single moulded unit made from a polyesterigiass mixture which varies in thickness between 2.5 and 10rom depending on the load-bearing requirement. The 150mm thick neck is reinforced further by a number of hollow carbon fibre sections which extend longitudinally to a deep 'step' pn that runs beneath the main cargo carrying area.
This belly section provides the body stiffness and incorporates a cer tunnel that extends to the end of the trailer. Conventional crossmembers also used between the neck and rear frame. The trailer's side raves are furl reinforced by hard expanded foam.
At the time of CM'S visit, the deck had yet to be added but work was underway attaching the SAF air-sprung axles by normal steel mounting ph huck-bolted through the composite body.
When completed, the trailer will take pride of place on Southfields/Krone stand at the NEC. However, it will be left with an un-cm plastic finish, "We want operators to see it in the 'raw', and see exactly wt gone into the construction," says Southfields sales and marketing mem' Jeremy Malpas.
ROADLITE PARTNERS
The Roadlite trailer is part-funded by the UK government and is supported I consortium of major organisations Including • Leyland Technical Centre • Nottingham University • Euro-Projects • Southfields • Halmatic/Vosper Thorneycroft • The Department of Transport Roadlite from below: Note deep sectioi in cargo area.
WHY PLASTIC?
• Jonathan Richards, boss of pla and composite technology company Or SafeComp (part of the Euro-Projects Gro which provide Southfields with composite pa and R&D says: "it's because it's a new material—it's tics and thermoplastics. We've always had thermoset pi ucts that work with a catalyst like acetylacetone peroxide. But that process you get a lot of chemical 'nestles'. Thermoplastics also 100% recyclable, sustainable and the technology works for transp or lamp standards, or piping, whatever you want. It's not only extrer durable, but you can also form it, or bend it into whatever shape you w Amongst the HGV components that Omnia Safecomp has developed are `ir tion moulded' vehicle air tanks made from a woven polypropylene glass that are 75% of the weight of a normal steel air reservoir.
Commenting on the Roadlite project, Richards says the final product '' got to be realistic".
"That's why we've held off from producing composite axle tubes and Ian legs, as nobody would ever stock them. We've created a composite chassis retained normal running gear. We don't want to create a beast that can'' sold," he concludes.