PERFECTING THE PASSENGER-VEHICLE BODY.
Page 69
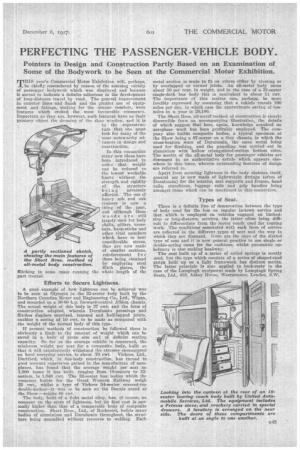
Page 70
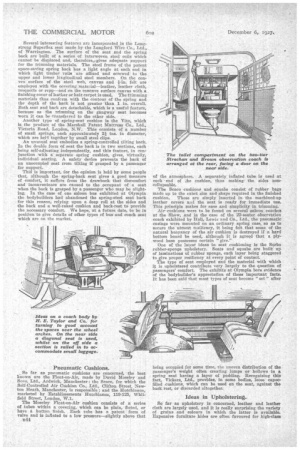
Page 71
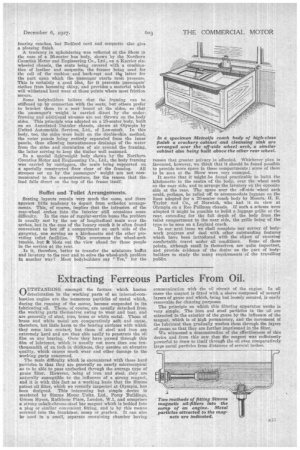
If you've noticed an error in this article please click here to report it so we can fix it.
Pointers in Design and Construction Partly Based on an Examination of. Some of the Bodywork to be Seen at the Commercial Motor Exhibition.
THIS year's Commercial Motor Exhibition will, perhaps, 'be chiefly remembered by reason of the amazing variety of passenger bodywcrk which was displayed and because it served to indicate a definite milestone in the development of long-distance travel by road. The general improvement in exterior lines and finish and the greater use of equipment and fittings, making for the utmost comfort,, were features which evoked the most favourable comments. Important as they an, however, such features have as their primary object the dressing of the shop window, and it is to the superstructure that one must look for many of the most noteworthy advances in design and construction.
In this connection many new ideas have been introduced in order that weight can be reduced to the lowest workable limits without the strength and rigidity of the structure being adversely affected. The use of heavy ash and oak timbers is now a thing of the past, and although these woods are still largely used for body shells, pillars, crossbars, hoop-sticks and other vital members which have to bear considerable stress, they are now made of smaller sections, reinforcement f o r them being obtained by employing steel flitch plates, the flitching in some cases running the whole length of the part treated. A partly sectioned sketch, showing the math features of the Short Bros. method of all-metal body construction.
Efforts to Secure Lightness.
A good example of how lightness can be achieved was to be seen at Olympia in the 32-seater body built by the 'Northern Counties Motor and Engineering Co., Ltd., Wigan, and mounted on a 30-60 h.p. forward-control Albion chassis. The actual weight of this body is 27 cwt. and the form of construction adopted, wherein Duralumin pressings and flitches disphee mortised, tenoned and half-lapped joints, enables a saving of 10 cwt. to be made as compared with the weight of the normal body of this type.
If present methods of construction be followed there is obviously a limit to the amount of weight which can be saved in a body of given size and of definite seating capacity. So far as the average vehicle is concerned, the minimum weight per seat for a composite body, built so that it will satisfactorily withstand the stresses encountered 011 hard everyday service, is about .70 cwt, 'Vickers, Ltd., Dartford, which, in bus-body construction, has turned to good account experience gained in the manufacture of aeroplanes, has found that the• average weight per seat on 1,000 buses it has built, ranging from 18-seaters to 32seaters, is 1.040 cwt. The 32-seater bus bodies which the company builds for the Great Western Railway weigh 33 cwt., whilst a type of Vickers 54-seater covered-top double-decker—it was to be seen on the Dennis stand at the Show—weighs 48 cwt.
The body, built of a light metal alloy, has, of course, no compeer on the score of lightness, but its first cost is normally higher than that of a comparable body of composite construction. Short Bros., Ltd., of Rochester, builds many bodies of aluminium and Duralumin throughout, the structure being assembled without recourse to welding. Each metal section is made to fit on others either by riveting or by overlapped or turned joints. An all-metal body saves about 80 per cent. in weight, and in the ease of a 22-seater single-deck bus body this is equivalent to about 11 cwt. The importance of this matter can, perhaps, be more forcibly expressed by assuming that a vehicle travels 100 miles per day, in which case the approximate saying of tonmiles in a year is 20,100.
The Short Bros. all-metal method of construction is clearly discernible from an accompanying illustration, the details of which suggest that here, again, knowledge acquired on aeroplane work has been profitably employed. The company also builds composite bodies, a typical specimen at the Show being a 67-seater on a Guy chassis, in which the cross-bearers were of Duralumin, the same metal being used for flitching, and the panelling was carried out in aluminium with hollow triangulated-section bottom sides. The merits of the all-metal body for passenger vehicles are discussed in an authoritative article which appears elsewhere in this issue, wherein outstanding features of design are referred to.
Apart from securing lightness in the -body skeleton itself, general use is now made of lightweight fittings (often of Duralumin) for the interior, seat supports and frames, hand rails, stanchions, luggage rails and grip handles being amongst those which can be mentioned in this connection.
Types of Seat.
There is a definite line of demarcation between the type of body used for the bus on regular in-town service and that which is employed on vehicles engaged on limitedstop or long-distance services, the latter often being difficult to differentiate from the motor coach used for touring work. The conditions associated with each form of service are reflected in the different types of seat and the way in which they are disposed. Gone are the days of the slatted type of seat and it is now general practice to use single or double-spring cases for the cushions, whilst pneumatic upholstery is also making headway.
The mat built up of a series of coiled springs is mostly used, but the type which consists of a series of shaped-steel strips built up on a light framework has distinct merits. The latter principle is also applied to back-rests in the case of the Lamplugh equipment made by Lamplugh Spring Seats, Ltd., 419, Abbey House, Westminster, London, S.W. Several interesting fee tureG are incorporated in the Longstrong Superflex ;ieat made by the Longford Wire Co., Ltd., of Warrington. The surface of the seat and the spring back are built of a series of interwoven steel coils which cannot be displaced and, therefore,, gives adequate support for the trimming materials. The steel frame of the patent space-saving spring back has a light angle at each end in which light timber mile are affixed and screwed to the upper and lower lcng,itudinal steel members. On the convex surface of the steel web, canvas and 1-in. felt are employee. with the covering material—leather, leather cloth, moquette or repp—and on the concave surface canvas with a finishing cover of leather or hair carpet is used. The trimming materials thus conform( with the contour of the spring and the depth of the back is not greater than 1 in. overall. Both seat and back are detachable, which is a useful feature, because as the trimming on the gangway seat becomes worn it can be transferred to the other side.
Another typo of spring-seat cushion is the Vito, which is the product of the Marshall Patent Mattress Co., Ltd., Victoria Road, Loudon, N.W. This consists of a number of small springs, each ,approximately 21 ins, in diameter, which are hell together by small steel clips.
An unusual seat embodies a spring-controlled tilting back. In the double form of seat the back is in two sectioxis, each being self-adjusting independently, and this feature, in conjunction with a separate spring cushion, gives, virtually, individual seating. A safety device prevents the back of an unoccupied seat nom tilting if grasped by a passenger for support.
Thi4 is important, for the opinion is held by some people that although the spring-back seat gives a good measure of comfort, it suffers from the drawback that discomfort and inconvenience are caused to the occupant of n seat when the back is grasped by a passenger who may be alighting. In the case of one saloon bus exhibited at Olympia the bodybuilders had abandoned the spring-steel seat back for this reason, relying upon a deep roll at the sides and the back and a well-raked cushion and back-rest to provide the necessary comfort. We hope, at a future date, to be in position to give details of other types cf bus and coach seat which are on the market.
Pneumatic Cushions.
So far as pneumatic cushions are concerned, the best known are the Float-on-Air, made by David Moseley and Sons, Ltd., Ardwick, Manchester ; the Scaco, for which the Self-Controlled Air Cushion Co., Ltd., Clifton Street, Newton Heath, Manchester, is responsible ; and the Hutchinson, marketed by Establissements Hutchinson, 119-125, Whitfield Street, London, W.1. The Moseley Float-en-Air cushion consists of a series of tubes within a covering, which can be plain, fluted, or have a button fieish. Each tube has a patent form of valve and is inflated to a low pressure—slightly above that
B44
of the atmosphere, A separately inflated tube is used at each end of the cushion, thus making the sides noncollapsable.
The &tie° cushions and squabs consist of rubber hags made up to the exact size and shape required in the finished cushion. These are simply inserted in the machined-up leather covers and the seat is ready for immediate use. This prieciple makes for ease and simplicity in trimming.
Air cushions were to be found on several saloon coaches at the Show, and in the case of the 22-seater observation coach exhibited by Hall, Lewis and Co., Ltd,, the' pneumatic casings were mounted on an, ordinary spring case, so as to secure the utmost resiliency, it being felt that some of the natural buoyancy of the air cushion is destroyed if a hard bottom board be used, although it is agreed that a plywood base possesses certain " give."
One of the latest ideas in seat cushioning is the Sorb° rubber-sponge upholstery. Seats and squabs are built up of laminations of rubber sponge, each layer being staggered to give proper resiliency at every point of contact.
The type of seat employed and the material with which it is upholstered contribute very largely to the question of passengers' comfort. The exhibits at Olympia bore evidence of the bodybuilder's appreciation of these important facts. It has been said that most types of seat become " set " after
being occupied for some time, the. uneven distribution of the passenger's weight often creating lumps or hollows in a spring seat having a layer of padding. Recognizing this fact, Vickers, Ltd., provides, in some bodies, loose capoc% filled cushions, which can be used on the seat, against the back rest, or discarded altogether.
Ideas in Upholstering.
So far as upholstery is concerned, leather and leather cloth are largely used, and it is really surprising the variety of grains and colours in which the latter is available. Expensive furniture hides are often favoured for high-class
touring coaches, but Bedford cord and moquette also give a pleasing finish.
A tendency in upholstering was reflected at the Show in the case of a 36-seater bus body, shown by the Northern Counties Motor and Engineering Co., Ltd., on a Karrier sixwheeled chassis, the seats being covered with a combination of leather and moquette, the former being used for the roll of the cushion and back-rest and th.2 latter for the part upon which the passenger exerts most pressure. This is certainly a good idea, for it prevents passengers' clothes from becoming shiny, and provides a material which will withstand hard wear at those points where most friction occurs.
Some bodybuilders believe that the framing can be stiffened up by connection with the seats, but others prefer to bracket them to a seat board at the sides, so that the passenger's weight is carried direct by the underframing and additional stresses are not thrown on the body sides. This principle was adopted on a 25-seater body, built on an Associated Daimler chassis, shown at Olympia by United Automobile Services, Ltd., of Lowestoft. In this body, too, the sides were built on the double-skin method, the outer panels being entirely separated from the inner panels, thus allowing instantaneous drainage of the water from the sides and circulation of air around the framing, the latter serving to keep the timber well seasoned.
In a special lightweight body shown by the Northern Counties Motor and Engineering Co., Ltd., the body framing was carried by outriggers, the seats being supported on a specially constricted flyer clear of the framing. All stresses set up by' the passengers' weight are not communicated to the superstructure, for the reason that the load falls direct on the top of the frame itself.
Buffet and Toilet Arrangements.
Seating layouts remain very much the same, and there appears little tendency to depart from orthodox arrange-. ments. This, of course, implies that the intrusion of the rear-wheel arches into the interior still occasions some difficulty. In the case of regular-service buses the problem is usually met by the use of longitudinal seats over the arches, but in the case of the luxury coach it is often found convenient to box off a compartment on each side of the gangway, one serving as a kitchenette and the other pro-,
riding toilet facilities. This overcomes the wheel-arch trouble, but it blots out the view ahead for those people in the section at the rear.
Is it, therefore, 'better to transfer the miniature buffet and lavatory to the rear and to solve the wheel-arch problem in another way? Most bodybuilders say "yes," for the reason that greater privacy is afforded. Whichever plan is favoured, however, we think that it should be found possible to provide more space in these compartments ; some of them to be seen at the Show were very cramped.
It seems that it might be found practicable to build the kitchenette in the centre of the body, over the wheel arch on the near side, and to arrange the lavatory on the opposite side at the rear. The space over the off-side wheel arch could, perhaps, be railed off to accommodate luggage on the lines adopted for a 20-seater coach body by Messrs. EL E. Taylor and Co., of Norwich, who had it on view at Olympia on a Ben Pullman chassis. If such a scheme were adopted it might be possible to build a luggage grille at the rear, extending for the full depth of the body from the toilet compartment to the near side, the grille being of the type to be seen on a Leyland coach. In our next issue we shall complete our survey of bodywork progress and deal with other outstanding features which have been introduced with the object of ensuring comfortable travel under all conditions. Some of these points, although small in themselves, are quite important, and provide evidence of the desire on the part Of bodybuilders to study the many requirements of the travelling public.