ALL-METAL BODIES FOR BUSES AND COACHES.
Page 61
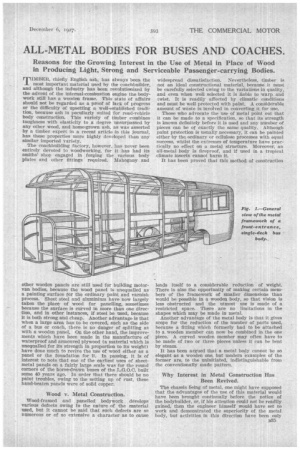
Page 62
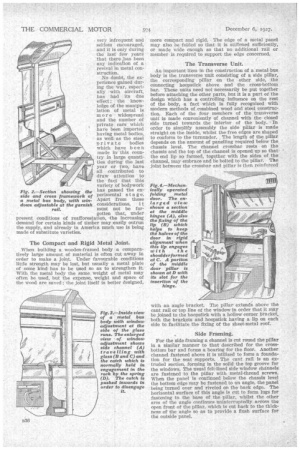
Page 63
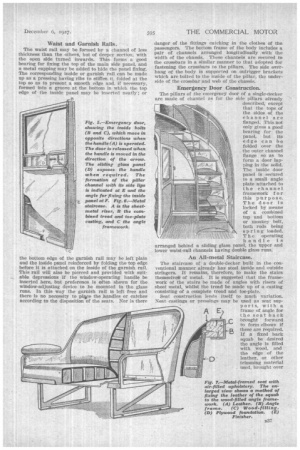
Page 64
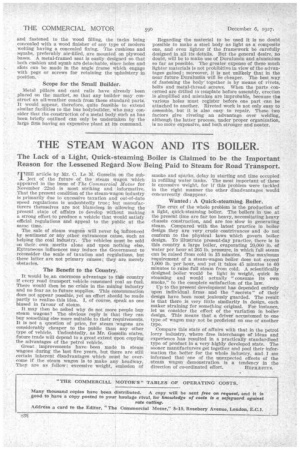
If you've noticed an error in this article please click here to report it so we can fix it.
Reasons for the Growing Interest in the Use of Metal in Place of Wood in Producing Light, Strong and Serviceable Passenger-carrying Bodies.
TIMBER, chiefly English ash, has always been the most important material used by the coachbuilder, and although the industry has been revolutionized by the advent of the internal-combustion engine the bodywork still has a wooden frame, This state of affairs should not be regarded as a proof of lack of progress or the difficulty of upsetting a well-established tradi tion, because ash is peculiarly suited for road-vehicle body construction. This variety of timber combines toughness with elasticity to a degree unsurpassed by any other wood, and home-grown ash, as was asserted by a timber expert in a recent article in this journal, has these properties more highly developed than any similar imported variety.
The coachbuilding factory, however, has never been entirely devoted to woodworking, for it has had its smiths' shop engaged in forging the various body plates and other fittings required. Mahogany and other wooden panels are still used for building motorvan bodies, because the wood panel is unequalled as a painting surface for the ordinary paint and varnish process. Sheet steel and aluminium have now largely taken the place of wood for panelling, sometimes because the surface is curved in more than one direction, and in other instances, if steel be used, because It is both strong and cheap. Another advantage is that when a large area has to be covered, such as the side of a bus or coach, there is no danger of splitting as with a wooden panel. On the other hand, the improvements which have been made in the manufacture of waterproof and armoured plywood (a material which is unequalled for its strength in proportion to its weight) have done much to revive the use of wood either as a panel or the foundation for it. In passing, it is of interest to note that one of the earliest uses of sheetmetal panels on a fairly large scale was for the round corners of the horse-drawn buses of the L.G.O.C. built some 40 years ago. In order that there should be no paint troubles, owing to the setting up of rust, these hand-beaten panels were of solid copper.
Wood v. Metal Construction.
Wood-framed and panelled bodywork develops various. defects owing to the nature of the material used, hut it cannot be said that such defects are so numerous or of so extensive a character as to cause
widespread dissatisfaction. Nevertheless, timber is not an ideal constructional material, because it must be carefully selected owing to the variations in quality, and even when well selected it is liable to warp and twist. It is readily affected by climatic conditions and must be well protected with paint. A considerable amount of waste is involved in converting it for use.
Those who advocate the use of metal point out that it can be made to a specification, so that its strength is known definitely before it is used and any number of pieces can be of exactly the same quality. Although paint protection is usually necessary, it can be painted either by the ordinary or cellulose processes with equal success, whilst the extremes of temperature have practically no effect on a metal structure. Moreover, an all-metal body is fireproof, and if used in a tropical climate insects cannot harm it.
• It has been proved that this method of construction lends itself to a considerable reduction of weight. There is also the opportunity of making certain members of the framework of smaller dimensions than would be possible in a wooden body, so that vision is less obstructed and the utmost use is made of a restricted space. There are no limitations in the shapes which may be made in metal.
Another advantage of the metal body is that it gives scope for the reduction of the number of parts used, because a fitting which formerly had to be attached to a wooden member can now be combined in the one piece. A curved wooden member may often have to be made of two or three pieces unless it can be bent by steam.
It has been argued that a metal body cannot be so elegant as a wooden one, but modern examples of the former are, to the uninitiated, indistinguishable from the conventionally made pattern.
Why Interest in Metal Construction Has Been Revived.
The chassis being of metal, one might have supposed that the advantages of the use of this material would have been brought continually before the notice of the bodybuilder, or, if his attention could not be readily gained, then the engineer himself would have set to work and demonstrated the superiority of the metal
body, but activities in this direction have been only very infrequent and seldom encouraged, and it is only during the last' few years that there ,Ilas been any indication of a revival in metal construction.
No doubt, the experience gained during the war, especially with aircraft, has had its due effect ; the knowledge of the manipulation of metal is more widespread and the number of private cars which have been imported having metal bodies, as well as the steel private bodies which have b een made in' this country in large quantities during the last year or two, have all contributed to draw attention to the fact that this variety of bodywork has passed the experimental stag e. Apart from these considerations, i t must not be forgotten that, under present conditions of reafforestation, the increasing demand for certain kinds of timber may .easily outrun the supply, and already in America much use is being made of substitute varieties. .. rail.
The Compact and Rigid Metal Joint.
When building a wooden-framed body a comparatively large amount of material is often cut away in order to make a joint. Under favourable conditions little strength may be lost, but usually a metal plate of some kind has to be used so as to strengthen it. With the metal body the same weight of metal may often be used, but the expense, weight and space of the wood are saved ; the joint itself is better designed, more compact and rigid. ' The edge of a metal panel may also be folded so that it is stiffened sufficiently, or made wide enough so that no additional rail or member is required to support the edge concerned.
The Transverse Unit.
An important item in the construction of a metal bus body is the transverse unit consisting of a side pillar, the corresponding pillar on the other side, the connecting hoopstick above and the cross-bottom bar. These units need not necessarily be put together before attaching the other parts, but it is a part of the design which has a controlling influence on the rest of the body, a fact which Is fully recognized with modern methods of combined wood and steel construction. Each of the four meMbers of the transverse unit is made conveniently of channel with the closed side turned towards the interior of the body. In order to simplify assembly the side pillar is made straight on the inside, whilst the free edges are shaped to conform to the turnunder. The length of the pillar depends on the amount of panelling required below the chassis level. The channel crossbar rests on the chassis and the top of the channel is opened up so that the end lip so formed, together with the sides of the channel, may embrace and be bolted to the pillar. The joint between the crossbar and pillar is then reinforced with an angle bracket. The pillar extends above the cant rail or top line of the window in order that it may be joined to the hoopstick with a hollow corner bracket, both the brackets and hoopstick having a lip on each side to facilitate the fixing of the sheet-metal roof.
Side Framing.
For the side framing a channel is cut round the pillar in a similar manner to that described for the crossbottom bar and forms a bearing for the floor. Another channel fastened above it is utilized to form a foundation for the seat supports. The cant rail is an extruded section, forming in the solid the top groove for the windows. The usual felt-lined side window channels are fastened to the pillar with metal-thread screws. When the panel Is continued below the chassis level the bottom edge may be fastened to an angle, the panel being turned over and riveted on the back edge. The horizontal surface of this angle is cut to form lugs for fastening to the base of the pillar, whilst the other arm or the angle continues uninterruptedly across the open front of the pillar, which is cut back to the thickness of the angle so as to provide a flush surface for the outside panel. Waist and Garnish Rails.
The waist rail may be formed by a channel of less thickness than the others, but of deeper section, with the open side turned inwards. This forms a good bearing for fixing the top of the main side panel, and a metal capping may be added to hide the panel fixing. The corresponding inside or garnish rail can he made up as a pressing having ribs to stiffen it, folded at the top so as to present a smooth edge and, if necessary, formed into a groove at the bottom in which the top edge of the inside panel may be inserted neatly ; or the bottom edge of the garnish rail may be left plain and the inside panel reinforced by folding the top edge before it is attached on the inside of the garnish rail. This rail will also be pierced and provided with suitable depressions if the window-operating handle be inserted here, but preference is often shown for the window-adjusting device to be mounted in the glass runs. In this way the garnish rail is left free and there is no necessity to pla,ce the handles or catches according to the disposition of the seats. Nor is there danger of the fittings catching in the clothes of the passengers. The bottom frame of the body includes a pair of channels arranged longitudinally with the width of the chassis. These channels are secured to the crossbars in a similar manner to that adopted for fastening the crossbars to the pillars. The side overhang of the body is supported on outrigger brackets which are bolted to the inside of the pillar, the underside of the crossbar and web of the chassis.
Emergency Door Construction.
The pillars of the emergency door of a single-decker are made of channel as for the side pillars already described, except that the tops of the sides of the channel are flanged. This not only gives a good bearing for the panel, but its edge can be folded over the the outer channel flange, so • as to form a door lapping in the solid. The inside door panel is secured to a small angle plate attached to the channel framework f o r this purpose. The door is locked by means of a combined top and bottom or monkey bolt, both rods being T h e operating spring loaded.
handle is arranged behind a sliding glass panel, the upper and lower waist-rail channels having double glass runs.
An All-metal Staircase.
The staircase of a double-decker built in the conventional manner already has steel inside and outside stringers. It remains, therefore, to make the stairs themselves of metal. It is suggested that the framework of the stairs be made of angles with risers of sheet metal, whilst the tread be made up of a casting consisting of a complete tread and toe-plate.
Seat construction lends itself to much variation. Neat castings or pressings may be used as seat support s, with a
A E frame of angle for the seat back brought forward to form elbows if these are required. If a fixed back squab be desired the angle is filled with wood, and the edge of the leather, or other trimming material used, brought over and fastened to the wood filling, the tacks being .concealed with a wood finisher of any type of modern welting having a concealed fixing. The cushions and squabs, preferably air-filled, are mounted on plywood bases. A. metal-framed seat is easily designed so that both cushion and squab are detachable, since holes and sIots can be made in the angle frame which engage with pegs or screws for retaining the upholstery in position.
Scope for the Small Builder.
Metal pillars and cant rails have already been placed on the market, so that any builder may construct an all-weather coach from these standard parts. It would appear, therefore, quite feasible to extend similar facilities to the bus bodybuilder, who may consider that the construction of a metal body such as has been briefly outlined can only be undertaken by the large firm having an expensive plant at its command. Regarding the material to be used it is no doubt possible to make a steel body as light as a composite one, and even lighter if the framework be carefully designed in all its details. But the general desire, no doubt, will be to make use of Duralumin and aluminium so far as possible. The greater expense of these much lighter materials is not prohibitive in view of the advantages gained ; moreover, it is not unlikely that in the near future Duraluinin will be cheaper. The best way of fastening the body together is by means of rivets, bolts and metal-thread screws. When the parts concerned are drilled to template before assembly, erection is simplified and mistakes are improbable, because the various holes must register before one part can be attached to another. Riveted work is not only easy to assemble, but it is also easy to repair. These two factors give riveting an advantage over welding, although the latter process, under proper organization, is no more expensive, and both stronger and neater.