Repairing Zinc Castings by Welding
Page 21
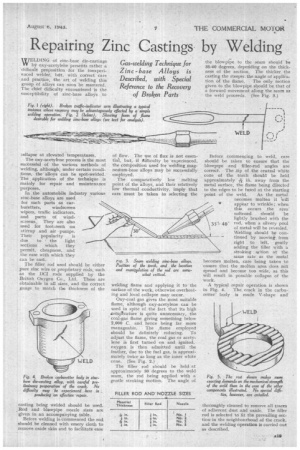
If you've noticed an error in this article please click here to report it so we can fix it.
Gas-welding Technique for Zinc-base Alloys is Described, with Special Reference to the Recovery of Broken Parts
WELDING of zinc-base die-castings IT by oxy-acetylehe presents rather a difficult proPosition for the inexperieuced welder, knit, with correct care and practice, the art of welding this group of alloys can soon be mastered. The chief difficulty encountered is the susceptibility of zinc-base alloys to collapse at elevated temperatures.
The oxy-acetylene process is the most successful of the various methods of welding, although, under certain conditions, the alloys can be spot-welded. The application of the technique is mainly for repair and maintenance purposes.
In the automobile industry various zinc-base alloys are used for such parts as car buretters, windscreen wipers, traffic indicators, and parts of windscreens.. They are also used for foot,restt on stirrup and air pumps. Their popularity is due to the light sections which they permit, cheapness, and the ease with which they can be cast.
The filler rod used should be either pure zinc wire or proprietary rods, such as the DCI rods supplied by the British Oxygen Co., Ltd. These are obtainable in all sizes, and the correct gauge to match the thickness of the casting being welded should be used. , Rod and blowpipe nozzle sizes are given in an accompanying table.
Before welding is commenced the rod should be cleaned with emery cloth to remove oxide skin and to facilitate ease of flow. The use of flux is not essential, but, if difficulty be experienced, the composition used for welding magnesium-base alloys may be successfully employed.
The comparatively low melting point of the alloys, and their relatively low thermal conductivity, imply that care must be taken in selecting the welding flame and applying it to the surface of the work, otherwise overheating and local collapse may occur.
Oxy-coal gas gives the most suitable flame, although oxy-acetylene can be used in spite of the fact that its high tetcipserature is quite unnecessary, the coal-gas flame giving something below 2,000 C. and hence being far more manageable. The ,flame employed should be definitely reducing. To adjust the flame, the coal gas or acetylene is first turned on and ignited, oxygen is then admitted until the feather, due tä the fuel gas, is approximately twice as long as the inner white, cone. (See Fig. 2.)
The filler rod should be held at approximately 30 degrees to the weld seam, the rod being applied with a gentle stroking motion, The angle of the blowpipe to the seam should be• 35-40 degrees, depending on the thickness of the section. The thicker the casting the steeper. the angle of application of the flame. The only motion given to the blowpipe should be that of a forward movement along the seam as the weld proceeds. (See Fig. 3.) Before commencing to weld, care should be taken to ensure that the blowpipe and filler-rod angles are correct_ The ;tip of the central white cone of the torch should be held approximately in. away from the metal surface, the flame being directed to the edges to be fused at the starting point of the weld. As the metal necomes molten it Will appear to wrinkle; when this occurs the area softened should be lightly brushed with the rod, when a silvery pool of metal will be revealed, Welding should be continued by moving from right to left, gently adding the filler with a stroking action at the same rate as the metal becomes molten, care being taken to ensure that the molten area does not spread and become too wide, as this will result in possible collapse of the work.
A typical repair operation is shown
in Fig. 4. The crack in the carburetter body is made V-shape and
thoroughly cleaned to remove all traces of adherent dust and oxide. The filler rod is selected to fit the prevailing 'section in the neighbourhood of the crack, and the welding operation is carried out as described.