Rolling out the barrel is easy for Whitbread
Page 49
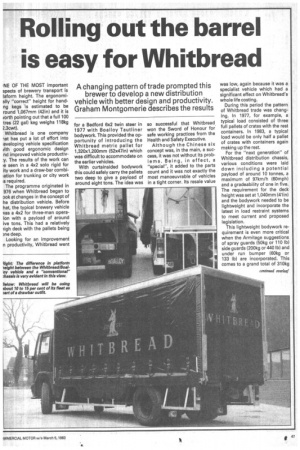
Page 50
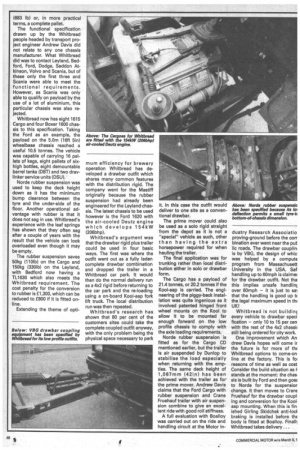
If you've noticed an error in this article please click here to report it so we can fix it.
A changing pattern of trade prompted this brewer to develop a new distribution vehicle with better design and productivity. Graham Montgomerie describes the results
1NE OF THE MOST important spects of brewery transport is laform height. The ergonomially "correct" height for handng kegs Is estimated to be round 1,067mm (42in) and it is north pointing out that a full 100 tres (22 gal) keg weighs 118kg 2.3cwt).
Whitbread is one company at has put a lot of effort into eveloping vehicle specification 60ith good ergonomic design nd improved vehicle productivThe results of the work can le seen in a 4x2 solo rigid for ity work and a draw-bar combiiation for trunking or city work is required.
The programme originated in 976 when Whitbread began to ook at changes in the concept of he distribution vehicle. Before hat, the typical brewery vehicle vas a 4x2 for three-man operaion with a payload of around ive tons. This had a relatively ugh deck with the pallets being )ne deep.
Looking for an improvement n productivity, Whitbread went for a Bedford 6x2 twin steer in 1977 with Boalloy Tautliner bodywork. This provided the opportunity of introducing the Whitbread metric pallet for 1,320x1,200mm (52x471n) which was difficult to accommodate on the earlier vehicles.
With curtainsided bodywork this could safely carry the pallets two deep to give a payload of around eight tons. The idea was
so successful that Whitbread won the Sword of Honour for safe working practices from the Health and Safety Executive.
Although the Chinese six concept was, in the main, a success, it was not without its problems. Being, in effect, a "special", it added to the parts count and it was not exactly the most manoeuvrable of vehicles in a tight corner. Its resale value
was low, again because it was a specialist vehicle which had a significant effect on Whitbread's whole life costing.
During this period the pattern of Whitbread trade was changing. In 1977, for example, a typical load consisted of three full pallets of crates with the rest containers. In 1983, a typical load would be only half a pallet of crates with containers again making up the rest.
For the "next generation" of Whitbread distribution chassis, various conditions were laid down including a potential payload of around 10 tonnes, a maximum of 97km/h (60mph) and a gradeability of one in five. The requirement for the deck height was set at 1,040mm (41in) and the bodywork needed to be lightweight and incorporate the latest in load restraint systems to meet current and proposed legislation.
This lightweight bodywork requirement is even more critical when the Armitage suggestions of spray guards (50kg or 110 lb) side guards (200kg or 440 lb) and under run bumper (60kg or 133 lb) are incorporated. This comes to a grand total of 310kg (683 lb) or, in more practical terms, a complete pallet.
The functional specification drawn up by the Whitbread people headed by transport project engineer Andrew Davis did not relate to any one chassis manufacturer. What Whitbread did was to contact Leyland, Bedford, Ford, Dodge, Seddon Atkinson, Volvo and Scania, but of these only the first three and Scania were able to meet the functional requirements. However, as Scania was only able to qualify on payload by the use of a lot of aluminium, this particular chassis was also rejected.
Whitbread now has eight 1615 Cargo and four Boxer 1600 chassis to this specification. Taking the Ford as an example, the payload on the 5.0m (16ft 51n) wheelbase chassis reached a useful 10.5 tonnes. The vehicle was capable of carrying 16 pallets of kegs, eight pallets of sixhigh bottles, eight demountable barrel tanks (DBT) and two draylinker service units (DSU).
Norde rubber suspension was used to keep the deck height down as it has the minimum bump clearance between the tyre and the under-side of the floor. Another operational advantage with rubber is that it does not sag in use. Whitbread's experience with the leaf springs has shown that they often sag after a couple of years with the result that the vehicle can look overloaded even though it may be empty.
The rubber suspension saves 50kg (110Ib) on the Cargo and 150kg (330Ib) on the Leyland, with Bedford now having a TL1630 which also meets the Whitbread requirement. The cost penalty for the conversion to rubber is £1,300, which can be reduced to £800 if it is fitted online.
Extending the theme of opti mum efficiency for brewery operation Whitbread has developed a drawbar outfit which shares many common features with the distribution rigid. The company went for the Mastiff originally because the rubber suspension had already been engineered for the Leyland chassis. The latest chassis to be used however is the Ford 1620 with the air-cooled Deutz engine which develops 154 kW (206bhp).
Whitbread's argument was that the drawbar rigid plus trailer could be used in four basic ways. The first was where the outfit went out as a fully laden complete drawbar combination and dropped the trailer in a Whitbread car park. It would then do the normal delivery run as a 4x2 rigid before returning to the car park and the re-loading using a on-board Kooi-aap fork lift truck. The local distribution run was then repeated.
Whitbread's research has shown that 80 per cent of the customers sites could take the complete coupled outfit anyway, with the only problem being the physical space necessary to park t. In this case the outfit would deliver to one site as a conventional drawbar.
The prime mover could also be used as a solo rigid straight from the depot as it is not a "special" vehicle as such, other than having the extra horsepower required for when hauling the trailer.
The final application was for trunking rather than local distribution either in solo or drawbar form.
The Cargo has a payload of 21.4 tonnes, or 20.2 tonnes if the Kooi-aap is carried. The engineering of the piggy-back installation was quite ingenious as it involved patented hinged front wheel mounts on the Kooi to allow it to be mounted far enough forward on the low profile chassis to comply with the axle loading requirements.
Norde rubber suspension is fitted as for the Cargo CD mentioned earlier, but the trailer is air suspended by Dunlop to stabilise the load especially when returning with the empties. The same deck height of 1,067mm (42in) has been achieved with the trailer as for the prime mover. Andrew Davis claims that the Ford Cargo with rubber suspension and Crane Fruehauf trailer with air suspension combine to give an excellent ride with good roll stiffness.
A full evaluation with Boalloy was carried out on the ride and handling circuit at the Motor In dustry Research Associatio proving-ground before the con' bination ever went near the put lic roads. The drawbar couplinl is by VBG, the design of whic was helped by a compute program from Massachusett University in the USA. Sat handling up to 60mph is claime( for the drawbar outfit. Not tha this implies unsafe handlini over 60mph — it is just to sa) that the handling is good up tE the legal maximum speed in th( UK!
Whitbread is not buildini every vehicle to drawbar speci fication — only 10 to 15 per cen with the rest of the 4x2 chassil still being ordered for city work.
One improvement which An drew Davis hopes will come ir the future is for more of thE Whitbread options to come-on line at the factory. This is foi reasons of time as well as cost Consider the build situation as ii stands at the moment: the chas sis is built by Ford and then goes to Norde for the suspensior change. It then moves to CranE Fruehauf for the drawbar coupi. ing and conversion for the Kooi. aap mounting. When this is fin ished Girling Skidchek anti-loci braking is installed before thE body is fitted at Boalloy. Final!) Whitbread takes delivery ...