From T
Page 18
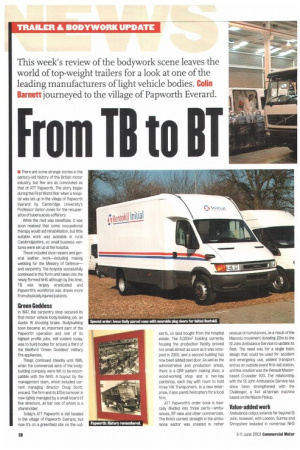
Page 19
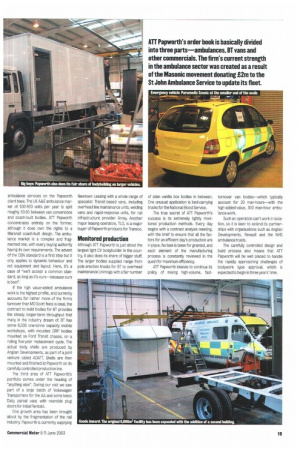
If you've noticed an error in this article please click here to report it so we can fix it.
to B
This week's review of the bodywork scene leaves the world of top-weight trailers for a look at one of the leading manufacturers of light vehicle bodies. Colin Barnett journeyed to the village of Papworth Everard.
• There are some strange stories in the century-old history of the British motor industry, but few are as convoluted as that of AU Papworth. The story began during the First World War when a hospital was set up in the village of Papworth Everard by Cambridge University's Professor Varior-Jones for the recuperation of tuberculosis sufferers.
While the rest was beneficial, it was soon realised that some occupational therapy would aid rehabilttation, but little suitable work was available in rural Cambridgeshire, so small business ventures were set up at the hospital.
These included shoe repairs and general leather work—including making webbing for the Ministry of Defence— and carpentry The hospital successfully continued in this form until taken into the newly-formed NHS although by this time, TB was largely eradicated and Papworth's workforce was drawn more from physically injured patients.
Green Goddess
In 1947, the carpentry shop secured its first motor vehicle body-building job, an Austin 16 shooting brake. Bodybuilding soon became an important part of the Papworth operation and one of its highest profile jobs, still evident today, was to build bodies for around a third of the Bedford 'Green Goddess' military fire appliances.
Things continued steadily until 1995, when the commercial aims of the bodybuilding company were felt to be incompatible with the NHS. A buyout by the management team, which included current managing director Doug Scott, ensued. The firm and its 210m turnover is now tightly managed by a small board of five directors, all bar one of whom is a shareholder.
Today's All Papworth is still located in the village of Papworth Everard, but now it's on a greenfield site on the out
skirts, on land bought from the hospital estate. The 6,000m2 building currently housing the production facility proved too small almost as soon as it was occupied in 2000, and a second building has now been added next door. As well as the administrative and production areas, there is a GRP pattern making shop, a wood-working shop and a two-bay paintshop, each bay with room to hold three VW Transporters. In a new enterprise, it also paints helicopters for a local firm.
AU Papworth's order book is basically divided into three parts—ambulances, BT vans and other commercials. The firm's current strength in the ambulance sector was created in rather unusual circumstances, as a result of the Masonic movement donating 22m to the St John Ambulance Service to update its fleet. The need was for a single basic design that could be used for accident and emergency use, patient transport and as an outside-event first-aid station, and the solution was the Renault Masterbased Crusader 900. The relationship with the St John Ambulance Service has since been strengthened with the Challenger, a 4x4 all-terrain machine based on the Nissan Pickup.
Value-added work
Ambulance output extends far beyond St John, however, with London, Surrey and Shropshire included in numerous NHS ambulance services on the Papworth client base. The UK A&E ambulance market of 500-600 units per year is split roughly 50:50 between van conversions and coach-built bodies. AU Papworth concentrates entirely on the former, although it does own the rights to a Marshall coach-built design. The ambulance market is a complex and fragmented one, with every buying authority having its own requirements. The advent of the GEN standard is a first step but it only applies to dynamic behaviour and not equipment and layout. Here, it's a case of "we'll accept a common standard, as long as it's ours—because ours is best".
If the high value-added ambulance work is the highest profile, and currently accounts for rather more of the firm's turnover than MID Scott feels is ideal, the contract to build bodies for BT provides the steady longer-term throughput that many in the industry dream of. BT has some 6,000 one-tonne capacity mobile workshops, with moulded GAP bodies mounted on Ford Transit chassis, on a rolling five-year replacement cycle. The actual body shells are produced by Anglian Developments, as part of a joint venture called ADATT. Shells are then mounted and finished at Papworth on its carefully controlled production line.
The third area of AU Papworth's portfolio comes under the heading of "anything else". During our visit we saw part of a large batch of Volkswagen Transporters for the AA and some lveco Daily parcel vans with nearside plug doors for Initial Rentokil.
One growth area has been brought about by the fragmentation of the rail industry. Papworth is currently supplying Newtown Leasing with a whole range of specialist Transit-based vans, including overhead line maintenance units, welding vans and rapid-response units, for rail infrastructure provider Amey. Another major leasing operation, TLG, is a major buyer of Papworth products for Transco.
Monitored production
Although ATT Papworth is just about the largest light CV bodybuilder in the country, it also does its share of bigger stuff. The larger bodies supplied range from pole erection trucks for BT to overhead maintenance Unimogs with a fair number of plain vanilla box bodies in between. One unusual application is bed-carrying trucks for the National Blood Service.
The true secret of ATT Papworth's success is its extremely tightly monitored production methods. Every day begins with a contract analysis meeting, with the brief to ensure that all the factors for an efficient day's production are in place. No task is taken for granted, and each element of the manufacturing process is constantly reviewed in the quest for maximum efficiency.
AU Papworth intends to continue its policy of mixing high-volume, fast
turnover van bodies—which typically account for 20 man-hours—with the high-added-value, 300 man-hour ambulance work.
Such an operation can't work in isolation, so it is keen to extend its partnerships with organisations such as Anglian Developments, Renault and the NHS ambulance trusts.
The carefully controlled design and build process also means that All Papworth will be well placed to handle the rapidly approaching challenges of bodywork type approval, which is expected to begin in three years' time.