OM RUSSIA ITH MAZ
Page 34
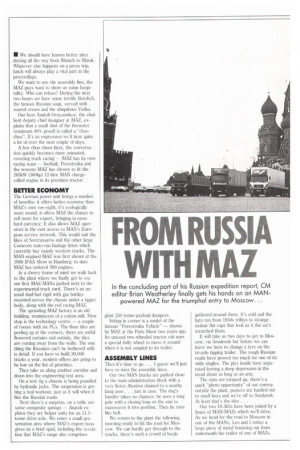
Page 35
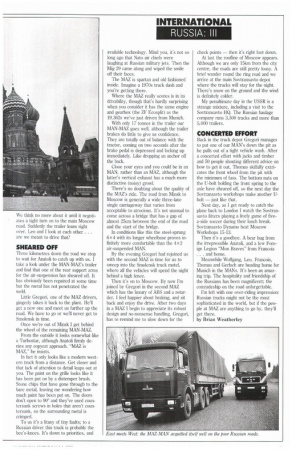
If you've noticed an error in this article please click here to report it so we can fix it.
In the concluding part of his Russian expedition report, CM editor Brian Weatherley finally gets his hands on an MANpowered MAZ for the triumphal entry to Moscow ...
10 We should have known better after driving all the way from Munich to Minsk. Whatever else happens on a press trip, lunch will always play a vital part in the proceedings.
We want to see the assembly line; the MAZ guys want to show us some hospitality. Who can refuse? During the next two hours we have some terrific Borshch, the famous Russian soup, served with soured cream and the ubiquitous Vodka.
Our host Anatoli Ovsyannikov, the ebullient deputy chief designer at MAZ, explains that a small shot of the firewater (minimum 40% proof) is called a "choo choo". It's an expression we'd hear quite a lot of over the next couple of days.
A few choo choos later, the conversation quickly becomes more animated, covering truck racing — MAZ has its own racing team — football, Perestroika and the reasons MAZ has chosen to fit the 265kW (360hp) 12-litre MAN chargecoiled engine in its premium tractor.
NEWER ECONOMY
The German power unit brings a number of benefits: it offers better economy than MAZ's own vee-eight; it's ecologically more sound; it offers MAZ the chance to sell more for export, bringing in more hard cun-ency; It also allows MAZ operators in the east access to MAN's European service network. This would suit the likes of Sovtransavto and the other large Comecon state-run haulage firms which currently buy mainly western trucks. The MAN-engined MAZ was first shown at the 1988 IFAA Show in Hamburg: to date MAZ has ordered 500 engines.
In a cheery frame of mind we walk back to the plant where we finally get to see our first MAZ-MANs parked next to the experimental-truck yard. There's an unusual dual-fuel rigid with gas bottles mounted across the chassis under a tipper body, along with the red racing MAZ.
The sprawling MAZ factory is an old building, reminiscent of a cotton mill. First stop is the technology centre — a couple of rooms with six PCs. 'I'he floor tiles are peeling up at the corners, there are awful flowered curtains and outside, the tiles are coming away from the walls. The one thing the Russians can't be bothered with is detail. If you have to build 39,000 trucks a year, modern offices are going to be low on the list of priorities.
They take us along another corridor and down into the engineering test area.
On a test rig a chassis is being pounded by hydraulic jacks. The suspension is getting a real workout, just as it will when it hits the Russian roads.
Next there's a surprise, on a table are some composite springs — Anatoli explains they are helper units for an 11.5tonne drive axle. We enter a small presentation area where MAZ's export boss gives us a brief spiel, including the revelation that MAZ's range also comprises giant 250-tonne-payload dumpers.
Sitting in corner is a model of the famous "Perestroika Vehicle" — shown by MAZ at the Paris Show two years ago. Its unusual two-wheeled tractor cab uses a special dolly wheel to move it around when it is not coupled to its trailer.
ASSEMBLY LINES
Then it's time to go . . I guess we'll just have to miss the assembly lines.
Our two MAN trucks are parked close to the main administration block with a very fierce Alsation chained to a nearby lamp post . . . just in case. The dog's handler takes no chances: he uses a long pole with a closing loop on the end to manoeuvre it into position. Then he runs like hell.
We return to the plant the following morning ready to hit the road for Moscow. We can hardly get through to the trucks, there's such a crowd of locals gathered around them. It's cold and the hats run from 1950s trilbys to strange mohair flat caps that look as if the cat's scratched them.
It will take us two days to get to Moscow, via Smolensk but before we can leave we have to change a tyre on the tri-axle tipping trailer. The tough Russian roads have proved too much for one of its wide singles. The plys inside have separated leaving a deep depression in the tread about as long as an arm.
The nuts are torqued up, there's a quick "photo opportunity" of our convoy outside the plant, posters are handed out to small boys and we're off to Smolensk. At least that's the idea . . .
Our two 19.362s have been joined by a brace of MAN-MAZs which we'll drive. As we head for the road to Moscow in one of the MANs, Leo and I notice a large piece of metal bouncing out from underneath the trailer of one of MAZs. We think no more about it until it negotiates a tight turn on to the main Moscow road. Suddenly the trailer leans right over. Leo and I look at each other. . . are we meant to drive that?
SHEARED OFF
Three kilometres down the road we stop to wait for Anatoli to catch up with us. I take a look under the MAN-MAZ's trailer and find that one of the rear support urns for the air-suspension has sheared off. It has obviously been repaired at some time but the metal has not penetrated the weld.
Little Gregori, one of the MAZ drivers, gingerly takes it back to the plant. He'll get a new one and meet us further up the road. We have to go or we'll never get to Smolensk in time.
Once we're out of Minsk I get behind the wheel of the remaining MAN-MAZ.
From the outside it looks somewhat like Turbostar, although Anatoli firmly denies any copycat approach. "MAZ is MAZ," he insists.
In fact it only looks like a modern western truck from a distance. Get closer and that lack of attention to detail leaps out at you. The paint on the grille looks like it has been put on by a distemper brush. Stone chips that have gone through to the bare metal, leaving me wondering how much paint has been put on. The doors don't open to 900 and they've used countersunk screws in holes that aren't countersunk, so the surrounding metal is crimped.
To us it's a litany of tiny faults; to a Russian driver this truck is probably the bee's-knees. It's down to priorities, and available technology. Mind you, it's not so long ago that Nato air chiefs were laughing at Russian military jets. Then the Mig 29 came along and wiped the smile off their faces.
The MAZ is spartan and old fashioned inside. Imagine a 1970s truck dash and you're getting there.
Where the MAZ really scores is in its drivability, though that's hardly surprising when you consider it has the same engine and gearbox (the 'a.' Ecosplit) as the 19.362s we've just driven from Munich.
With only 17 tonnes in the trailer our MAN-MAZ goes well, although the trailer brakes do little to give us confidence. They are totally out of balance with the tractor, coming on two seconds after the brake pedal is depressed and locking up immediately. Like dropping an anchor off the back.
Close your eyes and you could be in an MAN, rather than an MAZ, although the latter's vertical exhaust has a much more distinctive (noisy) growl.
There's no doubting about the quality of the MAZ's ride. The road from Minsk to Moscow is generally a wide three-lane single carriageway that varies from acceptable to atrocious. It's not unusual to come across a bridge that has a gap of almost 25cm between the end of the road and the start of the bridge.
In conditions like this the steel-sprung 6x4 with its longer wheelbase proves infinitely more comfortable than the 4x2 air-suspended MAN.
By the evening Gregori had rejoined us with the second MAZ in time for us to sweep into the Smolensk truck motel, where all the vehicles will spend the night behind a high fence.
Then it's on to Moscow. By now I'm joined by Gregori in the second MAZ which has the luxury of ABS and a retarder. I feel happier about braking, and sit back and enjoy the drive. After two days in a MAZ I begin to appreciate its robust design and no-nonsense handling. Gregori, has to remind me to slow down for the check points — then it's right foot down.
At Last the roofline of Moscow appears. Although we are only 15km from the city centre, the roads are still pretty lousy. A brief wander round the ring road and we arrive at the main Sovtransavto depot where the trucks will stay for the night. There's snow on the ground and the wind is definitely colder.
My penultimate day in the USSR is a strange mixture, including a visit to the Sovtransavto HQ. The Russian haulage company runs 3,500 trucks and more than 5,000 trailers.
CONCERTED EFFORT
Back in the truck depot Gregori manages to put one of our MAN's down the pit as he pulls out of a tight vehicle wash. After a concerted effort with jacks and timber and 50 people shouting different advice on how to get it out, Thomas skilfully extricates the front wheel from the pit with the minimum of fuss. The bottom nuts on the U-bolt holding the front spring to the axle have sheared off, so the next day the Sovtransavto workshops make another Ubolt — just like that.
Next day, as I get ready to catch the plane back to London I watch the Sovtransavto fitters playing a lively game of fivea-side soccer during their lunch break_ Sovtransavto Dynamo beat Moscow Workshops 15-13.
Then it's a goodbye. A bear hug from the irrepressible Anatoli, and a few Foreign Legion "Mon Braves" from Francois . . . and home.
Meanwhile Wolfgang, Leo, Francois, Thomas and Gerlach are heading home for Munich in the MANs. It's been an amazing trip. The hospitality and friendship of the Russians has been magnificent; the comradeship on the road unforgettable.
I'm left with one over-riding impression: Russian trucks might not be the most sophisticated in the world, but if the people at MAZ are anything to go by, they'll get there.
by Brian Weatherley