Change for the better at modest price
Page 34
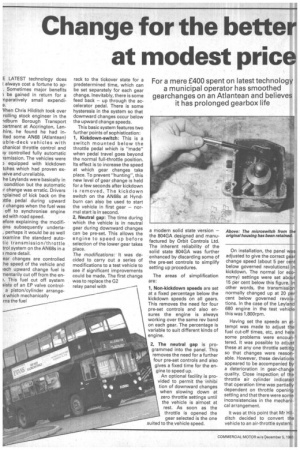
Page 35
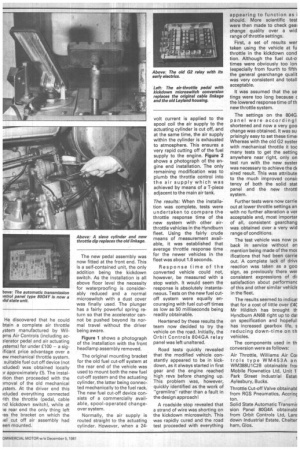
If you've noticed an error in this article please click here to report it so we can fix it.
For a mere £400 spent on latest technology a municipal operator has smoothed gearchanges on an Atlantean and believes it has prolonged gearbox life
E LATEST technology does always cost a fortune to ap. Sometimes major benefits 1 be gained in return for a nparatively small expendie.
Vhen Chris Hilditch took over rolling stock engineer in the idburn Borough Transport 3artment at Accrington, Lanhire, he found he had inited some AN68 (Atlantean) uble-deck vehicles with chanical throttle control and iy controlled fully automatic lsmission. The vehicles were ) equipped with kickdown tches which had proven ex'sive and unreliable.
he Leylands were basically in condition but the automatic r change was erratic. Drivers iplained of kick back on the Atle pedal during upward r changes when the fuel was off to synchronise engine ed with road speed.
efore explaining the modifions subsequently underta, perhaps it would be as well .ixamine the standard autotic transmission/throttle trol system on the AN68s in a more detail.
ear changes are controlled :he speed of the vehicle and iach upward change fuel is -nentarily cut off from the en:. This fuel cut off system sists of an EP valve control
rack to the tickover state for a predetermined time, which can be set separately for each gear change. Inevitably, there is some feed back — up through the accelerator pedal. There is some hysteresis in the system so that downward changes occur below the upward change speeds.
This basic system features two further points of sophistication: 1, Kickdown-switch: This is a switch mounted below the throttle pedal which is "made" when pedal travel goes beyond the normal full-throttle position. Its effect is to increase the speed at which gear changes take place. To prevent "hunting", this new level of gear change is held for a few seconds after kickdown is removed. The kickdown switch on the AN68s at Hyndburn can also be used to start the vehicle in first gear — normal start is in second.
2, Neutral gap: The time during which the vehicle is in neutral gear during downward changes can be pre-set. This allows the engine to speed up before selection of the lower gear takes place.
The modifications: It was decided to carry out a series of modifications to a test vehicle to see if significant improvements could be made. The first change was to replace the G2 relay panel with a modern solid state version — the 804GA designed and manufactured by Orbit Controls Ltd. The inherent reliability of the solid state 804GA was further enhanced by discarding some of the pre-set controls to simplify setting up procedures.
The areas of simplification are: 1, Non-kickdown speeds are set at a fixed percentage below the kickdown speeds on all gears. This removes the need for four pre-set controls and also ensures the engine is always working over the same rev band on each gear. The percentage is variable to suit different kinds of engine.
2, The neutral gap is programmed into the panel. This removes the need for a further four pre-set controls and also gives a fixed time for the engine to speed up.
An optional facility is provided to permit the inhibi tion of downward changes when slowing down at zero throttle settings until the vehicle is almost at rest. As soon as the throttle is opened the gear selected is the one suited to the vehicle speed. On installation, the panel was adjusted to give the correct gear change speed (about 5 per cent below governed revolutions) in kickdown. The normal (or economy) settings were set about 15 per cent below this figure. In other words, the transmission normally changed up at 20 per cent below governed revolutions. In the case of the Leyland 680 engine in the test vehicle this was 1,800rpm.
Having set the speeds an attempt was made to adjust the fuel cut-off times, etc, and here some problems were encountered. It was possible to adjust these at any one throttle setting so that changes were reasonable. However, these deviations appeared to be accompanied by a deterioration in gear-change quality. Close inspection, of the throttle air cylinder indicated that operation time was partially dependent on throttle opening setting and that there were some inconsistencies in the mechanical arrangement.
It was at this point that Mr Hilditch decided to convert the vehicle to an air-throttle system.
He discovered that he could btain a complete air throttle vstem manufactured by Wilwris Air Controls (including acDlerator pedal and air actuating vstems) for under £100 — a sigificant price advantage over a ew mechanical throttle system. suitable fuel cut off device (not icluded) was obtained locally )rapproximately £5. The instalrtion then proceeded with the )moval of the old mechanical vstem, At the driver end this iclucled everything connected Fith the throttle (pedal, cable nd kickdown switch), while at le rear end the only thing left as the bracket on which the rel cut off air assembly had een mounted.
The new pedal assembly was now fitted at the front end. This is a self-contained unit, the only addition being the kickdown switch. As the installation is all above floor level the necessity for waterproofing is considerably reduced and a normal microswitch with a dust cover was finally used. The plunger has a fairly powerful spring return so that the accelerator cannot be pushed beyond its normal travel without the driver being aware.
Figure 1 shows a photograph of the installation with the front headlamp assembly removed.
The original mounting bracket for the old fuel cut-off system at the rear end of the vehicle was used to mount both the new fuel cut-off system and the actuating cylinder, the latter being connected mechanically to the fuel rack. The new fuel cut-off device consists of a commercially available, spool-operated changeover system.
Normally, the air supply is routed straight to the actuating cylinder. However, when a 24
volt current is applied to the spool coil the air supply to the actuating cylinder is cut off, and at the same time, the air supply within the cylinder is exhausted to atmosphere. This ensures a very rapid cutting off of the fuel supply to the engine. Figure 2 shows a photograph of the engine end installation. The only remaining modification was to plumb the throttle control into the air supply which was achieved by means of a T-piece adjacent to the main air tank.
The results: When the installation was complete, tests were undertaken to compare the throttle response time of the new system with other airthrottle vehicles in the Hyndburn fleet. Using the fairly crude means of measurement available, it was established that average throttle response time for the newer vehicles in the fleet was about 1.8 seconds.
Response time of the converted vehicle could not, however, be measured with a stop watch. It would seem the response is absolutely instantaneous. Tests on the new fuel cutoff system were equally encouraging with fuel cut-off times as low as 50 milliseconds being readily obtainable.
Heartened by these results the team now decided to try the vehicle on the road. Initially, the Orbit Controls 80 4GA relay panel was left unaltered.
Road tests quickly revealed that the modified vehicle constantly appeared to be in kickdown, as it always started in first gear and the engine reached high revs before changing up. This problem was, however, quickly identified as the work of "gremlins" rather than a fault in the design approach!
A roadside stop revealed that a strand of wire was shorting on the kickdown rnicroswitch. This was rapidly cured and the road test proceeded with everything appearing to function as i should. More scientific test were then made to check geei change quality over a wid range of throttle settings.
First, a set of results wer taken using the vehicle at fu throttle in the kickdown cond tion. Although the fuel cut-o. times were obviously too Ion (especially from fourth to fifth the general gearchange qualit was very consistent and total) acceptable.
It was assumed that the se. tings were too long because c the lowered response time of th new throttle system.
The settings on the 804G panel were according) shortened and now a very goo change was obtained. It was su prisingly easy to set these timer Whereas with the old G2 syster with mechanical throttle it too many tests to get the setting anywhere near right, only on test run with the new syster was necessary to achieve the ch sired result. This was attribute to the much improved consir tency of both the solid stat panel and the new throttl system.
Further tests were now carrie out at lower throttle settings an with no further alteration a ver acceptable and, most importer of all, consistent gearchang was obtained over a very wid range of conditions.
The test vehicle was now pt back in service without an mention being made of the moc ifications that had been carrie out. A complete lack of drivc reaction was taken as a goo sign, as previously there wer consistent expressions of di! satisfaction about performanc of this and other similar vehicic in the fleet.
The results seemed to indical that for a cost of little over E4C Mr Hilditch has brought th Hyndburn AN68 right up to dal on specification and hopefull has increased gearbox life, s reducing down-time on th vehicles.
The components used in th conversion were as follows:
Air Throttle, Williams Air Cor trols type WM4 5 3A an WM388U1C28 obtainable fror Mobile Flownetics Ltd, Unit I Park Street Industrial Estat, Aylesbury, Bucks.
Throttle Cut-off Valve obtainabl from RGS Pneumatics, Accrinc, ton.
Solid State Automatic Transmi sion Panel 8004A obtainabl from Orbit Controls Ltd, Lan; down Industrial Estate, Chelter ham, Glos.