Simple Tests for Fuel Injectors
Page 111
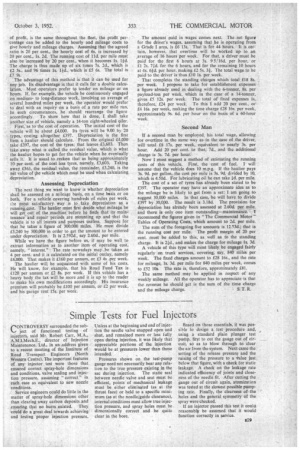
If you've noticed an error in this article please click here to report it so we can fix it.
rONTROVERSY surrounded the sub ject of functional testing of injectors, said Mr. Robert Carr, M.A., A.M.I.Mech.E., director of Injection Maintenance, Ltd., in an address given to a recent meeting of the Institute of Road Transport Engineers (North Western Centre). The important features of any injector test were those that ensured correct spray-hole dimensions and conditions, valve sealing and injection pressure, assuming " correct " in each case as equivalent to new nozzle conditions.
Service engineers could do little in the matter of spray-hole dimensions other than clearing away carbon deposits and ensuring that no burrs existed. They could do a great deal towards achieving and testing proper injection pressure. Unless at the beginning and end of injection the needle valve snapped open and shut, and remained more or less fully open during injection, it was likely that appreciable portions of the injection would be at pressures lower than those intended.
Pressures shown on the test-pump gauge need not necessarily bear any relation to the true pressure existing in the sac during injection. The static seal between needle valve and seat must be efficient, points of mechanical leakage must be either eliminated (as at the thrust face) or held to a specific minimum (as at the needle/guide clearance), internal conditions must allow true injection pressure, and spray holes must be dimensionally correct and be quite clear in the bore.
Rased -on those essentials, it was possible to design a test procedure and, using a standard plain plunger test pump, first to cut the gauge out of circuit, so as to blow through to clear the air from the system. Next came the setting of the release pressure and the raising of the pressure to a dalue just below that figure, with a check for static leakage. A check on the leakage rate indicated efficiency of joints and closeness of the needle fit. After cutting the gauge out of circuit again, atomization was tested at the slowest possible pumping rate. Finally, the clearness of the holes and the general symmetry of the spray were checked.
lf an injector passed this test it coula reasonably be assumed that it would function correctly in service.