ircraft refueller is a bird — C and U not
Page 46
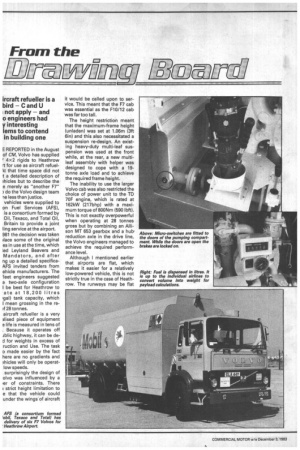
Page 47
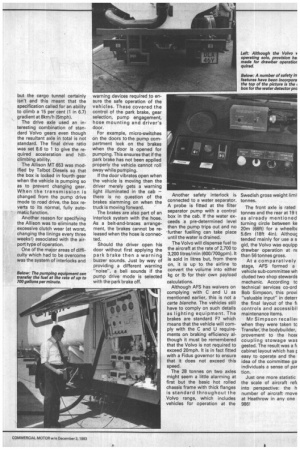
If you've noticed an error in this article please click here to report it so we can fix it.
apply — and o engineers had y interesting lems to contend in building one
E REPORTED in the August of CM, Volvo has supplied 4x2 rigids to Heathrow rt for use as aircraft refuel\t that time space did not t a detailed description of )ificles but to describe the e merely as "another F7" ) do the Volvo design team le less than justice.
vehicles were supplied to on Fuel Services (AFS), is a consortium formed by Oil, Texaco, and Total Oil, Britain to provide a joint ling service at the airport. 981 the decision was taken dace some of the original es in use at the time, which led Leyland Beavers and Mandators, and after ng up a detailed specificaAFS invited tenders from ehicle manufacturers. The 'lee engineers suggested a two-axle configuration I be best for Heathrow to ate at 18,200 litres igal) tank capacity, which I mean grossing in the reif 28 tonnes.
aircraft refueller is a very 3lised piece of equipment e life is measured in tens of . Because it operates off .tblic highway, it can be ded for weights in excess of ruction and Use. The task o made easier by the fact here are no gradients and ?hides will only be operatlow speeds.
surprisingly the design of olvo was influenced by a ier of constraints. There strict height limitation to e that the vehicle could under the wings of aircraft it would be called upon to service. This meant that the F7 cab was essential as the F10/12 cab was far too tall.
The height restriction meant that the maximum-frame height (unladen) was set at 1.06m (3ft 6in) and this also necessitated a suspension re-design. An existing heavy-duty multi-leaf suspension was used at the front while, at the rear, a new multileaf assembly with helper was designed to cope with a 19tonne axle load and to achieve the required frame height.
The inability to use the larger Volvo cab was also restricted the choice of power unit to the TO 70F engine, which is rated at 162kW (217bhp) with a maximum torque of 800Nm (590 lbft). This is not exactly overpowerful when operating at 28 tonnes gross but by combining an Allison MT 653 gearbox and a hub. reduction axle in the drive line, the Volvo engineers managed to achieve the required performance level.
Although I mentioned earlier that airports are flat, which makes it easier for a relatively low-powered vehicle, this is not strictly true in the case of Heathrow. The runways may be flat but the cargo tunnel certainly isn't and this meant that the specification called for an ability to climb a 15 per cent (1 in 6.7) gradient at 8km/h (5mph).
The drive axle used an interesting combination of standard Volvo gears even though the resultant axle in total is not standard. The final drive ratio was set 8.6 to 1 to give the required acceleration and hillclimbing ability.
The Allison MT 653 was modified by Talbot Diesels so that the box is locked in fourth gear when the vehicle is pumping so as to prevent changing gear. When the transmission is changed from the pump drive mode to road drive, the box reverts to its normal, fully automatic function.
Another reason for specifying the Allison was to eliminate the excessive clutch wear (at worst, changing the linings every three weeks!) associated with the airport type of operation.
One of the major areas of difficulty which had to be overcome was the system of interlocks and warning devices required to ensure the safe operation of the vehicles. These covered the control of the park brake, gear selection, pump engagement, hose mounting and driver's door.
For example, micro-switches On the doors to the pump compartment lock on the brakes when the door is opened for pumping. This ensures that if the park brake has not been applied properly the vehicle cannot roll away while pumping.
If the door vibrates open when the vehicle is moving then the driver merely gets a warning light illuminated in the cab — there is no question of the brakes slamming on when the truck is moving forward.
The brakes are also part of an interlock system with the hose. As a belt-and-braces arrangement, the brakes cannot be released when the hose is connected.
Should the driver open his door without first applying the park brake then a warning buzzer sounds. Just by way of providing a different warning "noise", a bell sounds if the pump drive mode is selected with the park brake off. Another safety interlock is connected to a water separator. A probe is fitted at the filter separator pump with a control box in the cab. If the water exceeds a pre-determined level then the pump trips out and no 'further fuelling can take place until the water is drained.
The Volvo will dispense fuel to the aircraft at the rate of 2,700 to 3,200 litres/min (600/700gpm). It is sold in litres but, from there on, it is up to the airline to convert the volume into either kg or lb for their own payload calculations.
Although AFS has waivers on complying with C and U as mentioned earlier, this is not a carte blanche. The vehicles still have to comply on such details as lighting equipment. The brakes are standard F7 which means that the vehicle will comply with the C and U requirements on braking efficiency although it must be remembered that the Volvo is not required to exceed 20mph. It is in fact fitted with a Fidus governor to ensure that it does not exceed this speed.
The 28 tonnes on two axles might seem a little alarming at first but the basic hot rolled chassis frame with thick flanges is standard throughout the Volvo range, which includes vehicles for operation at the The front axle is rated tonnes and the rear at 19 t as already mentioned turning circle between ke 20m (66ft) for a wheelbE 5.6m (18ft 4in). Althouc tended mainly for use a s gid, the Volvo was equipp drawbar operation at tic than 56 tonnes gross.
At a comparatively stage, AFS formed a vehicle sub-committee wh eluded two shop stewards mechanic. According to technical services co-ord Bob Simpson, this provi "valuable input" in deterr the final layout of the ft controls and accessibil maintenance items.
Mr Simpson recallec when they were taken to Transfer; the bodybuilder, provement to the hos( coupling stowage was gested. The result was a ft cabinet layout which has r easy to operate and the idea of the committee ga individuals a sense of par tion.
Just one more statistic the scale of aircraft reft into perspective: the h number of aircraft move at Heathrow in any one 986!