reaking good
Page 33
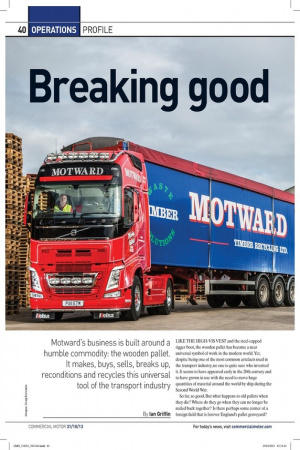
Page 34
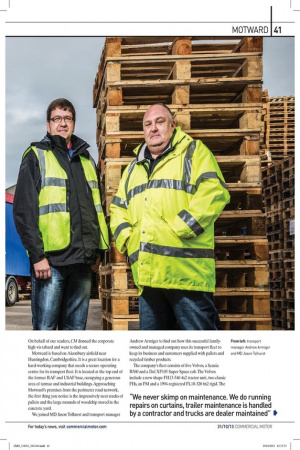
Page 35
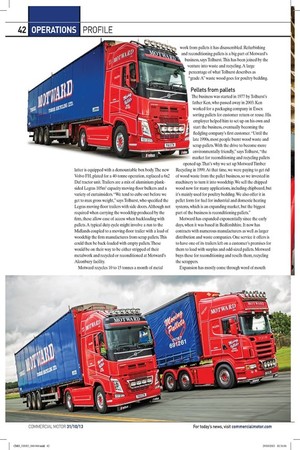
Page 36
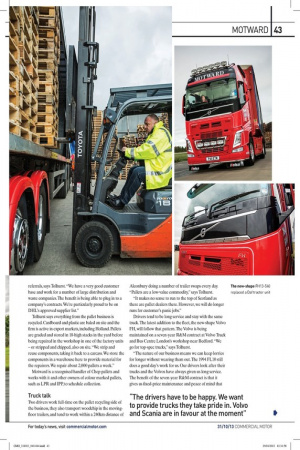
Page 37
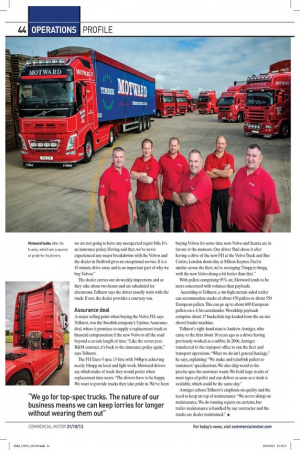
If you've noticed an error in this article please click here to report it so we can fix it.
Motward's business is built around a humble commodity: the wooden pallet. It makes, buys, sells, breaks up, reconditions and recycles this universal tool of the transport industry By Ian Griffin
LIKE THE HIGH-VIS VEST and the steel-capped rigger boot, the wooden pallet has become a near universal symbol of work in the modern world. Yet, despite being one of the most common artefacts used in the transport industry, no one is quite sure who invented it. It seems to have appeared early in the 20th century and to have grown in use with the need to move huge quantities of material around the world by ship during the Second World War.
So far, so good. But what happens to old pallets when they die? Where do they go when they can no longer be nailed back together? Is there perhaps some corner of a foreign field that is forever England's pallet graveyard?
On behalf of our readers, CM donned the corporate high-vis tabard and went to find out.
Motward is based on Alconbury airfield near Huntingdon, Cambridgeshire. It is a great location for a hard-working company that needs a secure operating centre for its transport fleet. It is located at the top end of the former RAF and USAF base, occupying a generous area of tarmac and industrial buildings. Approaching Motward's premises from the perimeter road network, the first thing you notice is the impressively neat stacks of pallets and the large mounds of woodchip stored in the concrete yard. We joined MD Jason Tolhurst and transport manager
Andrew Armiger to find out how this successful familyowned and managed company uses its transport fleet to keep its business and customers supplied with pallets and recycled timber products. The company's fleet consists of five Volvos, a Scania R560 and a Daf XF105 Super Space cab. The Volvos include a new shape FH13-540 4x2 tractor unit, two classic FHs, an FM and a 1994-registered FL10-320 6x2 rigid. The
latter is equipped with a demountable box body. The new Volvo FH, plated for a 40-tonne operation, replaced a 6x2 Daf tractor unit. Trailers are a mix of aluminium planksided L,egras 105m' capacity moving-floor bulkers and a variety of curtainsiders. "We tend to cube out before we get to max gross weight," says Tolhurst, who specified the L,egras moving-floor trailers with side doors. Although not required when carrying the woodchip produced by the firm, these allow ease of access when backloading with pallets. A typical duty cycle might involve a run to the Midlands coupled to a moving-floor trailer with a load of woodchip the firm manufactures from scrap pallets. This could then be back-loaded with empty pallets. These would be on their way to be either stripped of their metalwork and recycled or reconditioned at Motward's Alconbury facility. Motward recycles 10 to 15 tonnes a month of metal work from pallets it has disassembled. Refurbishing and reconditioning pallets is a big part of Motward's business, says Tolhurst. This has been joined by the venture into waste and recycling. A large
percentage of what Tolhurst describes as "grade A" waste wood goes for poultry bedding.
Pellets from pallets
The business was started in 1977 by Tolhurst's father Ken, who passed away in 2003. Ken worked for a packaging company in Essex sorting pallets for customer return or reuse. His employer helped him to set up on his own and start the business, eventually becoming the fledgling company's first customer. "Until the late 1990s, most people burnt wood waste and scrap pallets. With the drive to become more environmentally friendly," says Tolhurst, "the market for reconditioning and recycling pallets opened up. That's why we set up Motward Timber
Recycling in 1999. At that time, we were paying to get rid of wood waste from the pallet business, so we invested in machinery to turn it into woodchip. We sell the chipped wood now for many applications, including chipboard, but it's mainly used for poultry bedding. We also offer it in pellet form for fuel for industrial and domestic heating systems, which is an expanding market, but the biggest part of the business is reconditioning pallets."
Motward has expanded exponentially since the early days, when it was based in Bedfordshire. It now has contracts with numerous manufacturers as well as larger distribution and waste companies. One service it offers is to have one of its trailers left on a customer's premises for them to load with surplus and odd-sized pallets. Motward buys these for reconditioning and resells them, recycling the scrappers. Expansion has mostly come through word of mouth
referrals, says Tolhurst. "We have a very good customer base and work for a number of large distribution and waste companies. The benefit is being able to plug in to a company's contracts. We're particularly proud to be on Dlit's approved supplier list."
Tolhurst says everything from the pallet business is recycled. Cardboard and plastic are baled on site and the firm is active in export markets, including Holland. Pallets are graded and stored in 18-high stacks in the yard before being repaired in the workshop in one of the factory units — or stripped and chipped, also on site. "We strip and reuse components, taking it back to a carcass. We store the components in a warehouse here to provide material for the repairers. We repair about 2,000 pallets a week."
Motward is a recognised handler of Chep pallets and works with it and other owners of colour marked pallets, such as LPR and IPP, to schedule collection.
Truck talk
Two drivers work full-time on the pallet recycling side of the business, they also transport woodchip in the moving floor trailers, and tend to work within a 240km distance of
Alconbury doing a number of trailer swaps every day. "Pallets are a low-value commodity," says Tolhurst.
"It makes no sense to run to the top of Scotland as there are pallet dealers there. However, we will do longer runs for customer's panic jobs."
Drivers tend to be long service and stay with the same truck. The latest addition to the fleet, the new-shape Volvo FH, will follow that pattern. The Volvo is being maintained on a seven-year R&M contract at Volvo Truck and Bus Centre London's workshop near Bedford. "We go for top-spec trucks," says Tolhurst. "The nature of our business means we can keep lorries for longer without wearing them out. The 1994 FL10 still does a good day's work for us. Our drivers look after their trucks and the Volvos have always given us long service. The benefit of the seven-year R&M contract is that it gives us fixed-price maintenance and peace of mind that
we are not going to have any unexpected repair bills. It's an insurance policy. Having said that, we've never experienced any major breakdowns with the Volvos and the dealer in Bedford gives us exceptional service. It is a 45-minute drive away and is an important part of why we buy Volvos."
The dealer carries out six-weekly inspections and as they take about two hours and are scheduled for afternoons, Tolhurst says the driver usually waits with the truck. If not, the dealer provides a courtesy van.
Assurance deal
A major selling point when buying the Volvo FH, says Tolhurst, was the Swedish company's Uptime Assurance deal, where it promises to supply a replacement truck or financial compensation if the new Volvo is off the road beyond a certain length of time. "Like the seven-year R&M contract, it's back to the insurance policy again," says Tolhurst. The FH Euro-5 spec 13-litre with 540hp is achieving nearly lOmpg on local and light work. Motward drivers say which make of truck they would prefer when replacement time nears. "The drivers have to be happy. We want to provide trucks they take pride in. We've been
buying Volvos for some time now. Volvo and Scania are in favour at the moment. Our driver Paul chose it after having a drive of the new FH at the Volvo Truck and Bus Centre, London demo day at Milton Keynes. Fuel is similar across the fleet, we're averaging 75mpg to 8mpg, with the new Volvo doing a bit better than that."
With pallets comprising 95% air, Motward tends to be more concerned with volumes than payloads.
According to Tolhurst, a 4m-high curtain-sided trailer can accommodate stacks of about 470 pallets or about 550 European pallets. This can go up to about 600 European pallets on a 4.5m curtainsider. Woodchip payloads comprise about 17 bucketfuls top-loaded from the on-site shovel loader machine.
Tolhurst's right-hand man is Andrew Armiger, who came to the firm about 10 years ago as a driver having previously worked as a subbie. In 2006, Armiger transferred to the transport office to run the fleet and transport operations. "What we do isn't general haulage," he says, explaining: "We make and refurbish pallets to customers' specifications. We also chip wood to the precise spec the customer wants. We hold large stocks of most types of pallet and can deliver as soon as a truck is available, which could be the same day." Armiger echoes Tolhurst's emphasis on quality and the need to keep on top of maintenance. "We never skimp on maintenance. We do running repairs on curtains, but trailer maintenance is handled by our contractor and the trucks are dealer maintained." •