SAFE, AND SOUND SENS
Page 18
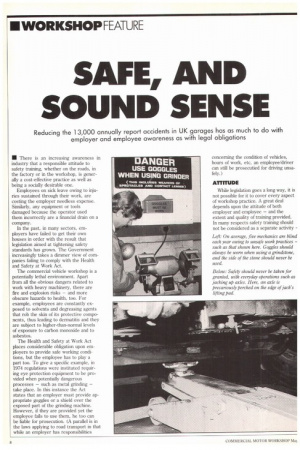
Page 19
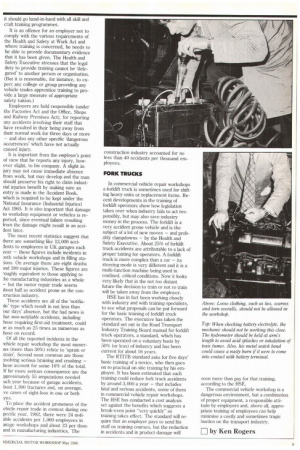
If you've noticed an error in this article please click here to report it so we can fix it.
Reducing the 13,000 annually report accidents in UK garages has as much to do with employer and employee awareness as with legal obligations
• There is an increasing awareness in industry that a responsible attitude to safety training, whether on the roads, in the factory or in the workshop, is generally a cost-effective practice as well as being a socially desirable one.
Employees on sick leave owing to injuries sustained through their work, are costing the employer needless expense. Similarly, any equipment or tools damaged because the operator used them incorrectly are a financial drain on a company.
In the past, in many sectors, employers have failed to get their own houses in order with the result that legislation aimed at tightening safety standards has grown. The Government increasingly takes a dimmer view of companies failing to comply with the Health and Safety at Work Act.
The commercial vehicle workshop is a potentially lethal environment. Apart from all the obvious dangers related to work with heavy machinery, there are fire and explosion risks and more obscure hazards to health, too. For example, employees are constantly exposed to solvents and degreasing agents that rob the skin of its protective components, thus leading to dermatitis and they are subject to higher-than-normal levels of exposure to carbon monoxide and to asbestos.
The Health and Safety at Work Act places considerable obligation upon employers to provide safe working conchdons, but the employee has to play a part too. To give a specific example, in 1974 regulations were instituted requiring eye protection equipment to be provided when potentially dangerous processes such as metal grinding take place. In this instance the Act states that an employer must provide appropriate goggles or a shield over the exposed part of the grinding machine. However, if they are provided yet the employee fails to use them, he too can be liable for prosecution. (A parallel is in the laws applying to road transport in that while an employer has responsibilities concerning the condition of vehicles, hours of work, etc, an employee/driver can still be prosecutied for driving unsafely.) ATTITUDE While legislation goes a long way, it is not possible for it to cover every aspect of workshop practice. A great deal depends upon the attitude of both employer and employee and the extent and quality of training provided. In many respects safety training should not be considered as a separate activity it should go hand-in-hand with all skill and craft training programmes.
It is an offence for an employer not to comply with the various requirements of the Health and Safety at Work Act and where training is concerned, he needs to be able to provide documentary evidence that it has been given. The Health and Safety Executive stresses that the legal duty to provide training cannot be 'delegated to another person or organisation. (But it is reasonable, for instance, to expect any college or group providing any vehicle trades apprentice training to provide a large measure of appropriate safety tuition.) Employers are held responsible (under the Factories Act and the Office, Shops and Railway Premises Act), for reporting any accidents involving their staff that have resulted in their being away from their normal work for three days or more — and also any other specific 'dangerous occurrences' which have not actually caused injury.
It is important from the employee's point of view that he reports any injury, however slight, to his company. A slight injury may not cause immediate absence from work, but may develop and the man should preserve his right to claim industrial injuries benefit by making sure an entry is made in the Accident Book, which is required to be kept under the National Insurance (Industrial Injuries) Act 1965. It is also important that damage to workshop equipment or vehicles is reported, since eventual failure resulting from the damage might result in an accident later.
The most recent statistics suggest that there are something like 13,000 accidents to employees in UK garages each year — these figures include incidents in Doth vehicle workshops and in filling staions. On average there are eight deaths Ind 280 major injuries. These figures are -oughly equivalent to those applying to Ihe manufacturing industries as a whole — but the motor repair trade seems ibout half as accident prone as the con3truction industry.
These accidents are all of the 'notifiaile' type which result in not less than our days' absence, but the bad news is hat non-notifiable accidents, including hose requiring first-aid treatment, could )e as much as 25 times as numerous as hose on record.
Of all the reported incidents in the Thiele repair workshop the most numerals (more than 30%) relate to 'sprain or train'. Second most common are those nvolving serious bruising and crushing — hese account for some 16% of the total.
)f far more serious consequence are the pproximately 55 amputations needed iach year because of garage accidents, bout 1,300 fractures and, on average, ye cases of sight-loss in one or both yes.
To place the accident proneness of the ehicle repair trade in context during one pecific year, 1982, there were 24 notiable accidents per 1,000 employees in arage workshops and about 23 per thouand in manufacturing industries. The construction industry accounted for no less than 40 accidents per thousand emplovees.
FORK TRUCKS In commercial vehicle repair workshops a forklift truck is sometimes used for shifting heavy units or replacement items. Recent developments in the training of forklift operators show how legislation takes over when industry fails to act responsibly, but may also save industry money in the process. The forklift is a very accident prone vehicle and is the subject of a lot of new moves — and probably clampdowns — by the Health and Safety Executive. About 25% of forklift truck accidents are attributable to a lack of proper taming for operators. A forklift truck is more complex than a car — its steering mode is very different and it is a multi-function machine being used in confined, critical conditions. Now it looks very likely that in the not too distant future the decision to train or not to train will be taken away from the employer.
HSE has in fact been working closely with industry and with training specialists, to see what proposals can be put forward for the basic training of forklift truck operators. The executive has taken the standard set out in the Road Transport Industry Training Board manual for forklift truck operators, a standard, which has been operated on a voluntary basis by 50% (or less) of industry and has been current for about 16 years.
The RTITB standard asks for five days' basic training of a novice, who then goes on to practical on-site training by his employer. It has been estimated that such training could reduce fork truck accidents by around 3,000 a year — that includes fatal and serious accidents, some of them in commercial vehicle repair workshops. The HSE has conducted a cost analysis set against the benefits which suggests a break-even point "very quickly" as training takes effect. The standard will require that an employer pays to send his staff on training courses, but the reduction in accidents and in product damage will soon more than pay for that training, according to the HSE.
The commercial vehicle workshop is a dangerous environment, but a combination of proper equipment, a responsible attitude by employers and, above all, appropriate training of employees can help minimise a costly and sometimes tragic burden on the transport industry.
El by Ken Rogers