THE ELECTRO-DEPOSITION OF RUBBER.
Page 60
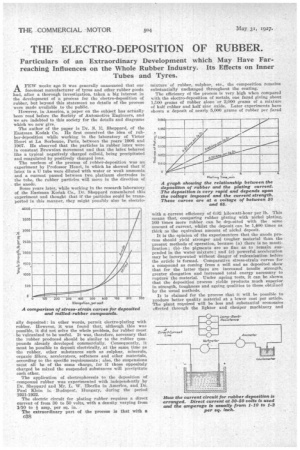
Page 61
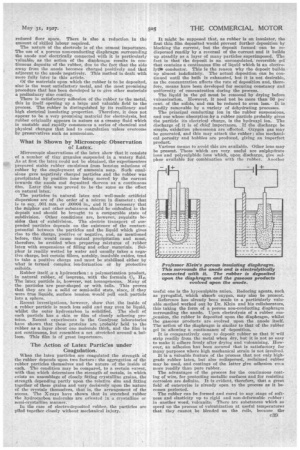
Page 62
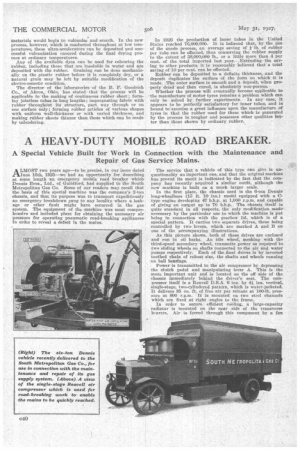
If you've noticed an error in this article please click here to report it so we can fix it.
Particulars of an Extraordinary Development which May Have Farreaching Influences on the Whole Rubber Industry. Its Effects on Inner Tubes and Tyres.
AFEW weeks ago it was generally announced that our foremost manufacturer of tyres and other rubber goods had, after a thorough investigation' taken a big interest in the development of a process for the electro-deposition of rubber, but beyond this statement no details of the process were made available to the public.
However, in America, n, paper on the subject has actually been read before the Society of Automotive Engineers, and we are indebted to this society for the details and diagrams which we now give.
The. author of the paper is Dr. S. E. Sheppard, of the Eastman Kodak Co. He first conceived the idea of rubber-deposition while working in the laboratory of Victor Henri at La Sorbonne, Paris, between the years 1906 and 3907. He observed that the particles in rubber latex were in constant Brownian movement and that the latex behaved like a typical negatively charged colloid, being precipitated and coagulated by positively charged ions.
The nucleus of the process of rubber-deposition was an experiment by Professor Henri, in which he showed that if latex in a TI tube were diluted with water or weak ammonia and a current passed between two platinum electrodes in the tube, the rubber particles will move in the direction of the anode.
Some years later, while working in the research laboratory of the Eastman Kodak Co., Dr. Sheppard remembered this experiment and thought that if the particles could be transported in this manner, they might possibly also be electric ally deposited: in other words, permit electro-plating with rubber. However, it was found that, although this was possible, it did not solve the whole problem, for rubber must be vulcanized to be useful. It was, therefore, necessary that the rubber produced should be similar to the rubber compounds already developed commercially. Consequently, it must be possible to deposit electrically, at the same time as the rubber, other substances such as sulphur, minerals, organic fillers, accelerators, softeners and other materials, according to the specific requirements; also, the suspensions must all be of the same charge, for if those oppositely charged be mixed the suspended substances will precipitate each other, The application of electrophoresis to the deposition of compound rubber was experimented with independently by Dr. Sheppard and Mr. L. W. Eberlin in America, and Dr. Paul Klein in Budapest, Hungary, during the period 1921-1922.
The electric circuit for plating rubber requires a direct current of from 30 to 50 volts, with a density varying from 140 toj amp, per sq. in...
The extraordinary part of the process is that with a
mixture of rubber, sulphur, etc., the composition remains substantially unchanged throughout the coating.
The efficiency of the process is very high when compared with the eleetro-deposition of metals, one farad giving about 1,500 grams of rubber alone or 2,000 grams of a mixture of half rubber and half sine oxide. Later experiments have shown a deposit of nearly 5,000 grams of rubber per farad with a current efficiency of 0.02 kilowatt-hour per lb. This means that, comparing rubber plating with nickel plating, 160 times more rubber can be deposited with the same amount of current, whilst the deposit can be 1,400 times as thick as the equivalent amount of nickel deposit.
It is the opinion of the experimenters that the anode process should yield stronger and tougher material than, the present methods of operation, because (a) there is no mastification; (b) the pigments are so fine as to remain suspended in the water mixture; and (c) powerful acceleration may be incorporated without danger of vulcanization before the article is formed. Comparative stress-strain curves for a compound as coming from a mill and as deposited show that for the latter there are increased tensile strength, greater elongation and increased total energy necessary to rupture the material. Under ageing tests, it can be &hewn that the deposition process yields products much superior in strength, toughness and ageing qualities to those obtained by the usual methods.
It is claimed for the process that it will be possible to produce better quality material at a lower cost per article. The plant required will be less and substantial economies effected through the lighter and cheaper machinery and reduced floor space. There is also a reduction in the amount of skilled labour required.
The nature of the electrode is of the utmost importance. The use of a porous non-conducting diaphragm surrounding the anode and electrically connected with it is particularly valuable; as the action of the dianhraem results in continuous deposits of the rubber, due to the fact that the side away from the anode becomes charged positively and that adjacent to the anode negatively. This method is dealt with more folly later in this article.
Of the materials upon which the rubber is to be deposited, zinc is the most satisfactory metal, and the most promising procedure that has been developed is to give other materials a preliminary zinc coating.
There is satisfactory adhesion of the rubber to the metal, this in itself opening up a large and valuable field to the process. The rubber is distinguished by its resiliency and high electrical insulating properties. Therefore, it does not appear to be a very promising material for electrolysis, but rubber originally appears in nature as a creamy fluid which is unstable and rapidly commences a series of chemical and Physical changes that lead to coagulation unless overcome by preservatives such as ammonium.
What is Shown by Microscopic Observation of Latex.
Microscopic observations of the latex show that it consists of a number of tiny granules suspended in a watery fluid. As at first the latex could not be obtained, the experimenters prepared stable rubber emulsions from benzine solutions of rubber by the employment of ammonia soap. Such etnul&ions gave negatively charged particles and the rubber was precipitated by positive ions being moved by the current towards the encode and deposited thereon as a continuous film. Later this was proved to be the same as the effect on natural latex.
The particles in natural latex and well-made artificial dispeesions are of the order of a micron in diameter : that is to say, .001 mm. or .00004 in., end it is necessary that the Sulphur and other substances should be embodied in the deposit and should be brought to a comparable state of subdivision. Other conditions are, however, requisite besides that of subdivision. The electric transport of suspended particles depends on the existence of the contactpotential between the particles and the liquid which gives rise to the charge, positive or negative, and, as mentioned before, this would cause mutual precipitation and must, therefore, be avoided when preparing mixtures of rubber latex with suspensions of filling and other materials. Sulphur is readily wetted by water and usually takes a negative charge, but certain fillers, notably, insoluble oxides, tend to take a positive charge and must be stabilized either by what is termed complex ion-formation or by protective colloids.
Rubber itself is a hydrocarbon: a polymerization product, in natural rubber, of isoprene, with the formula Ce Hg. The latex particle is, however, not homogeneous. Many of the particles are pear-shaped or with tails. This proves that they are in a solid or semi-solid state, since, if they were true liquids, surface tension Would pull each particle into a sphere.
Recent incetaigations, however, show that the inside of a rubber particle i5 much less solid and may even be liquid, whilst the outer hydrocarbon is solidified. The shell of each particle has a skin or film of closely adhering proteins. Recent experiments in the Goodyear laboratories have shown that these proteins are probably held to the rubber as a layer about one molecule thick, and the film is not continuous, but resembles a net stretched around a balloon. This film is of great importance.
The Action of Latex Partiees under Coagulation.
When the latex particles are coagulated the strength of the rubber depends upon two factors: the aggregation of the rubber particles themselves and the nature of the inside of each. The condition may be compared, to a certain extent, with that which determines the strength of metals, in which exists an assemblage of closely fitting crystalline grains, the strength depending partly upon the relative size and fitting together of these grains and very decisively upon the nature of the crystals themselves, that is, the arrangement of the atoms. The X-rays have shown that in stretched rubber the hydrocarbon molecules are oriented in a crystalline or semi-crystalline manner.
In the case of eleetro-deposited rubber, the particles are piled together closely without mechanical injury. It might be supposed that, as rubber is an insulator, the first thin film deposited would prevent further deposition by blocking the current, but the deposit formed can be redispersed readily by a reversal of the current and it builds up steadily as a layer of many particles superimposed. The fact is that the deposit is an unceagulated, reversible gel that contains a continuous film of liquid which is an electrolyte* conductor. This is the reason why the deposit builds up almost indefinitely. The actual deposition can be continued until the bath is exhausted, but it is not desirable, as the concentration affects the rate of deposition end, therefore, means have been developed for securing constancy and uniformity of concentration during the process.
The liquid in the gel must be removed by drying before vulcanization. However, it need not be more than 50 per cent, of the solids, and can be reduced to even less.It is readily removable by a variety of dehydrating processes.
The principal conducting ion in the rubber suspensions, and one whose absorption by a rubber Particle probably gives the particle its electrical charge, is the hydroxyl ion. The discharge of it is of chief importance. If the discharge be simple, oxidation phenomena are effected. Oxygen gas may be generated, and this may attack the rubber ; also mechanical porosity and bubbles are produced, giving an imperfect product.
Various means to avoid this are available. Other ions may be present. Those which are very useful are sulphydrate ions and polysulphide ions Which, upon discharge, give sulphur available for combination with the rubber. Another useful one is the hyposuiphite anion. Reducing agents, such as pyrogallol, which absorb oxygen, may also be present.
Reference has already been made to a particularly valuable method worked out by Dr. Klein and his collaborators, this taking the form of a porous non-conducting diaphragm surrounding the anode. Upon electrolysis of a rubber sus,pension, the rubber is deposited upon the diaphragm, whilst the gaseous products are evolved upon the anode itself. The action of the diaphragm is similar to that of the rubber gel in allowing a continuance of deposition.
It is comparatively easy to deposit rubber so that it will strip readily from the metal when dry, but it is not so easy to make it adhere firmly after drying and vulcanizing. However, an adhesion has been secured that is satisfactory for many purposes where high mechanical strain is not involved.
It is a valuable feature of the process that not only highgrade rubber latex, but also redispersed, reclaimed rubber may be used, and coatings of the latter give adhesion even more readily than pure rubber.
The advantages of the process for the continuous coating of wire, for protecting metallic surfaces and for resisting corrosion are definite. It is evident, therefore, that a great field of enterprise is already open to the process as it becomes perfected.
The rubber can be formed and cured to any stage of softness and elasticity up to rigid and non-deformable rubber: in another word, vulcanite. There are substances which so speed up the process of vulcanization at useful temperatures that they cannot be blended on the rolls, because the
materials would begin to vulcanize and scorch. In the new process, however, which is conducted throughout at low temperatures, these ultra-accelerators can be deposited and successful vulcanization ensured during the final drying process at ordinary temperatures.
Any of the available dyes can be used for colouring the rubber, including those that are insoluble in water and are deposited with the rubber. Graining can be done mechanically, on the plastic rubber before it is completely dry, or a natural grain may be left by suitable modification of the electro-osmotic condition.
The director of the laboratories of the B. F. Goodrich Co., of Akron,. Ohio, has stated that the process will be applicable to the making of continuous rubber sheet ; forming jointless tubes in long lengths; impregnating fabric with rubber throughout its structure, part way through or on one surface only; forming rubber. articles of various shapes with uniform wall-thickness or with varied thickness, and making rubber sheets thinner than those which can be made by calendering. In 1926 the production of inner tubes in the United States reached 76,000000. It is believed that, by the use of the anode process, an average saving of j lb. of rubber per tube can be effected, thns conserving the rubber supply to the extent of 38,000,000 /b., or a little more than 4 per Cent, of the total imported lust year. .Extending the saving to other products, it is reasonably believed that a total saving of 10 per cent. can be effected.
Rubber can be deposited to a definite thickness, and the deposit duplicates the surface of the form on which it is made. The outer surface is smoth and a deposit, when properly dried and then cured, is absolutely non-porous.
Whether the process will eventually become applicable to -the manufacture of motor tyres remains a problem which can only be solved by further experiments. In any case, it appears to be perfectly satisfactory for inner tubes, and is bound to exercise a great influence upon the manufacture of tyres in that the rubber used for these which is generated by the process is tougher and possesses other qualities better than those shown by ordinary rubber.