GETTING IN THE GROOVE?
Page 13
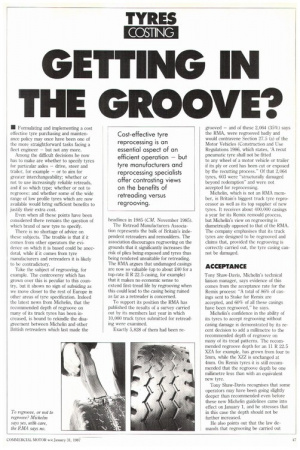
Page 14
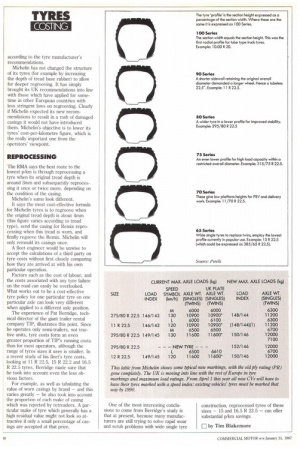
If you've noticed an error in this article please click here to report it so we can fix it.
• Formulating and implementing a cost effective tyre purchasing and maintenance policy may once have been one of the more straightforward tasks facing a fleet engineer — but not any more.
Among the difficult decisions he now has to make are whether to specify tyres for particular axles — drive, steer and trailer, for example — or to aim for greater interchangeability; whether or not to use increasingly reliable retreads, and if so which type; whether or not to regroove; and whether some of the wide range of low profile tyres which are now available would bring sufficient benefits to justify their extra cost.
Even when all these points have been considered there remains the question of which brand of new tyre to specify.
There is no shortage of advice on these subjects. The trouble is that if it comes from other operators the evidence on which it is based could be anecdotal, while if it comes from tyre manufacturers and retreaders it is likely to be contradictory.
Take the subject of regrooving, for example. The controversy which has grown over this is peculiar to this country, but it shows no sign of subsiding as we move closer to the rest of Europe in other areas of tyre specification. Indeed the latest news from Michelin, that the recommended depth of regroove on many of its truck tyres has been increased, is bound to rekindle the disagreement between Michelin and other British retreaders which last made the headlines in 1985 (CM, November 1985).
The Retread Manufacturers Association represents the bulk of Britain's independent retreaders and remoulders. The association discourages regrooving on the grounds that it significantly increases the risk of plies being exposed and tyres thus being rendered unsuitable for retreading. The RMA argues that undamaged casings are now so valuable (up to about 240 for a top-rate II R 22.5 casing, for example) that it makes no economic sense to extend first-tread life by regrooving when this could lead to the casing being ruined as far as a retreader is concerned.
To support its position the RMA has published the results of a survey carried out by its members last year in which 10,000 truck tyres submitted for retreading were examined.
Exactly 5,828 of them had been re
grooved — and of these 2,064 (35%) says the RMA, were regrooved badly and would contravene Section 27.5 (a) of the Motor Vehicles (Construction and Use Regulations 1986, which states, 'A recut pneumatic tyre shall not be fitted to any wheel of a motor vehicle or trailer if its ply or cord has been cut or exposed by the recutting process." Of that 2,064 tyres, 603 were "structurally damaged beyond redemption" and were not accepted for reprocessing.
Michelin, which is not an RMA member, is Britain's biggest truck tyre reprocessor as well as its top supplier of new tyres. It receives about 400,000 casings a year for its Remix remould process, but Michelin's view on regrooving is diametrically opposed to that of the RMA. The company emphasises that its truck tyres are designed to be regrooved and claims that, provided the regrooving is correctly carried out, the tyre casing cannot be damaged.
ACCEPTANCE
Tony Shaw-Davis, Michelin's technical liaison manager, says evidence of this comes from the acceptance rate for the Remix process: "A total of 86% of casings sent to Stoke for Remix are accepted, and 60% of all these casings have been regrooved," he says.
Michelin's confidence in the ability of its tyres to accept regrooving without casing damage is demonstrated by its recent decision to add a millimetre to the recommended depth of regroove on many of its tread patterns. The recommended regroove depth for an 11 R 22.5 XZA for example, has grown from four to 5mm, while the XZZ is unchanged at 4mm. On Remix tyres it is still recommended that the regroove depth be one millimetre less than with an equivalent new tyre.
Tony Shaw-Davis recognises that some operators may have been going slightly deeper than recommended even before these new Michelin guidelines came into effect on January 1, and he stresses that in this case the depth should not be further increased.
He also points out that the law demands that regrowing be carried out according to the tyre manufacturer's recommendations.
Michelin has not changed the structure of its tyres (for example by increasing the depth of tread base rubber) to allow for deeper regrooving. It has simply brought its UK recommendations into line with those which have applied for sometime in other European countries with less stringent laws on regrooving. Clearly if Michelin expected its new recommendations to result in a rash of damaged casings it would not have introduced them. Michelin's objective is to lower its tyres' cost-per-kilometre figure, which is the really important one from the operators' viewpoint.
REPROCESSING
The RMA says the best route to the lowest p/km is through reprocessing a tyre when its original tread depth is around 3mm and subsequently reprocessing it once or twice more, depending on the condition of the casing.
Michelin's sums look different.
It says the most cost-effective formula for Michelin tyres is to regroove when the original tread depth is about 4mm (this figure varies according to tread type), send the casing for Remix reprocessing when this tread is worn, and finally regoove the Rernix. Michelin will only remould its casings once.
A fleet engineer would be unwise to accept the calculations of a third party on tyre costs without first closely comparing how they are arrived at with his own particular operation.
Factors such as the cost of labour, and the costs associated with any tyre failure on the road can easily be overlooked. What works out to be a cost-effective tyre policy for one particular tyre on one particular axle can look very different when applied to a different axle position.
The experience of Pat Berridge, technical director of the giant trailer rental company TIP, illustrates this point. Since he operates only semi-trailers, not tractive units, tyre costs form an even greater proportion of TIP's running costs than for most operators, although the range of tyres sizes it uses is smaller. In a recent study of his fleet's tyre costs, looking at 11 R 22.5, 15 R 22.2 and 16.5 R 22.5 tyres, Berridge made sure that he took into account even the less obvious factors.
For example, as well as tabulating the value of worn casings by brand — and this varies greatly — he also took into account the proportion of each make of casing which was rejected by retreaders. A particular make of tyre which generally has a high residual value might not look so attractive if only a small percentage of casings are accepted at that price. One of the most interesting conclusions to come from Berridge's study is that at present, because many manufacturers are still trying to solve rapid wear and scrub problems with wide single tyre construction, reprocessed tyres of these sizes — 15 and 16.5 R 22.5 — can offer substantial p/km savings.
by Tim Blakemore