Five steps to safety
Page 40
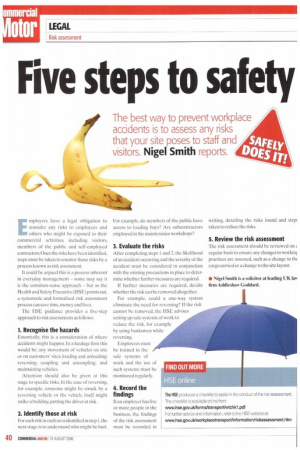
If you've noticed an error in this article please click here to report it so we can fix it.
The best way to prevent workplace accidents is to assess any risks
that your site poses to staff and visitors. Nigel Smith reports.
Employers have a legal obligation to consider any risks to employees and others who might be exposed to their commercial activities, including visitors, members of the public and self-employed contractors, Once the risks have been identified, steps must he taken to counter those risks by a process known as risk assessment, It could be argued this is a process inherent in everyday management — some may say it is the common-sense approach — but as the Health and Safety Executive (HSE) points out, a systematic and formalised risk assessment process can save time, money and lives.
The HSE guidance provides a five-step approach to risk assessments as follows:
1. Recognise the hazards
Essentially, this is a consideration of where accidents might happen. In a haulage firm this would be: any movement of vehicles on site or on customers sites; loading and unloading; reversing; coupling and uncoupling; and maintaining vehicles.
Attention should also be given at this stage to specific risks. In the case of reversing, for example, someone might be struck by a reversing vehicle or the vehicle itself might strike a building, putting the driver at risk.
2. identify those at risk
For each risk in each area identified instep 1 the next stage is to understand who might be hurt. For example. do members of the public have access to loading bays? Are subcontractors employed in the maintenance workshops?
3. Evaluate the risks
After completing steps 1 and 2, the likelihood of an accident occurring and the severity of the accident must be considered in conjunction with the existing precautions in place to determine whether further measures are required.
If further measures are required. decide whether the risk can be removed altogether.
For example, could a one-way system eliminate the need for reversing? If the risk cannot be removed, the HSE advises setting up safe systems of work to reduce the risk, for example by using banksrnen while reversing.
Employees must be trained in the safe systems of work and the use of such systems must be FIND OUT MORE monitored regularly.
4. Record the findings
If an employer has five or more people in the business, the findings of the risk assessment must be recorded in writing, detailing the risks found and step taken to reduce the risks.
5. Review the risk assessment
The risk assessment should be reviewed on regular basis to ensure any changes to workim practices are assessed, such as a change in thc cargo carried or a change to the site layout.
• Nigel Smith is a solicitor at leading UK lav firm Addleshaw Goddard.